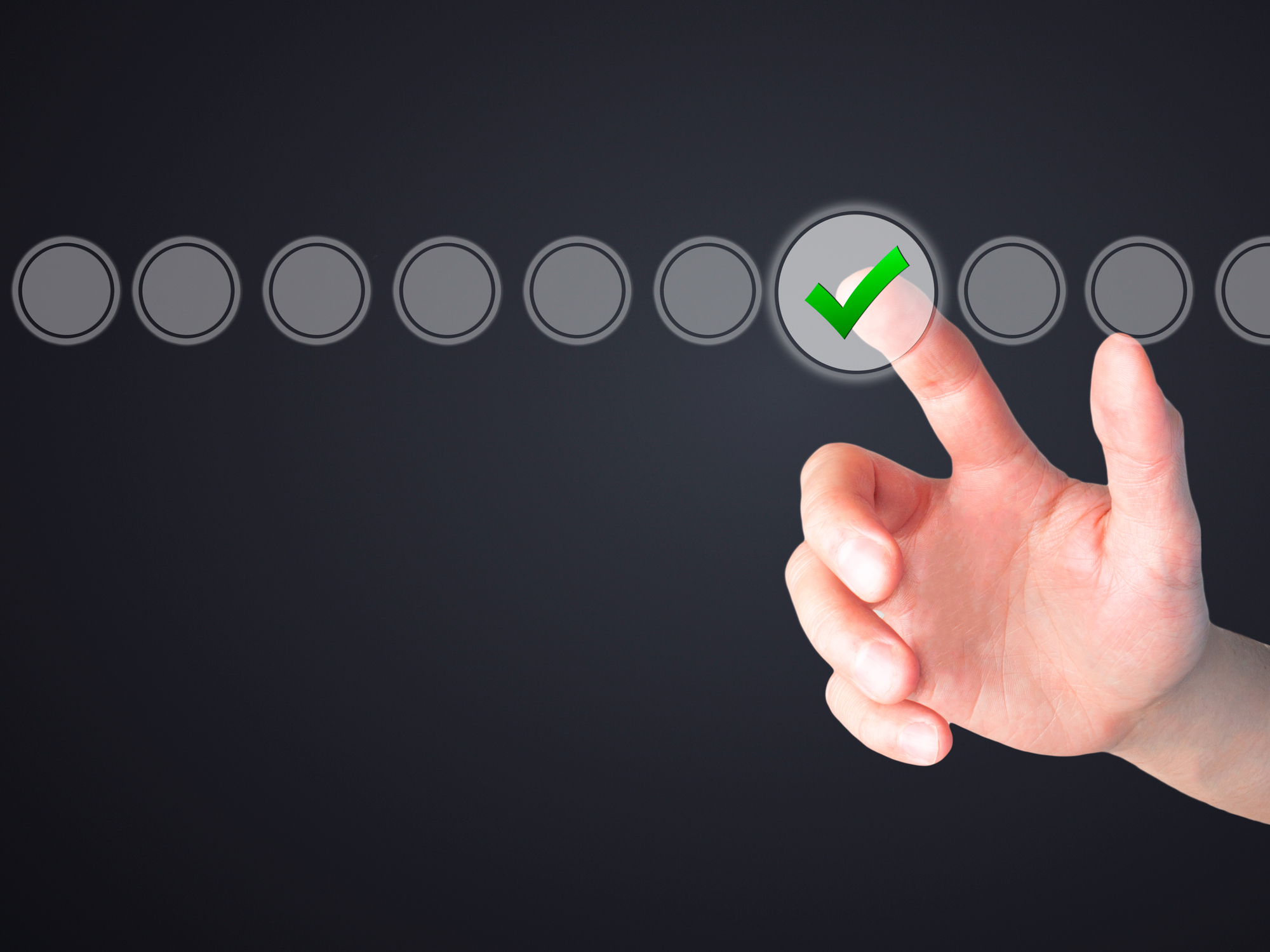
You cannot modern products using outdated and old technologies. Designing and building products is a complex process and you better make the right choice about how to manage the product life cycle. In today’s rapidly evolving manufacturing world, technology plays a pivotal role in shaping the success and growth of industrial companies. The importance of the right choice when selecting product lifecycle management (PLM) software cannot be overstated, because it directly influences efficiency, productivity, and the ability of engineers and a company to perform needed tasks. Therefore the strategic technological choice is important.
Why PLM choice is different in 2023?
