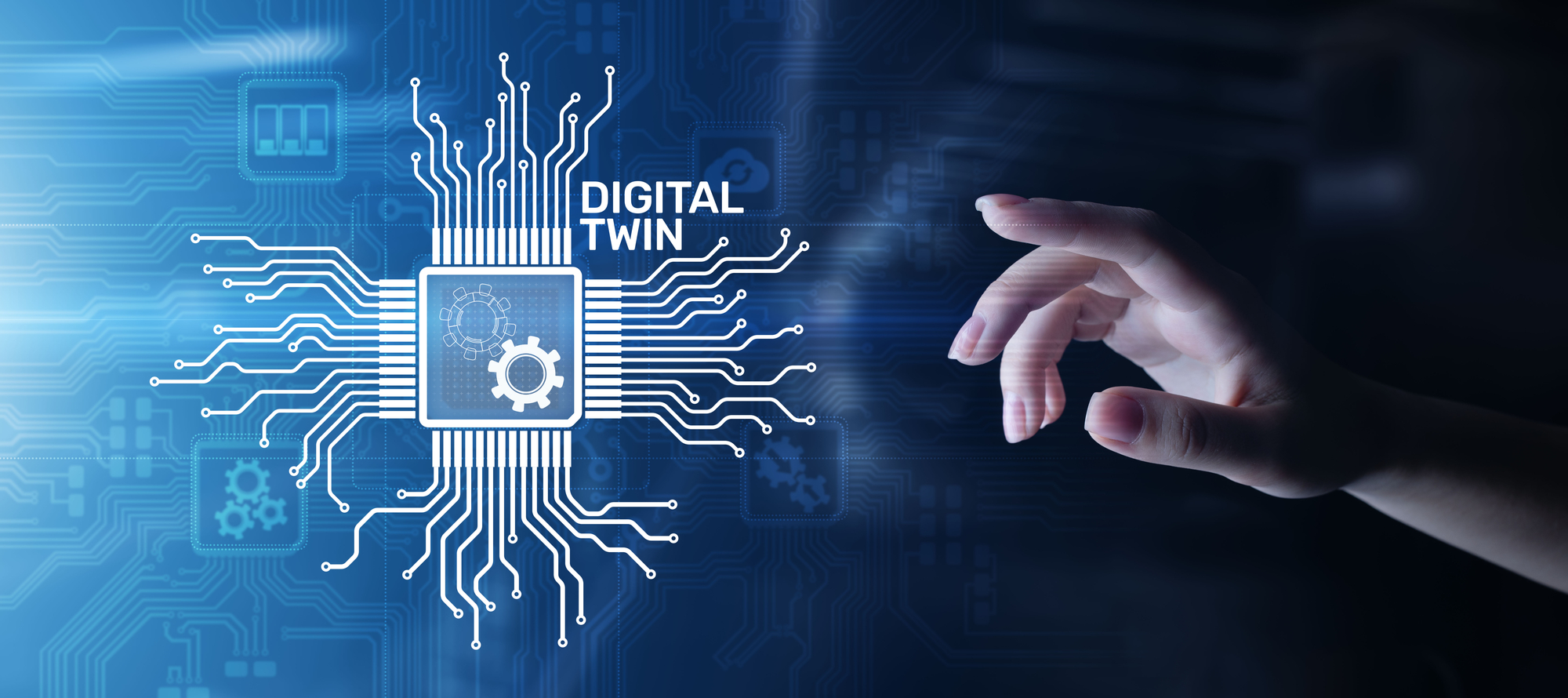
I’m continue to digest what I learned at CIMdata Industry Forum 2024 last week. The main theme of the forum was Digital Twin and its applications for Lifecycle Performance. CIMdata analysis took the Digital Twin topic much far that you can think about. While a typical association of Digital Twin is about simulation of product performance, CIMdata is expanding its beyond the typical scope. The Lifecycle Twin is a way to model a product in a perspective of its development across the entire lifecycle. Here is the initial passage from CIMdata website.
