How to make PLM more than just a buzzword? An article Make PLM Great Again written by Lionel Grealou in his blog V+D caught my attention earlier this week. The question Lionel asked there why PLM seems to mean something different to everyone (and that is perhaps part of the problem), deeply resonating. Usually, I say that when you ask two engineers about PLM, you can get more than two explanations. But enough for jokes and let’s get a bit more serious… Why the letter “P” drives so much conundrum and how to help engineering and manufacturing teams to. understand PLM better and, most importantly to come into alignment about how PLM can help their organizations.
A broad purpose of PLM
Product Lifecycle Management (PLM) is a transformative concept that enables organizations to organize information, collaborate, innovate, and optimize processes across the entire product lifecycle. However, PLM’s multi-disciplinary nature means different things to different people in organization. This is where it stuck in a disagreement. Engineers might see PLM as a tool for managing technical data, while executives view it as a driver of innovation. If we want to understand the power of PLM, it’s essential to explore how it serves each role, fostering collaboration and driving value throughout an organization.
CIMdata, one of the leading analytical and consulting outfit helping industrial companies and software vendors created a summary showing the “investment” into PLM by industrial companies. As we can see the top of the investment goes into a “traditional” functions provided by PLM vendors for the last 20+ years.
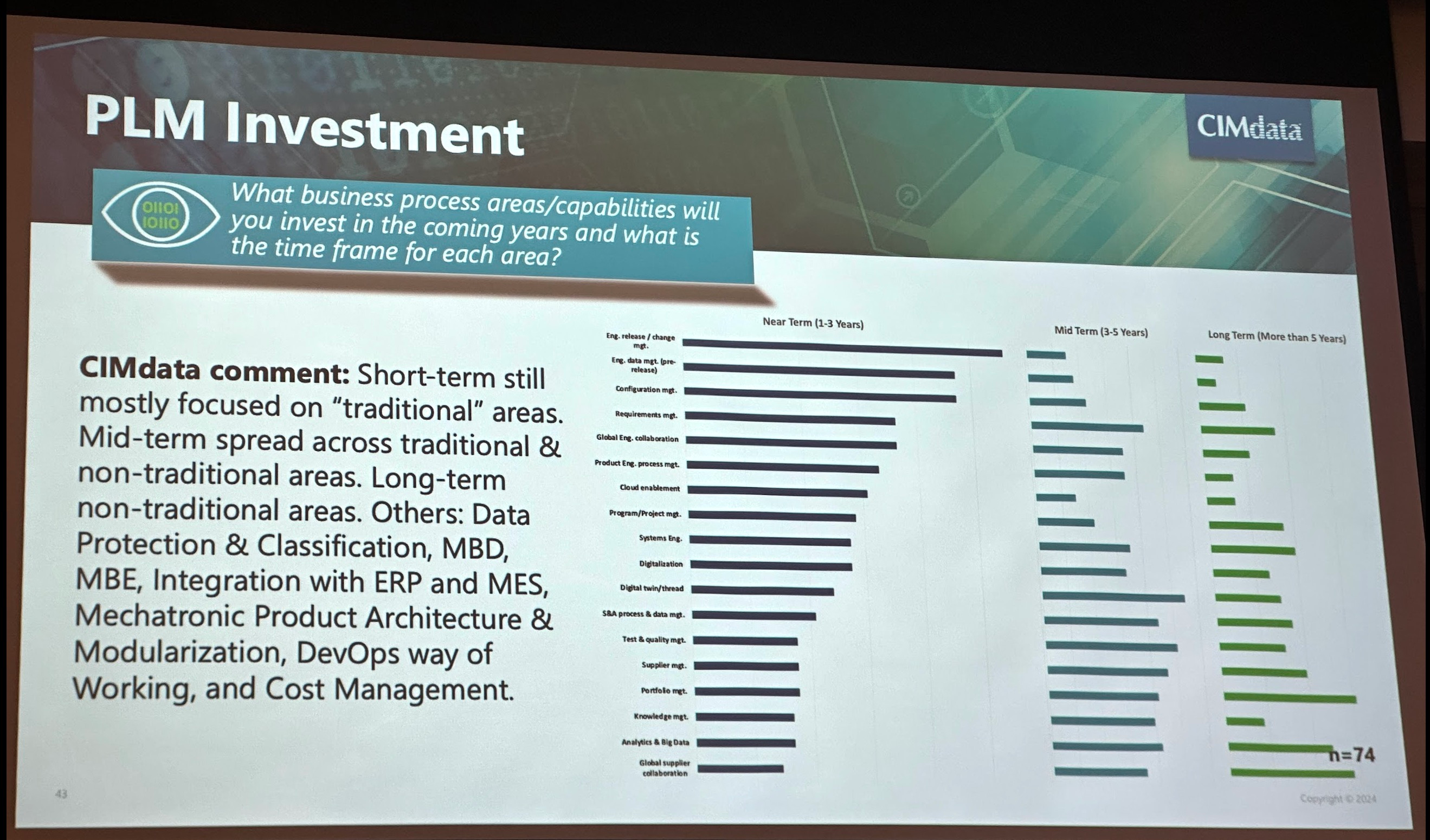
At the same time, debates around different functions of PLM mentioned in Lionel’s article are real because companies are looking broadly in a different aspects of company business performance.