PLM technology was always a hard thing to choose for an industrial company. Because of the PLM roots going deep into CAD file management, for many years, PDM was a usual starting point for PLM technology selection. While it is still a natural path for many engineering teams and manufacturing companies, there are two main reasons why your organization needs to think about PLM technology differently in 2023:
- Product Complexity
- Variety of SaaS tools and cloud technologies
In the past, most companies were starting PDM/PLM technology selection from a single CAD system (usually MCAD). Everything else was an afterthought. These days products are complex including mechanical, electronics, and software. The process to support product development can be different than selecting a platform to manage CAD files. Distributed way to manage product development process located in multiple places brings new requirements for product lifecycle management, product data management, and supply chain management. Which defines different priorities for PLM technological platform choice.
SaaS tools are another reason why technological choices can be different. Even though many CAD systems today are still desktop, we can see a growing presence of cloud tools, hosted systems, cloud storage, and a variety of technologies and tools allowing you to support distributed nature of work using tools available as cloud services and via subscription.
Check for your organization before choosing a technological platform
In the past PLM (or even PDM) was a selection done by engineers (or engineering department). While it is still the way most organizations are focusing even today, I often recommend stopping and thinking about organizational choices and the number of people involved in product development processes. It will help you to make a better decision about PLM technological selection. Check the diagram below that can give you some ideas about PLM technological challenges in different organizations.
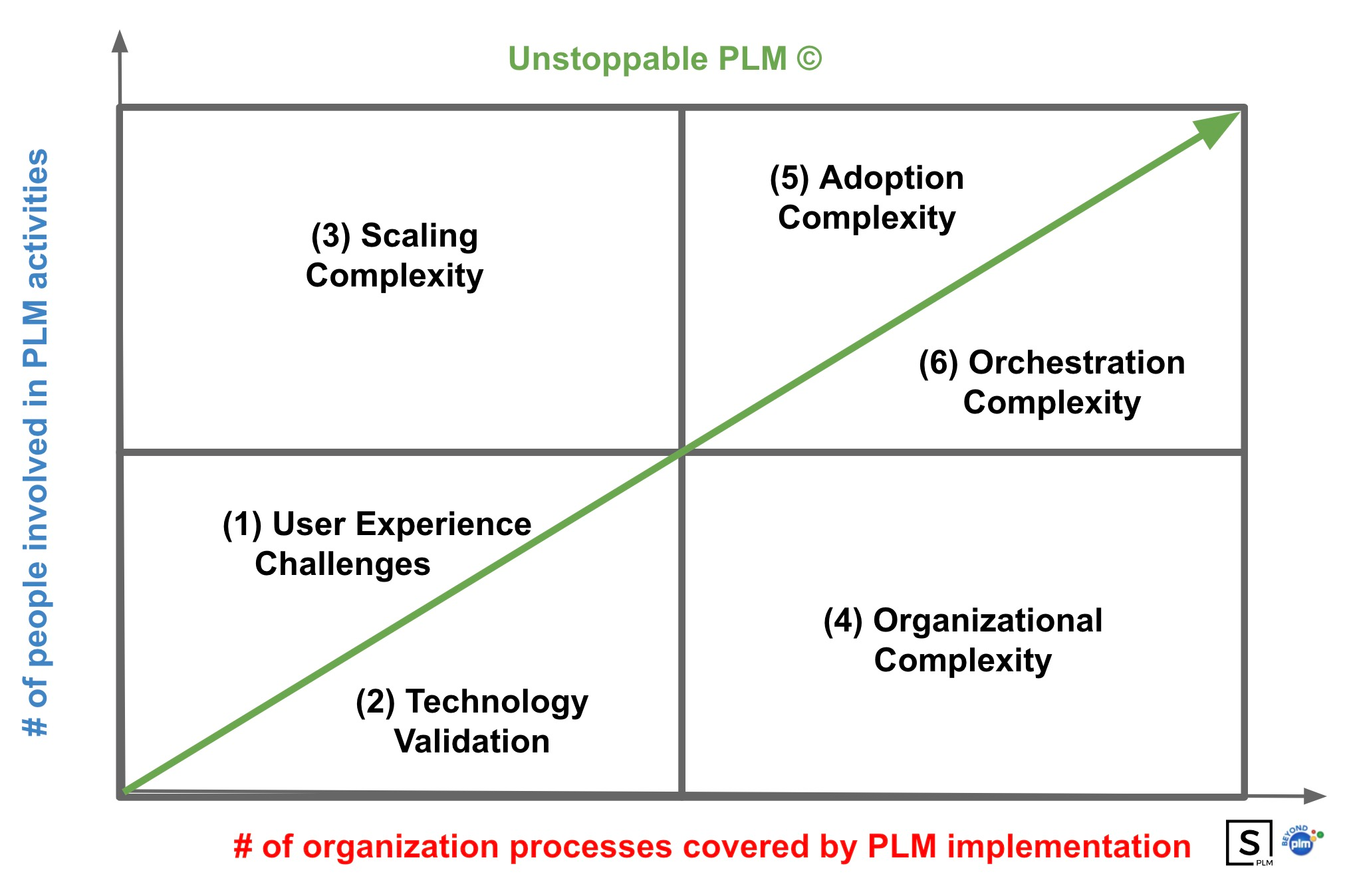
I defined 6 levels of complexity for PLM software implementations depending on company size and number of processes. You should be thinking about them while deciding what platform to use. I often can see how small organizations are looking into complex PLM platforms (as a proven technology), but missing the point of complexity level they need to overcome to implement it for a small organization. The opposite is also true – the system tailored for a small organization can fail to support needed governance for large-scale enterprises.
