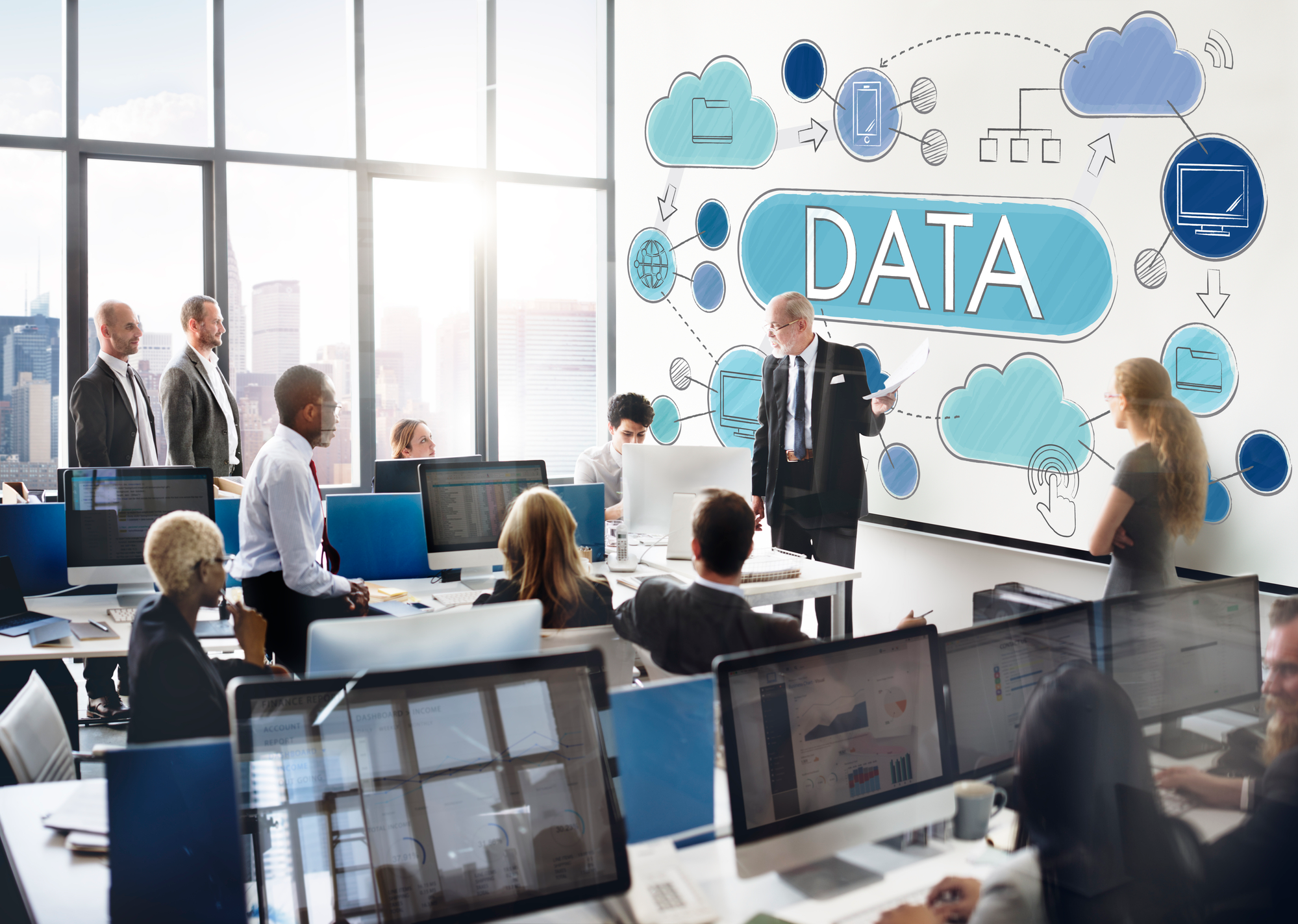
In the rapidly evolving landscape of industrial processes, the digital transformation has become a pivotal focus. This shift demands a reconsideration of how Product Lifecycle Management (PLM), Enterprise Resource Planning (ERP), and other systems manage data. One of the approaches I touched recently in my articles is related to buiilding a modern and robust product mode.
I want to talk about what can be a transition between existing practice and models to a novel digital BOM approach. My attention was caught by Lateef Khan post speaking about multiple BOMs – EBOM, MBOM, BOE, BOP… I found the questions asked in the past very typical in the current PLM practice and planning- how to organize multiple BOMs. Here is the passage:
When considering how to design and architect your BOMs in an enterprise PLM system, there’s a lot to consider and unpack. As you think through business processes and details about your product design & manufacturing, you need to weigh in on the overhead of your vs business value gained from having separate bom views as you architect your data model.