12 “P” of PLM Business and Software
In my article today, I’m making an attempt to outline 12 “P” of PLM software and PLM solutions. Product Lifecycle Management (PLM) has evolved into a cornerstone for fostering collaboration, ensuring efficiency, and delivering value across every organizational function. However, looking at business systems, PLM solutions quickly grows beyond traditional thinking of “document management” for CAD systems in manufacturing industry. The idea of PLM is to grow into various aspects of workflows and decision support focusing on production process, supply chain management, product data management, manufacturing processes, a broad perspective on product development process including multiple manufacturing models such as ETO, CTO, CTO+ and expanding into field service, maintenance and operation.
Let’s take a closer look at the 12 “P”s of PLM and their unique roles in driving success.
1. Product Data Management
Product Data Management is essential for engineers and designers, serving as the backbone for managing and organizing technical data like CAD files, schematics, and engineering change orders (ECOs). By centralizing multi-disciplinary design data, ensuring version control, and fostering real-time collaboration, PLM eliminates silos and streamlines design and engineering workflows. This reduces errors, enables faster design iterations, and ensures that manufacturing always works with the latest design, avoiding costly mistakes caused by outdated or conflicting versions. The importance of efficient product data management is growing because of skyrocketing of product complexity.
2. Process Coordination
Process Coordination plays a critical role for manufacturing and operations teams by ensuring a seamless transition from design to production. Connecting two biggest siloes – engineering and manufacturing is extremely important for every company. Acting as a single source of truth for multiple BOMs, manufacturing instructions, and quality checks, PLM support a workflows to reduce delays and errors. When an engineering change is approved, the system support the process of transition between EBOM to MBOM, preventing rework, optimizing planning and keeping production aligned with the latest design changes. This process can be vary depending on the type of manufacturing business process – ETO, CTO, CTO+, BTO.
3. Procurement Optimization
Procurement Optimization simplifies the sourcing process for supply chain and procurement professionals by centralizing supplier data, approved components, and cost comparisons. Supply chain turbulence is a big deal these days. PLM helps organize the information for planning LLI (long lead items) and provide up to date information to optimize raw materials and OTS components ordering. It also optimize RFQ/PO process with contract manufacturers and suppliers. An organized source of data helps to identify alternates and substitutes for components, minimizing risks from supply chain disruptions. For example, if a part becomes obsolete, procurement teams can quickly find alternatives to maintain uninterrupted production, reducing costs and risks.
4. Platform Integration
Platform Integration is critical for IT and digital transformation leaders, as PLM connects seamlessly with other enterprise systems like ERP, MES, and CRM to create a unified ecosystem. This integration establishes the digital thread, enabling end-to-end visibility across the organization. For instance, real-time synchronization between PLM and ERP ensures that inventory and BOM updates flow efficiently, eliminating redundancies and data silos. Modern SaaS business systems provides a much easier way for companies to consume software functions. Check an interesting statistics about SaaS software in this article.
The number of Software as a Service (SaaS) applications used by businesses varies based on company size: small businesses is approximately 253 SaaS applications, mid-market businesses is around 335 SaaS applications, and for enterprises is bout 473 SaaS applications. On average, organizations utilize 371 SaaS applications. These figures represent a 32% increase in SaaS usage since 2021.

5. Product Innovation
Product Innovation is a key focus for executives and decision-makers, with PLM fostering innovation by connecting teams, breaking silos, and providing lifecycle insights. By aligning product strategies with market demands and customer feedback, organizations can accelerate time-to-market and improve outcomes. For example, executives can use PLM dashboards to monitor product launches, identify roadblocks, and make informed decisions quickly about usage of specific function, covering of specific business KPI, or workflow.