Another aspect of technology decision is related to the decision to work with one or multiple systems. While large enterprise organizations usually decide to get multiple systems and integrate them together, for smaller organizations, it can be a bad idea, and the selection of a system with a smaller number of functions, but integrated processes can be a better choice.
10 Criterias of PLM Technology Selection
After many years of helping manufacturing companies to decide what PLM technology to use, I come down to these 10 points of criteria selections every company needs to follow when making a decision about PLM systems and technological platforms:
- Functionality: Decide what functions you need. Don’t focus on what the system provides but think about what your team needs to do (eg. manage files, manage BOM, work with contractors, suppliers, etc.). Come down with the list and check with providers.
- Integration: Ensure that the PLM system can integrate seamlessly with your existing software infrastructure, such as CAD tools, ERP systems, and other critical business applications.
- SaaS vs. Hosted vs On-Premises: While I’d be carefully deciding about anything that is not cloud-based these days, make a check based on the first two criteria. Cloud systems can remove a lot of the pain of managing, servicing, and updating systems. But, if the cloud system doesn’t integrate with your CAD systems, the value of this cloud system can be very diminished.
- User-Friendly Interface: Some systems (especially old ones) are terrible with user experience. Keep it in mind when deciding on “proven” industry leaders. The same can be said about some unproven out-of-the-box cloud or SaaS tools. Ask for a trial. If a vendor doesn’t give you a trial, it might be a showstopper in 2023. Keep in mind, PLM tech is not only for engineers. Everyone in the company will be able to use it.
- Security: PLM systems handle sensitive product data, so robust security features are essential to protect intellectual property and sensitive information. Check for some acceptable frameworks, infrastructure and check company processes. Security is a process, so it is important to understand how vendors manage it.
- Vendor Reputation: Research the vendor’s reputation, customer reviews, and track record in providing PLM solutions. G2 PLM Grid is a good place to check in 2023. Check customer stories and contact real customers to talk about the solutions.
- Scalability: Consider the future growth and expansion of your organization, and choose a PLM system that can accommodate your evolving needs.
- Customization and Flexibility: Assess whether the PLM system can be customized to match your specific workflows and requirements. Be aware of the out-of-the-box SaaS tools and “hosted PLM” systems without the capabilities to change the data, administration flexibility, and API access.
- Support and Training: Check the level of support and training provided by the vendor to ensure a smooth implementation and ongoing usage. PLM Onboarding training with the ability to help your company to adopt the technology is important.
- Cost and ROI: Evaluate the total cost of ownership (including licensing, implementation, maintenance, and support) and compare it with the expected return on investment. Don’t buy “future awesomeness”, but make the real calculations of what you need today.
Bonus Point – Data Portability
This one is very critical. Every business must take responsibility for its data. Data is more important than applications in 2023. Check what will happen when you decide to switch to another tool. How easy to get data out and make a switch? Don’t believe promises, but check what is the process of data export and how all your data can be easily saved outside of the PLM tech platform.
What is my conclusion?
Selecting PLM technology is a complex process. To make the right choice, you need to start with people, organization, and process in mind. Checking what your goals are and only after, to come decisions about technology, how to manage data you have in an organization, and integrate with other processes and tools. These days, SaaS and cloud technologies make the PLM platform available for trial and evaluation. Check for customer feedback. Unlike what happened 10-15 years ago, when PLM must be installed on premises and implemented by an advanced service team, modern PLM platforms can be tested and evaluated before a decision will be made. In a modern information-driven world, it is a must to check references and reviews, don’t stop on marketing presentations and ask for a trial of any technology you want to use and check it first hand. Just my thoughts…
Best, Oleg
Disclaimer: I’m co-founder and CEO of OpenBOM developing a digital thread platform including PDM/PLM and ERP capabilities that manages product data and connects manufacturers, construction companies, and their supply chain networks. My opinion can be unintentionally biased.