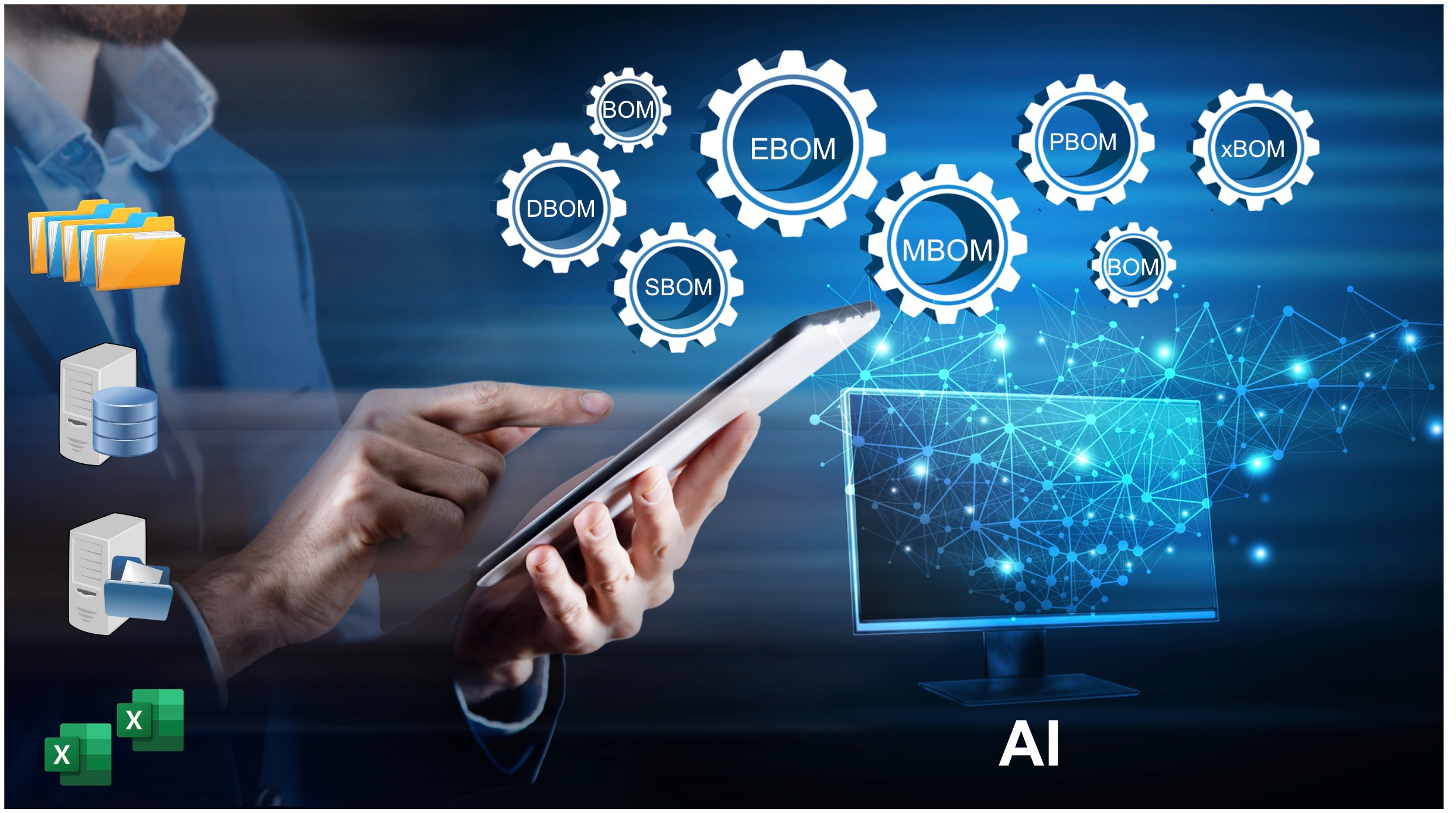
Working in the PLM industry for many years, I learned that BOM is a foundational piece of information systems used by the manufacturing industry – CAD, PDM, PLM, ERP, and many others. A few years ago, I posted my thoughts about BOM data management evolution where I mostly discussed technical aspects of how BOM-like data can be managed in modern enterprise systems.