6. Public Perception
Public Perception is enhanced through PLM by providing marketing and customer experience teams with accurate, consistent product data. This ensures clear communication of features and benefits, building trust and improving customer confidence. For instance, marketing teams can use PLM to pull precise specifications and images for campaigns, ensuring consistency and avoiding errors that could harm the brand.
7. Performance Tracking
Performance Tracking enables quality assurance teams to monitor quality metrics, testing protocols, and compliance documentation throughout the product lifecycle. PLM integrates these tools into workflows, helping teams identify and address issues proactively. For example, when a supplier defect is detected, QA teams can trace its impact on multiple product lines and take corrective actions to minimize downstream disruptions.
8. Product Lifecycle Orchestration and Project Management
Product Lifecycle Orchestration is a vital tool for product managers, offering a high-level view of progress, costs, and timelines. PLM ensures alignment across teams, helping managers make informed decisions and prioritize effectively. For instance, a product manager can evaluate the cost and timeline impact of an engineering change, ensuring that projects stay on track and aligned with strategic goals. The lifecycle orchestration is tightly connected to project management and delivering of product programs. The difference between these two depending on specific company needs and organization, but it is vital for business processes efficiency.
9. Profitability Management
Profitability Management supports financial teams by tracking costs associated with product development, manufacturing, and lifecycle management. PLM provides cost transparency, enabling better profitability analysis and decision-making. For instance, financial analysts can use PLM to assess how sourcing changes during development affect overall product costs and profitability, helping optimize margins.
10. Policy Compliance
Regulation and compliancy is on the rise. Policy Compliance is streamlined for sustainability and compliance teams, as PLM tracks regulatory requirements, sustainability metrics, and environmental impacts. By ensuring that products meet industry standards, PLM helps avoid fines and supports sustainability goals. For example, a compliance officer can use PLM to verify that a new product adheres to environmental regulations in multiple markets, avoiding costly penalties. Among recent development is a new “digital passport” regulation.
The digital passport regulation is an emerging initiative driven by governments and industries to enhance transparency, sustainability, and traceability. A digital passport is a product record associated, containing key information such as materials used, production processes, compliance certifications, environmental impact, and repair or recycling guidelines. This concept is gaining traction and will demand support from PLM initiatives and software developers. These regulations require to provide detailed, accessible, and standardized data for stakeholders across the supply chain, fostering accountability and promoting a more circular economy.
11. Product Knowledge Repository and Product Intelligence
AI is changing everything around us and PLM will be a core element of AI transformation for industrial companies. The main reason – product data, which is a fuel to build AI in the context of a specific customer needs. Product Knowledge Repository is foundation of AI and it benefits every aspect of development, manufacturing, and maintenance teams by acting as a centralized source for product information, supplier records, configurations, service manuals, and maintenance records. This ensures quick and accurate resolution of issues in product development and customer support and maintenance. A product support copilot can become an invaluable tool getting access to all information. For instance, a support agent can access PLM to identify the correct replacement part for a customer, finding relevant product configuration, directly connecting to supply house for part ordering.
12. Proactive Service
There is a huge interest in new business models in manufacturing. Companies are not selling their products anymore, but using them to provide a services – construction machines, robots, industrial equipments, drones, etc. All these products are included in “services” and technically “rented” to customers. Which creates a spike in the needs to maintain products, which is completely different from selling products off the production dock to customers.
Proactive Service is vital for field service and maintenance teams, as PLM provides insights into maintenance schedules, spare parts availability, and product updates. By enabling proactive service, PLM reduces downtime and builds customer trust. For example, technicians can use PLM to schedule preventive maintenance based on real-time usage data, extending product life and improving efficiency.
What is my conclusion?
By empowering every function and connecting data across the organization, PLM delivers unmatched value. Understanding what is your “P” in product lifecycle management, focusing on the business benefits and optimizing PLM for your organization is the key. The 12 “P”s of PLM can give you an idea how to make PLM business oriented and unlock its full potential, by adopting innovative technologies and connecting them to business needs.
To make it happen requires a combination of two main efforts – (1) brining new technological innovation and (2) map to business processes strategies. It is a wining combination that will make PLM successful in the future. Just my thoughts…
Best, Oleg
Disclaimer: I’m the co-founder and CEO of OpenBOM, a digital-thread platform providing cloud-native PDM, PLM, and ERP capabilities. With extensive experience in federated CAD-PDM and PLM architecture, I’m advocates for agile, open product models and cloud technologies in manufacturing. My opinion can be unintentionally biased.