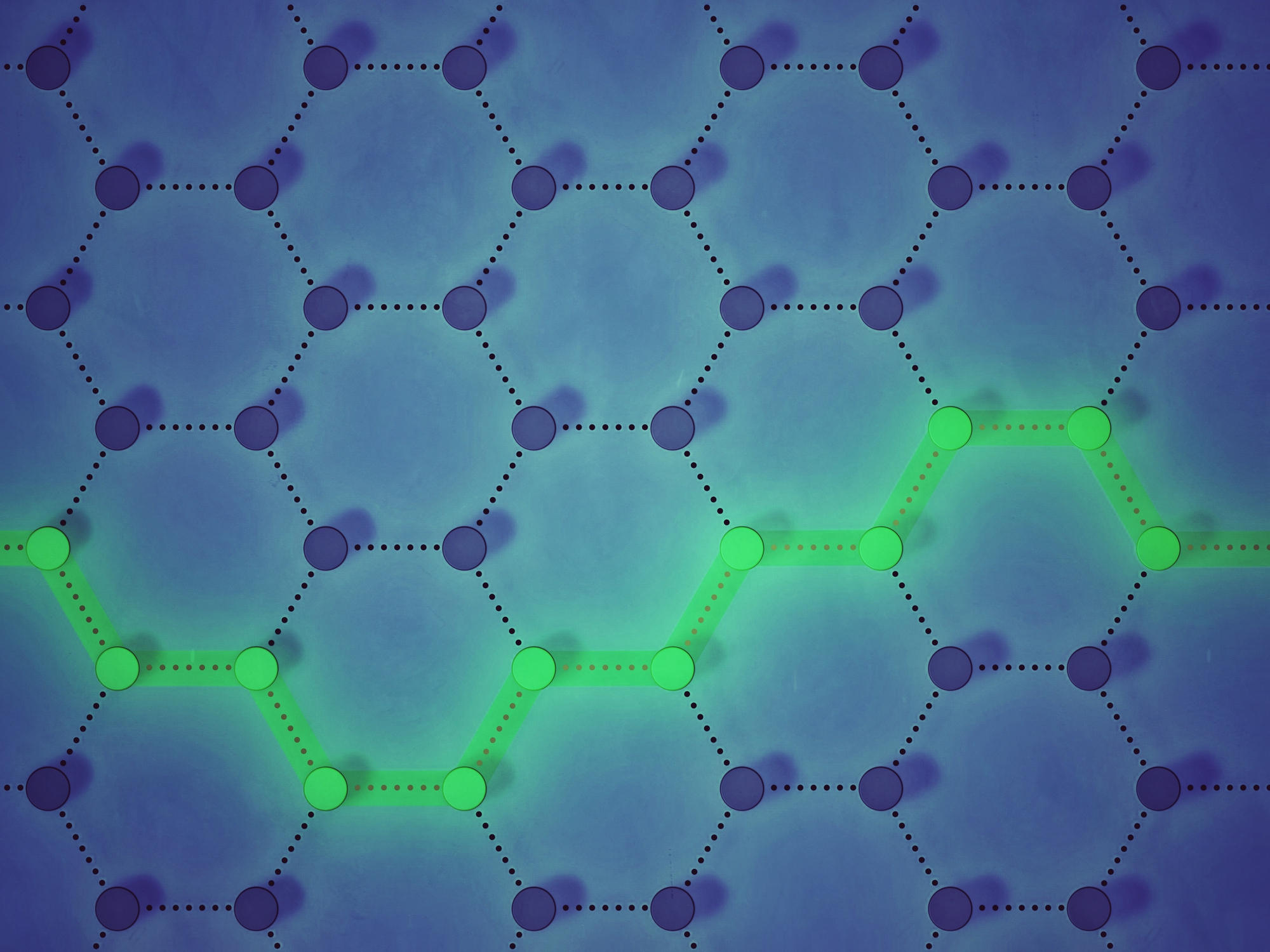
My article about building a product model for digital thread applications triggered a healthy amount of conversations. I appreciate everyone who contacted me online and offline as well as left comments in my LinkedIn post. Also, thank you to my readers who sent me links to presentations about various implementations of digital thread. And, very special thank you Matthias Ahrens for materials about OSLC Fest and presentations. I will talk about it later in my article. Also, thank you Andreas Lindenthal for your comments about traceability. And finally my special thank you for Prof. Martin Eigner and Prof Jorg Fischer for continuous contribution and sharing you insight and experience.