But technology is not everything. Enterprise applications live in a complex business and human ecosystem driven by multiple factors starting from people’s habits, legacy systems, controls and politics, and technological advancements. How to connect all these things together? A few days ago, my attention was caught by Jos Voskuil’s – The Rise and Fall of BOM article which speaks about the historical importance of BOM and rising of software development, which becomes an inseparable element of modern products.
I think it is time to zoom out and think about BOM management and how it will be in the future.
The Inspiration – Digital Transformation of Driving Process
Think about the driving process as we know it now and the way it existed 40 years ago. Zoom out into this process and think about transformations. It was not a single step and it took multiple efforts of many companies developing different technologies and products to make it happen.

The result is what we have today – intelligent and smart navigation systems that are also augmented into cars to provide a seamless driving experience and self-driving capabilities. You can see a 40 years distance between these pictures.
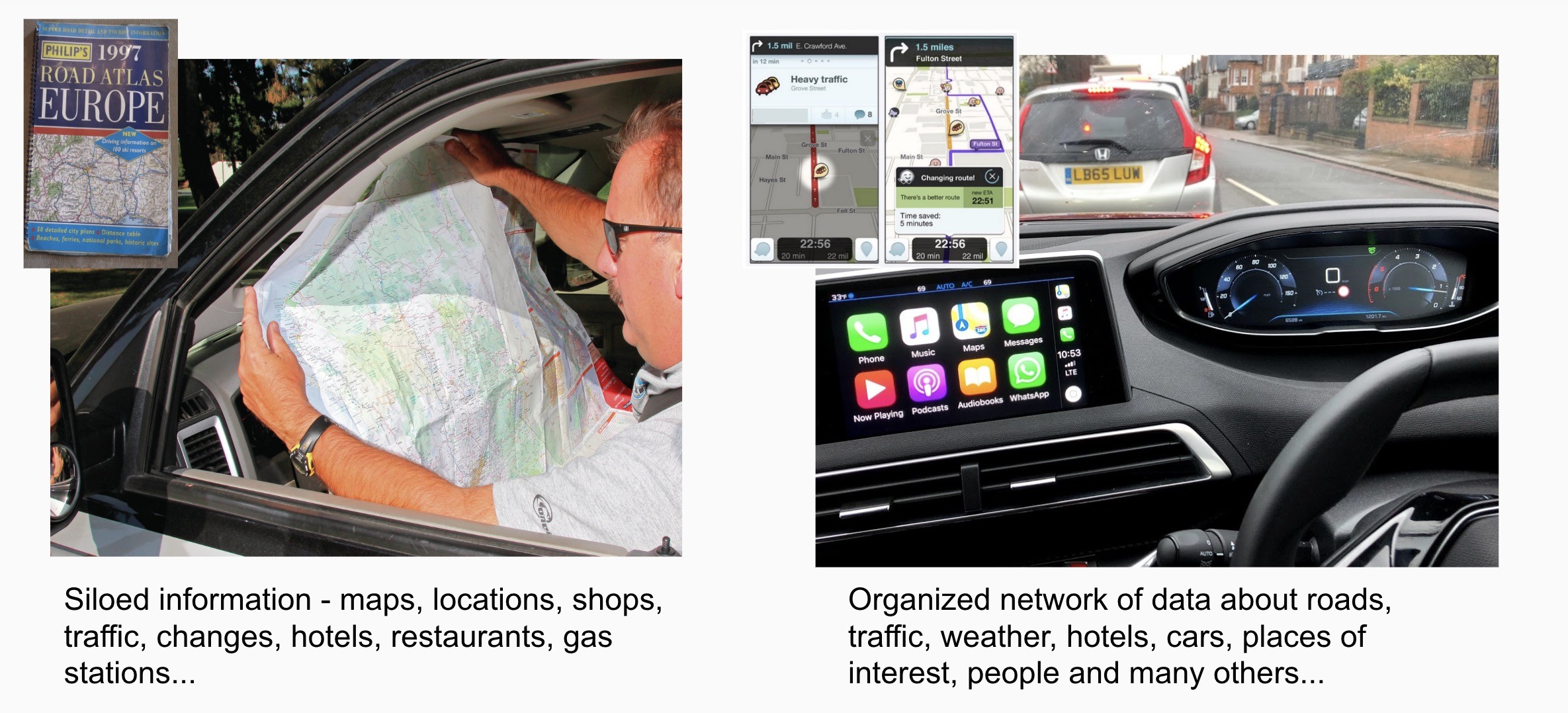
In my article today, I want to share my thoughts on the perspective of the future development of BOM management technologies and systems that will become part of future engineering and manufacturing platforms.