Digital Twins: Enhancing Lifecycle Performance. Initially rooted in electro-mechanical product design and development, ‘digital twin’ has expanded beyond its origins to cover comprehensive multi-attribute modeling and analysis from beyond engineering, manufacturing, and support. Multi-attribute modeling and simulation is core to CIMdata’s definition of the Product Innovation Platform, which underlies most industrial PLM strategies and implementations. The upcoming presentations will consider CIMdata’s expertise on digital twins, define the digital twin and related topics, and provide perspectives from both industry and software/service providers.
In this article I want to share what I learned and my perspective on building a lifecycle digital twin and how it can impact the lifecycle performance. As we expand our perspective on digital twin, I found their applications are evolving from a simple definition of 3D models and various simulations (an initial perspective on what is digital twin) to a more expanded perspective of models that can describe any type of product development, manufacturing, and maintenance activity.
From 3D Model To Digital Twin For Lifecycle Management?
Let’s talk about what is Digital Twin. At its core, a digital twin is a sophisticated model to emulate a physical asset or system, incorporating a wide range of real-time data streams and simulations to mirror its real-world counterpart. Simple examples of digital twin gives you a mechanism to create a replica of of a jet engine (or any complex product or system), continuously updated with sensor data, operational metrics, and environmental factors. This digital twin not only visualizes the current state of the engine but also predicts future performance, identifies potential issues, and enables proactive maintenance strategies. In essence, digital twins serve as virtual companions, offering insights and foresight into the behavior and evolution of physical assets throughout their lifecycle.
If you think about a system that makes this jet engine, including organizations that needed to develop the engine, activities that required to make a product design supply chain planning, sales and maintenance operation you can think about even a broader model of data interconnecting all representation of the model, historical operations, changes, incidents and many other aspects of the engine’s lifecycle. I captured three different perspective on Digital Twin- (1) Market, (2) Industrial, (3)PLM Economy. Let me talk about each of them.
Digital Twin Market Perspective
According to CIMdata, the market for digital twins is experiencing exponential growth, fueled by advancements in IoT, AI, and data analytics. Organizations across industries are recognizing the transformative potential of digital twins in driving operational efficiency, improving product quality, and enhancing customer experience.
However, the real question is how adoption of digital twins will impact different industries – from manufacturing and healthcare to transportation and energy. According to market analysts, the global digital twin market is projected to reach unprecedented heights in the coming years, with investments soaring and adoption rates accelerating. As you can see on the following slide, the question of the digital twin market boundary is really interesting.