The Problem of Traceability
Modern product development process of complex products requires involvement of multiple systems. You can find many enterprise system starting from CAD/PDM/PLM and extended to MRP/ERP/MES/CRM and many other systems and brownfield applications that live in manufacturing companies for a long time. The traceability challenge that many manufacturing organizations are experiencing is to provide a consistent information about product between all application domains (eg. mechanical, electronics, etc.) and lifecycle stages (engineering, production, maintenance, etc.)
In some applications, the problem of traceability is very critical, such as the ability to link between configuration of product for the customer or production and the way it linked to engineering information, releases and drawings. Each application that exists in this field has its own data model and it creates complexity and difficulties of tracing data between these systems.
I recommend you to follow this conversation about Part traceability and revisions between PLM and ERP systems started by Andreas Lindenthal. In a nutshell, the core of the discussion is different capabilities of PLM and ERP system to manage Part Revisions (including historical capabilities of both systems to manage revisions). While an inclination of a typical PLM system is to implement Part revisions and EBOM, it creates a complexity of tracking the relationships (PLM system has Part Revisions and ERP system doesn’t need it). Connecting these two system approaches sounds like a complex task. At the same time, the suggestion not to manage a BOM in PLM system and link between ERP BOM with no part revs and document revisions in engineering method sounds to me like a step back in the world without engineering BOM that can be difficult when managing complex systems.
Possible Solutions and Technologies
I found multiple technologies and solutions to solve the problem of traceability. For many years, the problem was solved using “point-to-point” links and integrations. But a growing complexity of data and processes for product lifecycle combined with complex business process management makes the results of simple links too restrictive. Linking Parts defined in ERP to a document with a specific revisions will create limit companies from getting engineering BOM on a granular level and eliminates the ability to create a holistic product representation by using released drawings (or CAD documents only). Here are possible approaches and examples of the solutions:
- Replicating data between multiple systems
- Build links between systems
- Build configurable links between systems