The History of BOM Management Is Still Around Us
Bill of Materials goes back in time many decades. You can find the first Bill of Materials back on the corkboards and CAD drawings. It is important to understand your past to predict the future. Things are changing, but not as fast as we might want them to be. I want to start my article with BOM history. Although, this is live history. The solution I will talk about below is still around us in a variety of forms and legacy systems.
BOM in MRP
The roots of all BOM management and single bill of materials in every manufacturing organization are coming back to the foundation of MRP systems. A bill of materials (BOM) is a critical component of a manufacturing resource planning (MRP) system. It is a list of all the materials and components that are required to manufacture a finished product. There are several reasons why BOM is important for MRP: Planning and Scheduling, Costing, Quality Control, and Traceability.
Nevertheless, BOM in MRP systems is often limited to specific functions of MRP. Therefore MRP BOM is not very useful for engineering functions. Read 5 Books To Start Your BOM Management Education to learn more. Inventory management was a core element of MRP, therefore, it was good for manufacturing BOM and supply chain management, which later became part of ERP solutions.
BOM in Drawings
Bill of Materials (or Part lists) in engineering was a long time before the PLM system even existed and it was a list of parts required in every engineering drawing. There are several standards that required part lists in drawings. Among them, ASME Y14.5 defines the practice of including a bill of materials (or part list). The BOM typically lists all the parts or components required for the assembly, including part numbers, quantities, and descriptions. In electronic and electrical engineering, the IPC-2581 standard provides some guidelines for manufacturing data and documentation, including the use of a parts list that specifies the assembly components. Similar requirements can be found in architecture, construction, HVAC, and electrical drawing for construction. All CAD packages provide support to create part lists and bills of materials. For many engineers, it is the first place where they meet BOMs.
BOM in PDM
PDM was born to manage CAD files. Therefore, the system usually provided very poor capabilities to manage bills of materials. PDM was managing product data in the way CAD files (later design or cloud documents), but never became a place to manage bills of materials except for supporting simple lists of parts based on CAD files. Some PDM systems provided a decent integration between PDM and drawing BOM management, which is largely used today. This is probably the mainstream BOM solution for all small and medium size companies. And it is a root cause of a lot of inefficiencies in data management.
BOM in PLM: EBOM, Multi-BOM, Enterprise BOM, and Multi-View BOM
Product lifecycle management (PLM) systems became the first place where the core foundational data model was focused on how to manage Items and BOMs. The most successful PLM systems for the past 25+ years were placing BOM management as a foundation of their technological platforms. Agile PLM, MatrixOne, Aras, Teamcenter, Windchill, and many others. All these systems were a great place to manage EBOM (engineering BOM) and its lifecycle. The model was evolving to absorb multiple aspects of BOM management needed in industrial companies. As such, we created EBOM (engineering BOM) and MBOM (manufacturing BOM). It became a continuous place for a battle between PLM and MRP/ERP systems for control of the BOM management and change process. Later, the concept of enterprise BOM management came out with the ability to manage multiple BOMs (EBOM, MBOM, SBOM, PBOM, etc) and finally came to the idea of xBOM. The recent PLM ideas and research is offering a multi-view BOM, which is important because it is the last PLM step before stepping into a full digital BOM.
Navigating the Simplicity and Complexity of BOM Management
Ask 3 engineers about something and you might end up with 4 and more opinions. The same is true about BOM management. For some people, BOM is simple – it is a list of components (or part list), which represents the recipe of the product. For some other people, BOM management is a complex discipline that is a foundation of product lifecycle management and one of the main sources of information for engineering, production planning, and supply chain.
Here is my reality check – it doesn’t matter what side of the BOM management process you represent, for every manufacturing company, BOM in all its forms represents one of the most critical elements of information about a product, about how it is designed, how it built and reflects on what customers can do with the product including the requirements for maintenance and sustainability.
BOM – Engineering Experience
For many years, BOM was one of the “outputs” of engineering and design activities. Every engineering department was responsible to produce a BOM before passing their work downstream. For the majority of manufacturing organizations, this is what is happening now.