When I consider separation of my EBOM vs MBOM, it’s important to assess what all the differences might be. For example, packaging like boxes, crates, tape, pallets to labeling to bom line quantities, are all things but not limited to that could be different or additional in an MBOM in comparison with an EBOM. From a design perspective, if my design engineers and manufacturing engineers collaborate often and frequent, having a single BOM could also be effective enough. However if your processes are more siloed, your functions have limited collaboration resulting in structure differences, and you have unique child items to manage in manufacturing versus what’s included in engineering, then having a separate EBOM and separate MBOM may be the way to go.
However, the most important question is the following one:
Digitization of your MBOM, BOE & BOP from a data model and process perspective also enables the opportunity to build your digital thread. Once you’ve established these digital views in their system of record, you’re now ready to transfer them to its system of reference. For example sending the MBOM to the ERP plants and sending the BOP to the MES to execute the recipe defined. Transition to this digital representation and process is a very large undertaking and paying particular attention to your business transformation and deployment strategy is critical.
The question raised in this post is very important. Traditionally, industries have relied on multiple Bill of Materials (BOMs) – including the Engineering BOM (EBOM), Manufacturing BOM (MBOM), Bill of Process (BOP), and Bill of Equipment (BOE). However, the question arises: what is the next step in this evolution?
Limitations of the Traditional xBOM System
Historically companies were building a “single BOM” which was usually stored in MRP/ERP system. Back in those days, the BOM was either in MRP or on engineering drawing (called Part List). Some of my avid readers always remind me that BOM is MRP and engineering just need to release drawings. The evolution of this system as well as brining PLM and some other systems triumphed a traditional xBOM system with siloed data model prevalent in enterprise systems.
In this model, customers are oriented towards documents and perceive product information through the lens of multiple BOMs. This approach, while familiar, has inherent limitations. It often leads to data redundancy, inconsistencies, and challenges in maintaining synchronization across different departments. Although, it is still the mainstream model used by most of PLM vendors, it has many disadvantages. The siloed nature of this model hinders the seamless flow of information, thereby impacting efficiency and adaptability.
The Shift Towards a Holistic Product Model
What can be a better approach then xBOM model? The adoption of modern data management technologies can bring a better model than BOM structure (known as xBOM). What modern systems architecture advocate is a development of newholistic digital product model. Check my earlier article for more information.
This model is enriched and capable of encapsulating multiple facets of product information – spanning requirements, engineering, manufacturing, and maintenance. A holistic product model fosters a unified view of the product lifecycle, enabling better coordination and integration across various stages. This approach streamlines processes, reduces errors, and enhances the overall efficiency of product management.
The technological foundation of such a model can be a graph model, which can provide a robust representation of multiple data assets and creating a flexible set of relationships. Product knowledge graph is a way to take PLM development and bill of materials data model from siloed engineering bill, manufacturing bill, service and maintenance all together to moderl engineering and product development process combined with production process and rest of lifecycle stages to present an accurate BOM all way down from requirement to maintenance.
BOM as a Process Bridge
In the realm of modern industry practices, the BOM is not just a structure (eBOM, mBOM, sBOM, etc), but it is a dynamic view and a bridge into a world of processes. In such a model each BOM is a “view” from a holistic product model. A graph model connects various aspect of product data and production process into a single whole, while providing each process its own view of a BOM (xBOM views).
Each process within the product lifecycle can access a subset of data from the BOM to perform necessary tasks. This perspective transforms the BOM from a mere list of parts to a dynamic tool that facilitates process integration and data-driven decision-making.
The Rise of Digital Twins and Digital Threads
The advent of modern data management technologies, particularly graph models, paves the way for robust product models. These models are instrumental in creating digital twins and digital threads of products. Digital twins enable the virtual representation of physical products, offering insights into performance and potential issues. Similarly, digital threads provide a continuous data flow across the product lifecycle, enhancing traceability and real-time monitoring. These technologies mark a significant stride towards intelligent and interconnected industrial systems.
What is My Conclusion?
Transitioning from separate data silos (bill of materials) to a holistic product model addresses the challenges associated with managing and synchronizing multiple BOMs. This shift not only simplifies data management but also unlocks new avenues for enterprise software services to construct digital processes leveraging integrated data. In such a way, all aspects of product development and business processes will be coordinated via a single product model – engineering BOMs, inventory management, supply chain, raw materials, material requirements planning will be connected together. This model can connect engineering and design software together with contract manufacturers, suppliers and OEMs together. As industries embrace digital BOMs, they step into a future of enhanced efficiency, agility, and innovation, heralding a new era in industrial management and operations. Just my thoughts…
Best, Oleg
Disclaimer: I’m co-founder and CEO of OpenBOM developing a digital-thread platform with cloud-native PDM & PLM capabilities to manage product data lifecycle and connect manufacturers, construction companies, and their supply chain networks. My opinion can be unintentionally biased.