- Create a product model capable and independent cloud service (software)
The solutions and technologies used in this approaches can vary and dependent on specific systems (eg. PLM) as well as technologies (eg. Graph Model model) or standards (eg. OSLC). The combination of approaches. Here are a few examples of applications I captured with links to applications, presentations and examples.
The following video from Bosch called Cross Domain Configuration Management
a new way to think PLM in engineering and it speaks about creation and OSLC-based layer capturing information from multiple systems with later capability to use this data for different applications. As you can see, according to Bosch, they didn’t find a solution in the market that can do so.
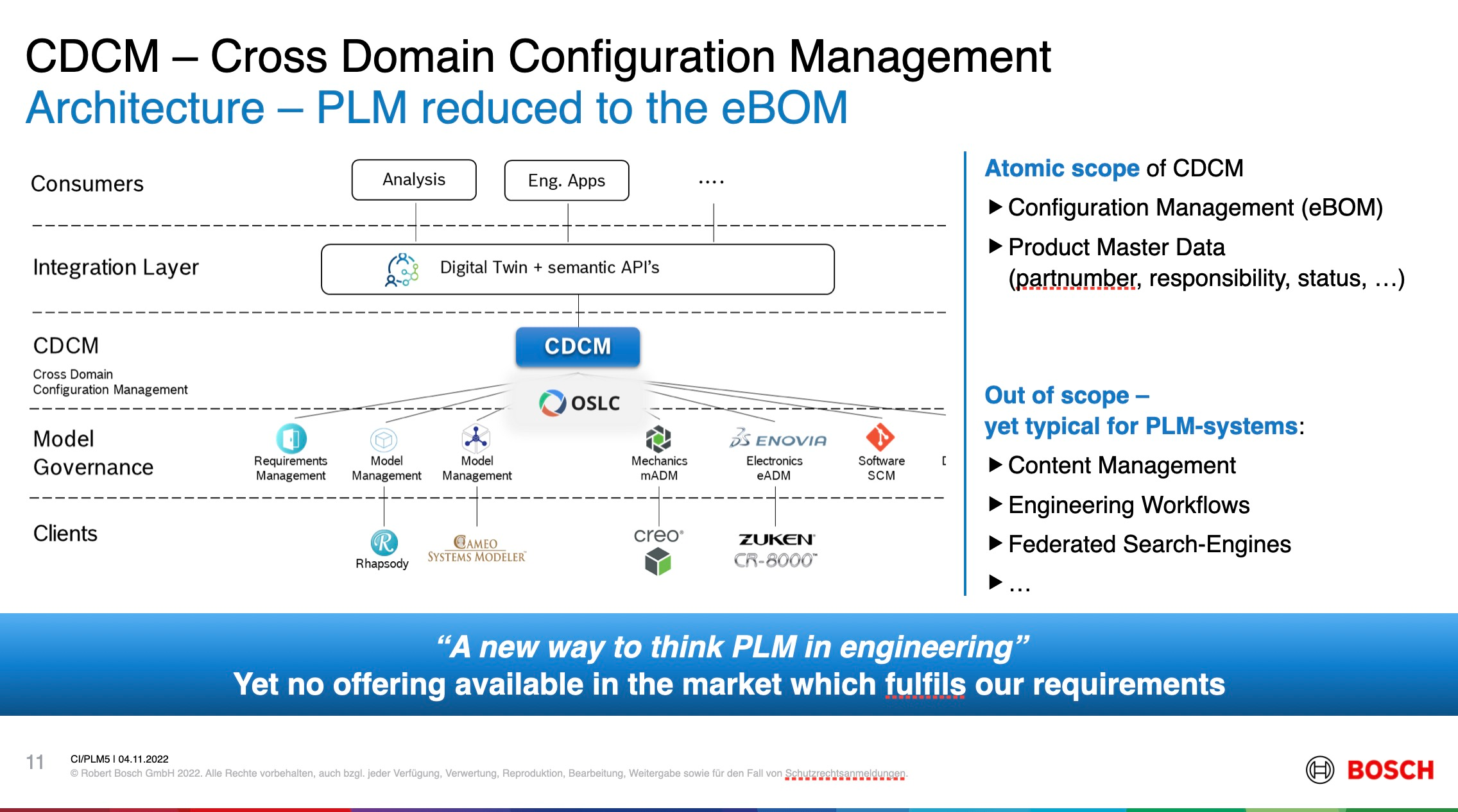
Integration layer and semantic API provides environment where different business process modeling and traceability supporting processes can be implemented.
A different approach that was called Enterprise Data Dependency Manager (EDDM) is presented in this video. Presented by Wipro and Dräger, the approach introduces the architecture of connections between different applications using EDDM server and client.
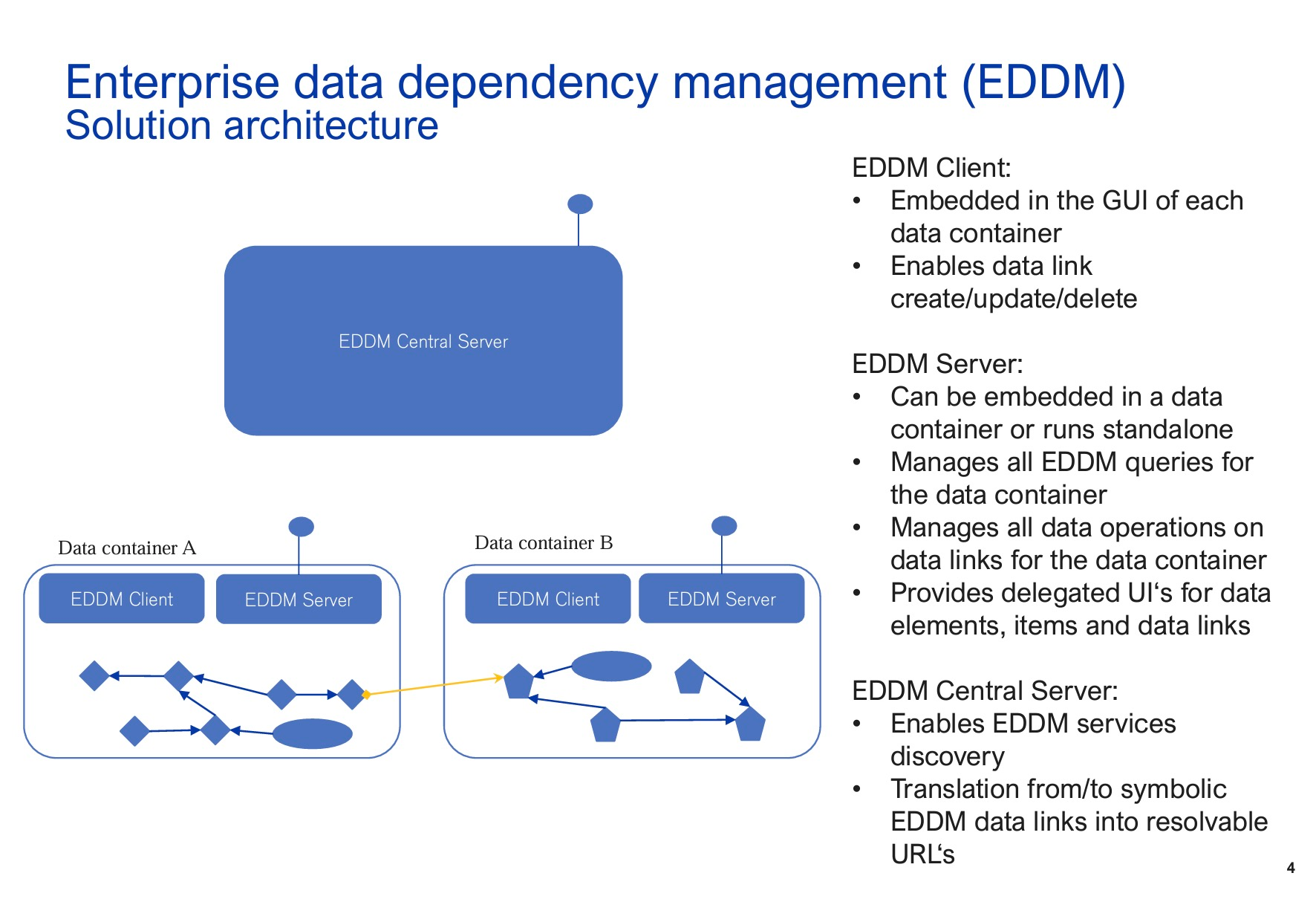
User experience and interface of the system is embedded in the PLM and other software allowing creations of various “links” that connecting pieces of information in different systems.