However, the challenges of product development, increasing complexity, and the need for speed and collaboration bring more and more questions to product development about how to bring digital technologies into the engineering process, to automate manual processes of BOM management. Read more about it in my article – Rev Up Your NPD Process: How New PLM Can Speed Up Your Engineering Processes.
BOM – MRP, ERP, and Enterprise Experience
BOM is a foundation of material resource planning. From that standpoint, nothing changed for the last 20+ years. MRP function requires BOM and every company needs to feed MRP with the data. This process is tedious and complex. The challenges of this process are related to bad communication between departments, the complexity of manual processes, and the complexity of the data. But BOM is needed for resource planning, supply chain management, maintenance, and many other activities. For most of these parts, MRP BOM is struggle to provide a balanced solution. Configurable products, complex supply chain, demand for sustainability. Companies are more and more looking at how to bring PLM and more specialized systems such as Sales configurations, CPQ, MRO, and many others to support the complexity of enterprise BOM management.
BOM – Software Experience
The importance of software BOM is on the rise. The need for transparency and accountability in the supply chain is one of the main factors. A software BOM is a list of all the software components that make up a particular product or application, including third-party libraries and open-source software, along with their version numbers, licenses, and dependencies.
You have software everywhere these days. Your car, home appliance, and many other products around us are filled with software. It becomes more pervasive and critical to business operations, and it also becomes more susceptible to security vulnerabilities and compliance risks. A software BOM helps to mitigate these risks by providing complete visibility into the software components used in a product, making it easier to identify and manage vulnerabilities and dependencies.
Since Software BOM is so important, it cannot be isolated anymore from other engineers involved in product development. With a clear and accurate software BOM, development teams can better coordinate and manage their work, while stakeholders such as product managers and quality assurance teams can ensure that the product meets their requirements and specifications.
Regulators are increasingly interested in software BOMs. For example, the US National Telecommunications and Information Administration (NTIA) has recommended that software BOMs be included in the Software Bill of Materials section of Internet of Things (IoT) devices, and the European Union’s General Data Protection Regulation (GDPR) requires organizations to maintain an inventory of all data processing activities, including those related to software components. Check my articles:
Software BOM and what is the path toward an open shared digital ingredient library
How to combine engineering and software BOMs
The importance of software BOM for hardware security
Software BOM: 3 Reasons why manufacturing companies need to start managing SBOM in 2021
BOM in Excel and Spreadsheets
This topic has a special place in my heart. Because every manufacturing company in the world I will come to, I will see how companies are using some form of spreadsheet to manage bills of materials and product information. It is one of the most widely used solutions. You can see it used by a small company with 2 engineers and Fortune 500 organization managing a supply chain using Excel.
I wrote tons of articles about the topic of Excel and spreadsheet BOMs. Check some of them.
The secret to why engineers are using Excel instead of PLM tools was finally revealed
Digital transformation, engineers and Excel paradox
BOM Management: Between Excel and Enterprise PLM
The presence of Excel represents the biggest opportunity for industrial companies to organize information and transform business processes from “Excel documents” to a new digital infrastructure. Let’s talk more about it.
BOM and Digital Transformation
The industry experts and vendors are in full agreement that digital transformation starts from BOM management transformation. If you’re not convinced. check some of the articles. I cherry-pick some of them for you, but please use Google or other tools to find more.
I like the new term offered by CIMdata – Bill of Information. Read Peter Bilello’s article – The Bill of Information is Vital for Digital Transformation. PTC’s white paper – Digital Transformation Starts with BOM management. Another great article Enable Digital Transformation with Digital BOM by Jim Brown of Tech-Clarity. One more – Why Poor BOM Management Slows Down Your Digital Transformation.
Digital transformation starts with digital information. In our case, it is a digital BOM.. Manufacturing companies should lay down a healthy data foundation for their digital transformation efforts. Such an element of data foundation creates digital records for your product which is an essential part of digital product development. Relying on Excel, spreadsheets, and drawing tables can give you an illusion that “work is done”, but eventually will lead to mistakes, additional costs, and delays.