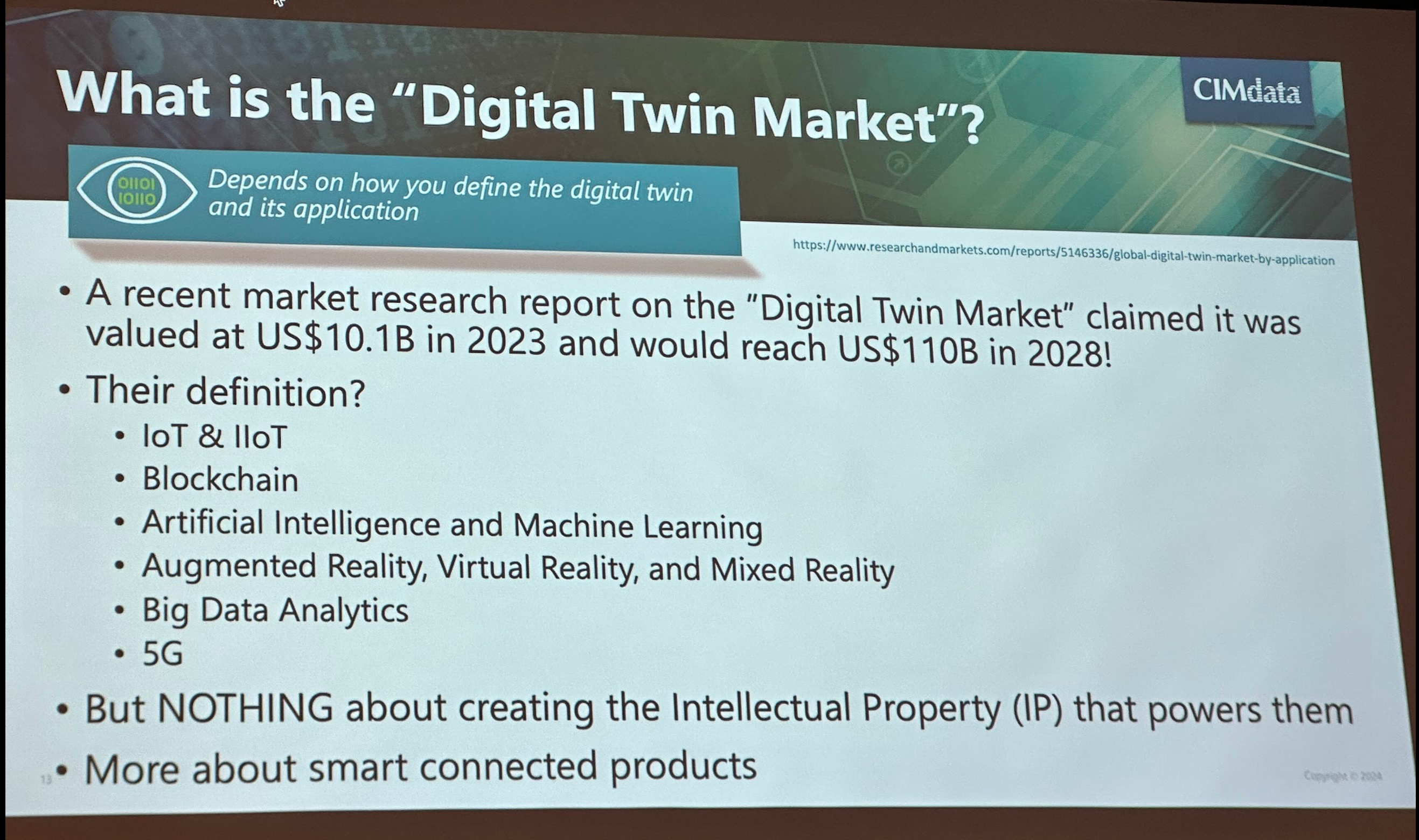
Digital Twin Industry Perspective:
While the concept of digital twins has primarily been rooted in physics-based simulations, there is a growing recognition of its broader implications for lifecycle performance. Beyond mere replicas of physical assets, digital twins are evolving into comprehensive models that encapsulate the entire product lifecycle – from design and manufacturing to operation and maintenance. This paradigm shift underscores the need for a more holistic approach to digital twin implementation, one that transcends traditional boundaries and embraces the interconnectedness of systems and processes.
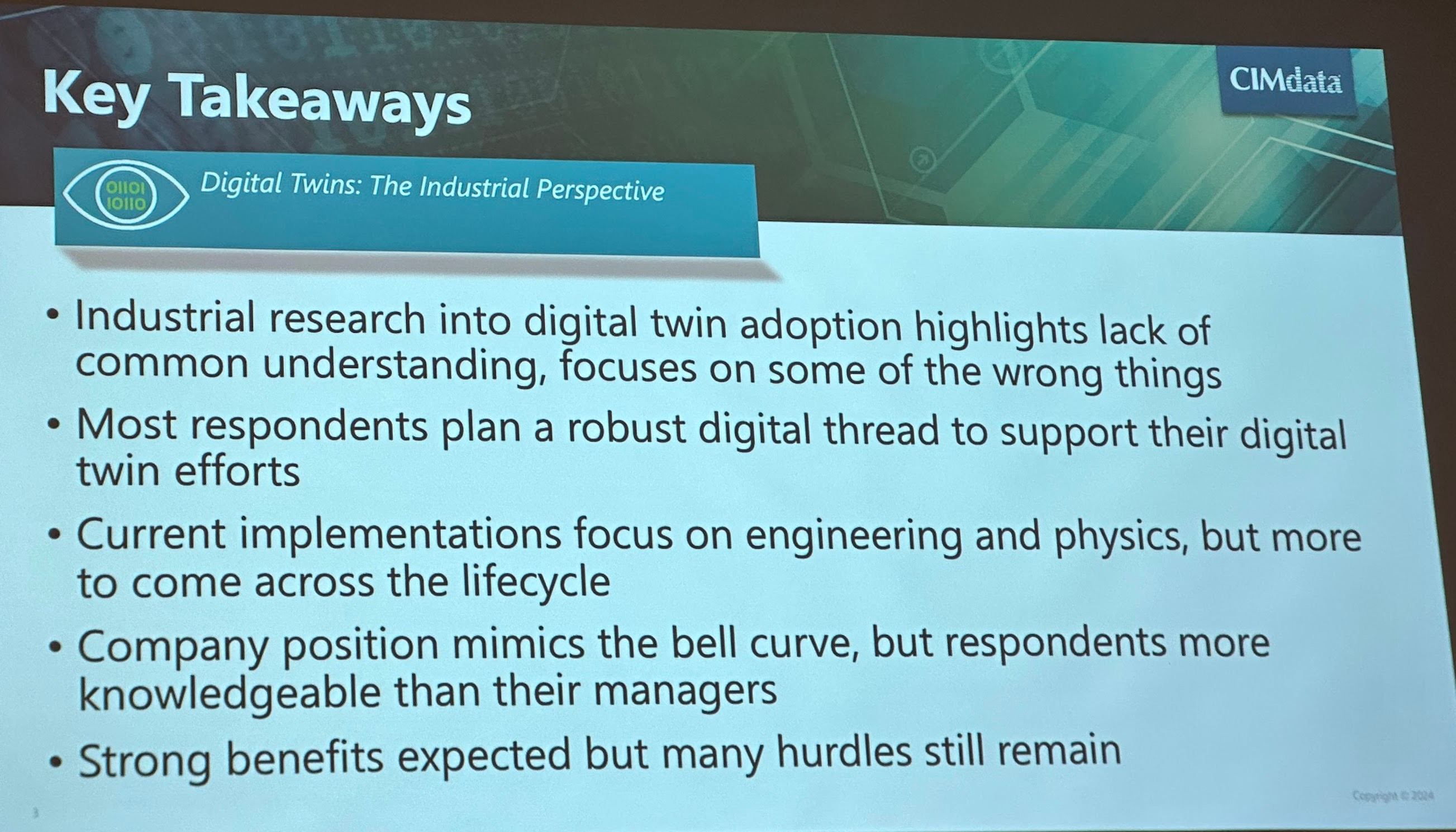
Digital Twin and PLM Economy Perspective:
What role digital twins will play in the space of Product Lifecycle Management (PLM)? Will it be a game changer to offer an unprecedented visibility and control over product lifecycles? PLM vendors are actively exploring digital twin strategies, seeking to integrate them seamlessly into existing platforms and workflows. However, there are challenges to overcome, including data interoperability, scalability, and organizational readiness. Those are the same challenges in PLM that we’ve heard from years. Similar to many PLM implementations there is a need to temper expectations, as vendors often overestimate the capabilities of digital twins and underestimate the complexities of real-world deployment.