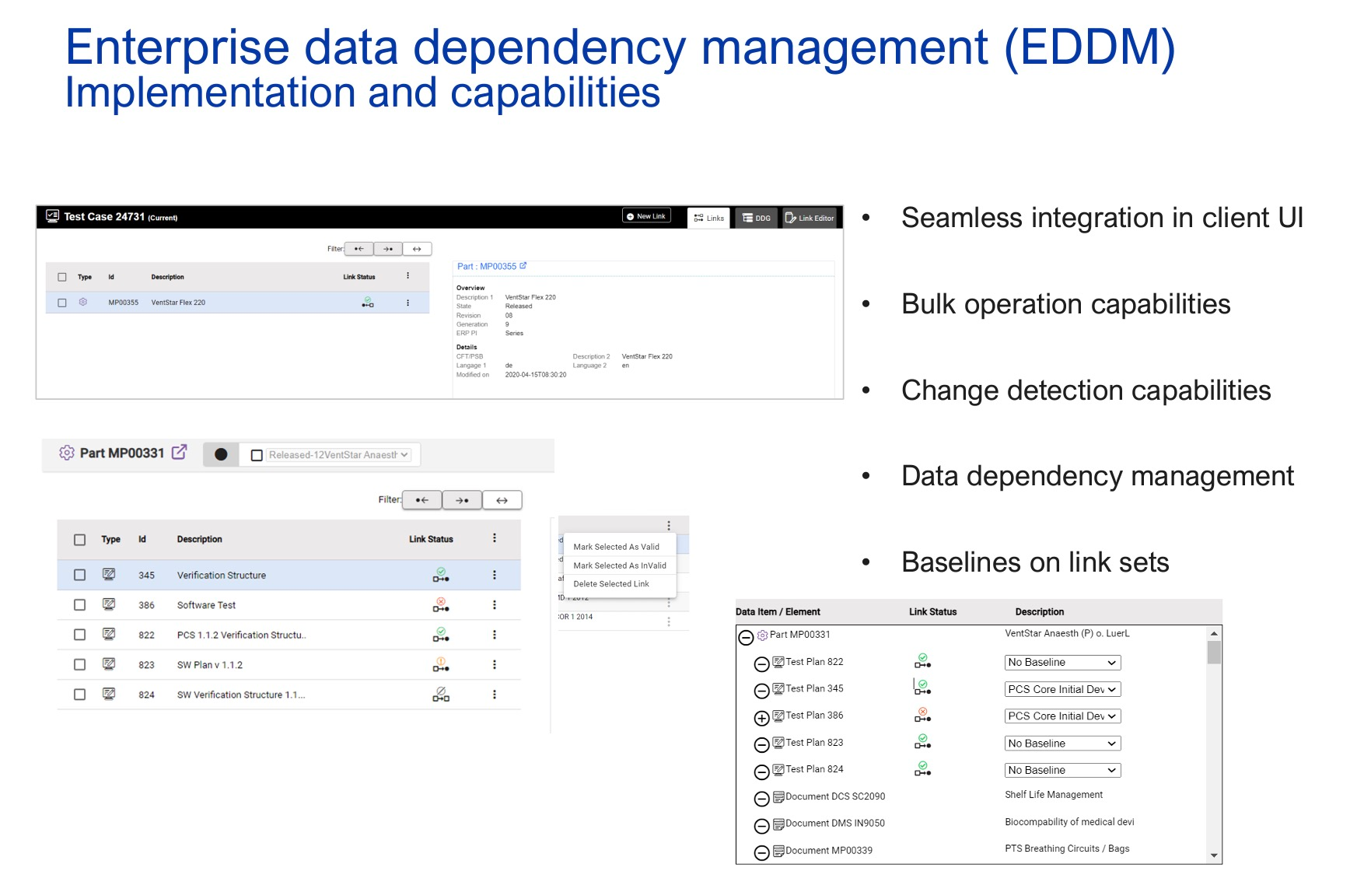
Another option is collecting information from multiple systems into digital thread graph collecting information from multiple systems and providing a way to assess relationships and traceability between data captured from multiple systems.

Another example of building relationships and traceability between multiple systems and data silos is OpenBOM product knowledge graph model.

OpenBOM architecture is built using Graph Database and OpenBOM flexible data model provides a way to bring data from multiple systems, databases and spreadsheets.

OpenBOM approach can use knowledge graph and capabilities of Neo4j graph database and graph data science as a semantic API layer. The differentiator of this approach is data model flexibility and reliance on graph database and graph science for data modeling.
Existing PLM Systems and Digital Thread Models and Applications
So far, I think, there is an agreement that traceability between systems is a painful problem for companies. What existing PLM technologies can provide to customers using their existing PLM platforms. I captured OSLC 2022 forum presentation by PTC speaking about digital thread support.
Here is the architecture of how PTC envision connection between different engineering domains.