Models – From Excel Documents To Digital Information
It is absolutely important to get rid of Excel (or any other forms) as a foundation of BOM and product data sources. By sourcing your Excel files in SVN or cloud disks, you won’t be able to digitally transform your processes. What is needed is a specialized system capable to manage information records, ensuring data is referenced and connected, relationships are managed in a proper manner, and providing a single source of truth about product data. The service to do so can come from any software vendor, but it is important to ensure that together with the capabilities to manage product information, you can manage the complexity of modern products as well as make this information available to everyone. Data is becoming more important than applications. This is where I can envision a future conversation from the “application” paradigm to the “information” paradigm. We will see a data-driven PLM approach and future conversion into intelligent web services, systems of engagement, and systems of intelligence approach.
Knowledge Graphs
A knowledge graph is a data structure that represents information as a network of interconnected entities, where each entity is represented as a node and each relationship between entities is represented as a link or edge. Knowledge graphs are designed to capture and organize complex relationships and dependencies between different pieces of information, enabling more efficient and effective data analysis, search, and discovery.
Knowledge graphs can be used to represent various types of information, such as facts, concepts, events, and entities from various domains such as medicine, finance, or entertainment. They can be built using various techniques, including natural language processing, machine learning, and semantic web technologies.
For the last decade, knowledge graphs have had a wide range of applications, such as in search engines, recommendation systems, and chatbots. For example, Google’s Knowledge Graph is used to enhance search results by providing information about entities and their relationships, such as the relationship between a famous person and their works, their date of birth, and their profession.
I wrote about Knowledge Graphs in the past. Check my earlier articles. I expect Knowledge Graph technologies to provide valuable technology to build a future of digital BOM and data modeling for PLM and other enterprise applications for engineers and manufacturing.
Multi-Tenant Data and Process Management
All legacy ERP and PLM systems have one thing in common. They were developed at a time when no one was really thinking about networks. Every company was a “king” and all data management solutions were focused on how to provide a better platform to serve a single company, centralize the data and upsell better applications to manage processes. That was the main concept and the paradigm of many PDM, PLM, and ERP systems available for the last 20+ years.
And the existing paradigm is changing in front of our eyes. Companies are not functioning alone anymore. They are involved in a complex set of relationships, communicating with a complex network of suppliers, contractors, customers, sales, and service facilities. Enterprise resource planning and material requirements planning is not isolated functions anymore. Internal operations cannot solely focus on internal focuses and processes- everything is intertwined and operates as one huge network.
As a result, modern PLM and other platforms require a function of multi-tenancy. In short, the ability to serve multiple companies on a single platform. Together with increased demand for openness and communication, multi-tenancy is quickly becoming a de-facto mandatory requirement for all engineering and manufacturing applications.
GPT, LLM, and Generative AI
One of the hottest topics for the last 100 days, ChatGPT was open the world of Generative Pre-trained Transformer, which is a type of language model (LLM) developed by OpenAI. It is an artificial intelligence system that uses deep learning techniques to generate human-like text based on a given prompt or context. The GPT model is trained on a large corpus of text data, such as books, articles, and websites, using unsupervised learning techniques. This means that the model learns to identify patterns and relationships in the text data without explicit guidance or supervision.
Once trained, the GPT model can be used for a wide range of natural language processing tasks, such as text generation, translation, summarization, and question-answering. The model generates text by predicting the most likely next word or sequence of words based on the input prompt and the context learned from the training data. GPT has become widely used and well-known due to its impressive language generation capabilities, particularly with the release of GPT-3, which has over 175 billion parameters and can generate a wide range of text, including coherent paragraphs, articles, and even creative writing such as poems and stories.
It opens the opportunity for Generative AI, which is a door to introduce a better way to predict what the right product design and planning options could be to use it in a variety of tasks related to new product design product data management, supply chain, and many other decisions. Read about it in my previous articles:
Future PLM AI Advancement – GPT, Large Language Hybrid Models and Copilots
PLM, Chat GPT and Large Model Thoughts
Conclusion
In my view, we are standing in front of a big transformation in the way manufacturing companies are running their business, developing new products, and supporting their customers. The new digital experience will be different from what exists now. but it won’t happen overnight. It is like we didn’t switch from paper maps to modern digital navigation systems, the same will not happen with digital manufacturing. Digital Bill of Materials will play a key role in making future manufacturing intelligent. Just my thoughts…
Best, Oleg
Disclaimer: I’m co-founder and CEO of OpenBOM developing a global digital thread platform providing PDM, PLM, and ERP capabilities and new experience to manage product data and connect manufacturers, construction companies, and their supply chain networks. My opinion can be unintentionally biased.