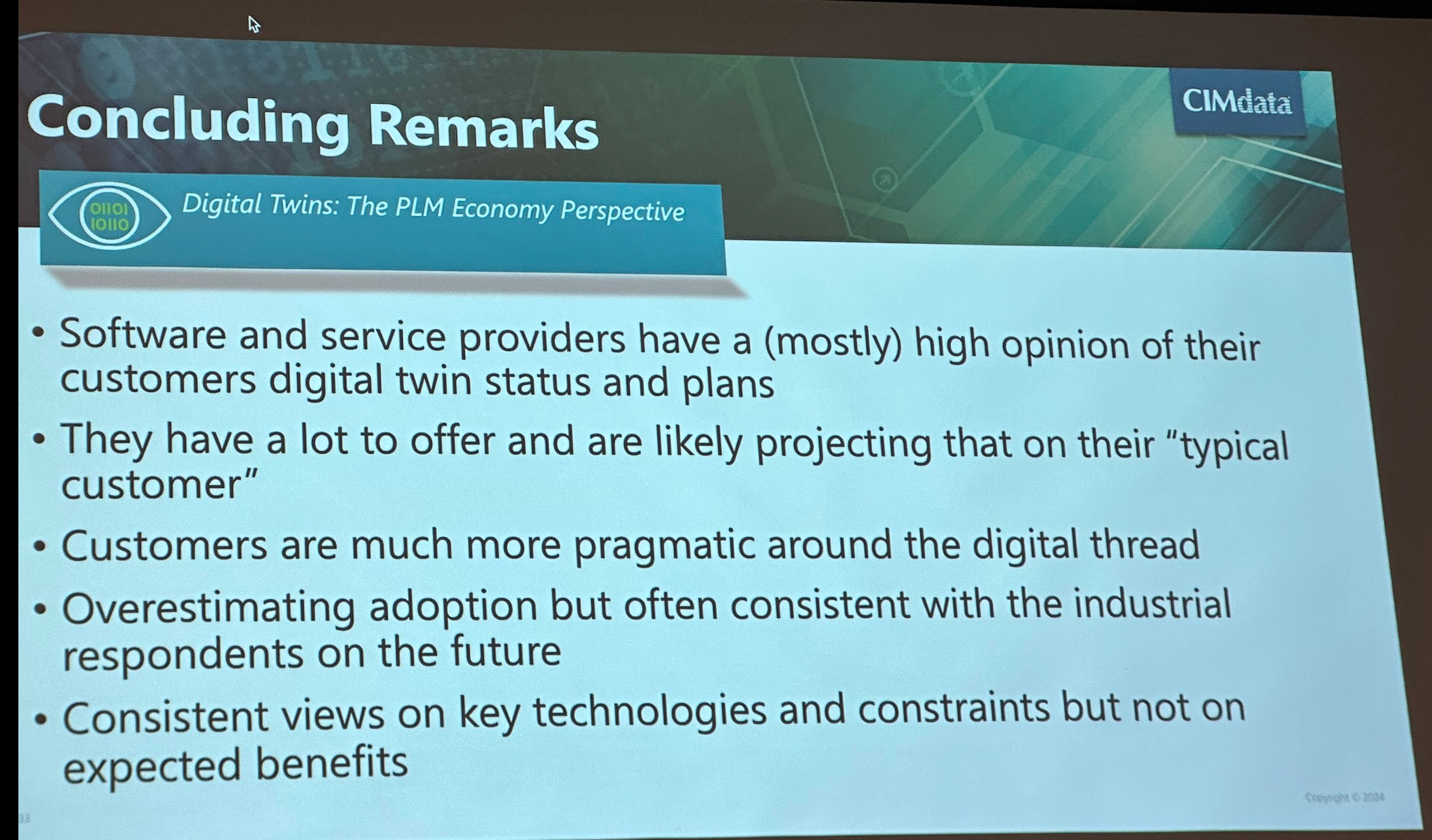
What is my conclusion?
The era of digital twin is upon us. But it is not well defined yet. In the layman PLM definition term, a digital twin is a model that represents information and behavior that can be managed and interpreted to get predictable results about product activities or process output. I agree with CIMdata assessment about the future of digital twins – from a engineering concept of simulating a product performance, it is growing towards a broad model to analyze product development activity, production, supply chain and many other types of activities.
By embracing digital twins as a cornerstone of their digital transformation strategies, organizations can unlock new levels of efficiency, innovation, and competitiveness. One day, Jim Happelmann, CEO of PTC said “IoT is PLM”, largely implying that PLM is now expanding from only capturing engineering and design process to the outside world of real physical products and processes. I want to echo it and say that Digital Twin can grow up to be a paradigm shift in how we design, build, and operate in a rapidly evolving world. At the same time, as every complex system, it has a possibility to fail. The jury is out and we are still very early in the process. What is clear to me that as we move towards more complex world of product development and lifecycle management, the need for product models to represent what companies design and operate and the ability to predict the outcome are becoming really important. Just my thoughts…
Best regards,
Disclaimer: I’m co-founder and CEO of OpenBOM developing a digital-thread platform with cloud-native PDM & PLM capabilities to manage product data lifecycle and connect manufacturers, construction companies, and their supply chain networks. My opinion can be unintentionally biased.