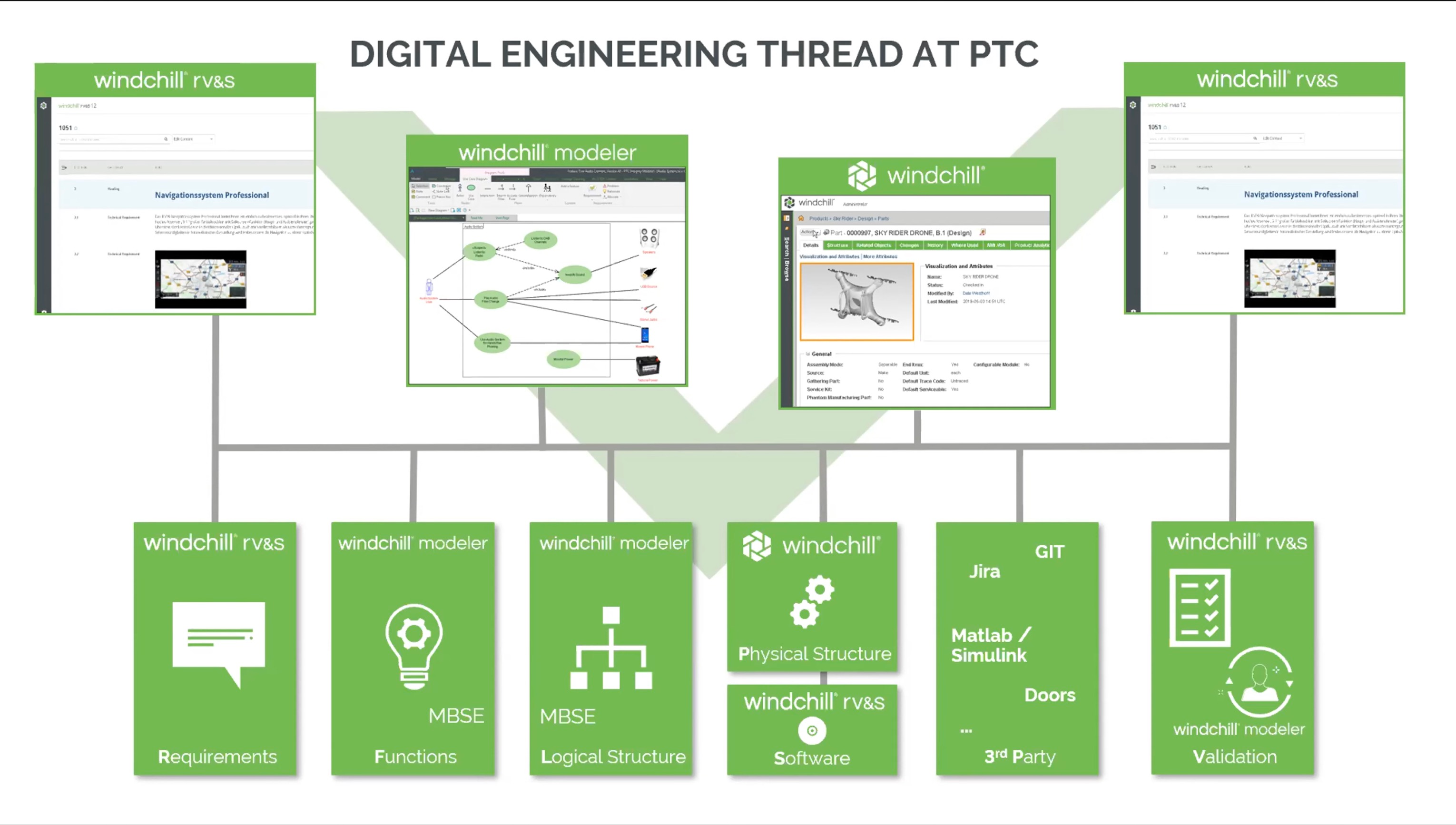
In the following example, you can see digital thread data.
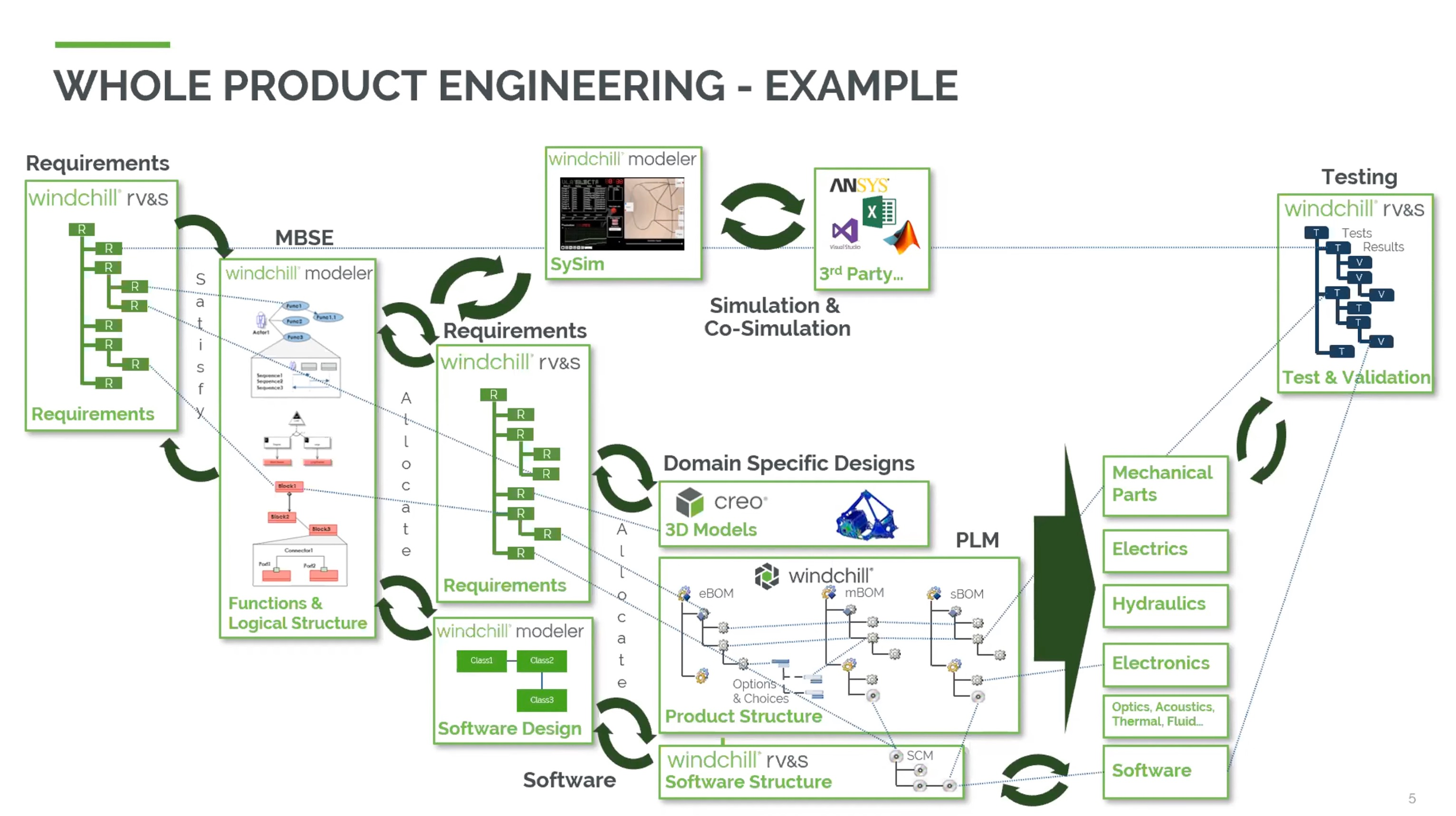
Examples of PTC support of OSLC links shows how traceability can be established.

The UX below is pretty much similar how EDDM solution was build using Aras UX.
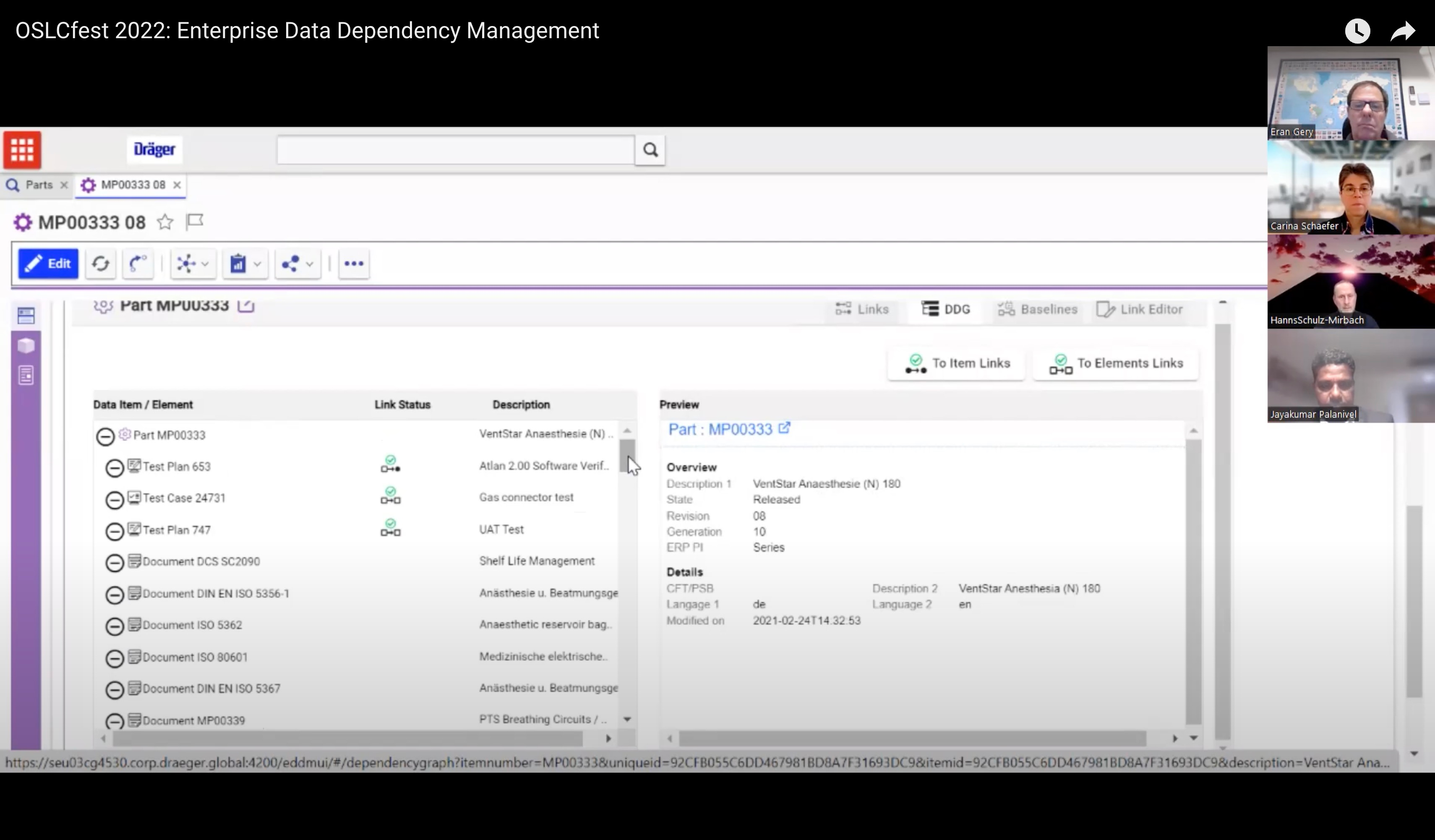
I can see how existing tools can be used. However, the main question I have when looking at this solutions is about how the entire model will be presented and how an entire product data set can be machine readable and navigable. I think, the importance of building a holistic model is important when we think about the future of PLM AI. An ability to have a overall knowledge graph and model that can be translated into LLM can be an interesting opportunity for the future.
What is my conclusion?
Product data is becoming really complex. To support business processes and to organize an efficient management processes to support product development and manufacturing processes is a critical requirement for systematic approach of solving complex product development, configurable product lifecycle, mass production for many organizations. Product traceability is an integral part of organizing efficient business operations and optimizing process performance. It leads to business benefits and will become an important factor in the forth industrial revolution.
The question is what technological approach provides a solid foundation for complex product engineering and manufacturing processes.
Just my thoughts…
Best, Oleg
Disclaimer: I’m co-founder and CEO of OpenBOM developing a digital-thread platform with cloud-native PDM & PLM capabilities to manage product data lifecycle and connect manufacturers, construction companies, and their supply chain networks. My opinion can be unintentionally biased.