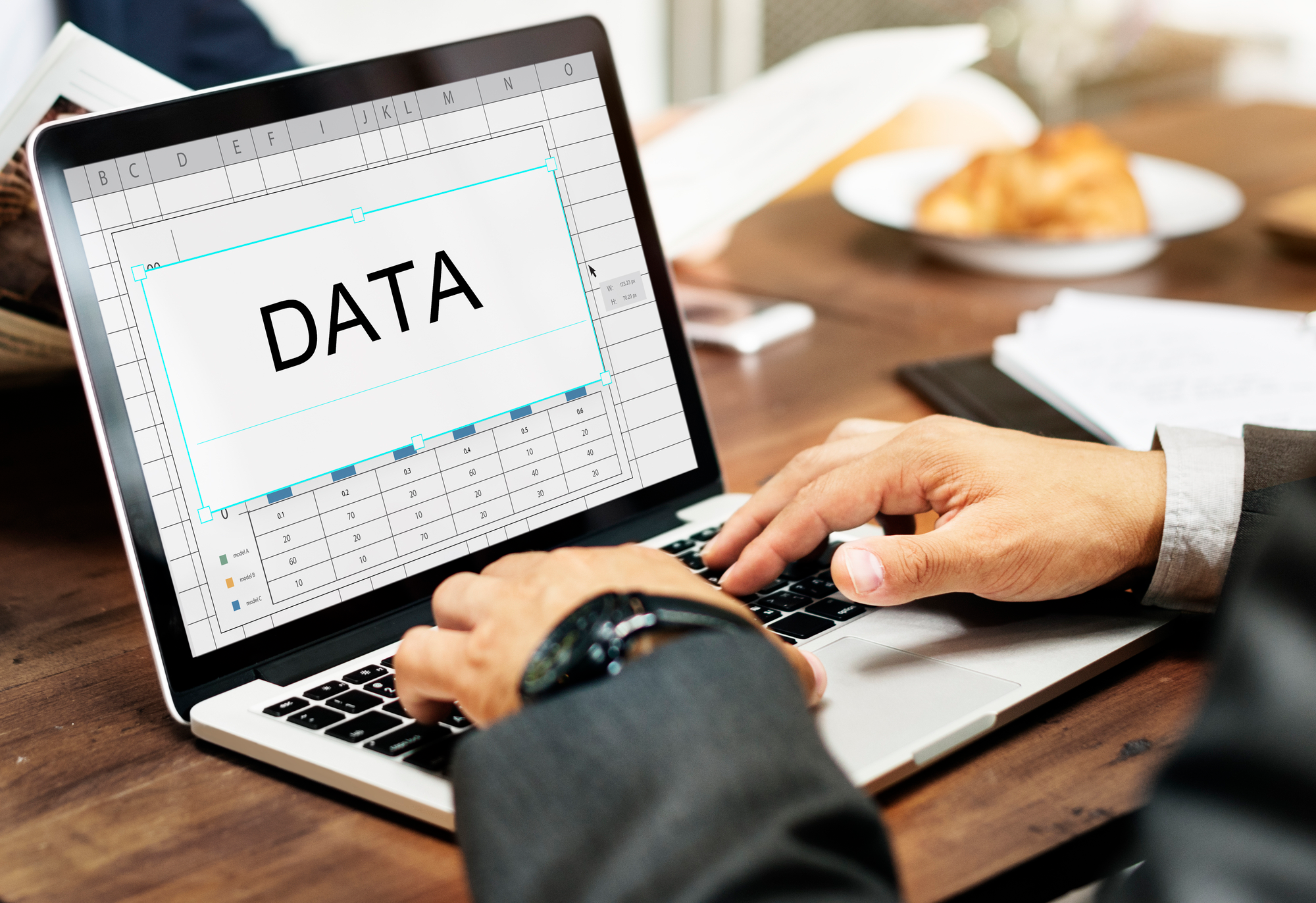
Data is playing a key role in engineering and manufacturing processes these days. In the past, companies relies on drawings and were able to figure out production planning and procurement later. These days, the product and processes are much complex. An engineering is multi-disciplinary with the need to cover an increased design complexity and tools. Planning ahead of increased turbulence of supply chain management and regulation create a high level of complexity for product lifecycle management and product data management. The efficiency and accuracy of data handling play a crucial role in ensuring product success and operational efficiency.
The question how to organize product development processes, customer data, supply chain collaboration and business processes is super critical. You cannot analyze data. when when everything you have is an old outdated Excel. But why is it happening and how to help companies to break through the bad habits is critical help and modern product lifecycle management software can do it.
Why Traditional Excel Processes Are Bad
Traditionally, many organizations have relied on Excel spreadsheets to manage product information. It was a simple and useful habit of all engineers – just dump design data to a spreadsheets, save STEP, PDF and other derivative data and, viola… you’ve got the information pushed downstream. It is simple and easy. I speak with some engineers that will be Infamously Persistent to do it even these days calling PLM tools complex and inefficient. They might be right on the second one- legacy PLM tools are not very user friendly, but at the same time, pouring data to Excels and other forms of spreadsheets leaves companies in a very bad state in everything that related to understanding of their data and efficiency of their operations.
My attention was caught by the article posted by Jeff Winter speaking about organizations that still relies on Excel to manage their operation. Check the article online on LinkedIn- it has some very interesting points about how inefficient can be Excel to manage operations. Here is an interesting snapshot of how operational efficiency can be improved compared to Excel.
𝐔𝐭𝐢𝐥𝐢𝐳𝐢𝐧𝐠 𝐜𝐥𝐨𝐮𝐝 𝐢𝐧 𝐨𝐩𝐞𝐫𝐚𝐭𝐢𝐨𝐧𝐬 𝐥𝐞𝐚𝐝𝐬 𝐭𝐨:
• 26% increase in demand forecast accuracy (Accenture)
• 16% reduction in supply chain operating costs (Accenture)
• 5% increase in revenue growth and profitability (Accenture)
• 16% average reduction in operations costs (Vanson Bourne)
• 15% average reduction in IT spending (Vanson Bourne)
• 17% average reduction in IT maintenance costs (Vanson Bourne)
• 19% average increase in process efficiency (Vanson Bourne)
3 Typical Questions PLM Excel Operations Cannot Answer
When it comes to product data and related informations, many companies feel ok to pour these data in Excel. It is simple and easy from the beginning. However, as products and supply chains become increasingly complex, the limitations of Excel become apparent. Here are three questions that cannot be answered easy when all your product information stored in Excel files:
- Where a specific part is used?
- How much did we pay for this part in the past?
- What are top critical suppliers for our products?
The reason for lack of intelligence is the fact that most of the data stored in Excels cannot be traversed, analyzed and used for intelligent decision support. This is where cloud data management and Artificial Intelligence (AI) step in, offering advanced capabilities that far surpass traditional methods. Let’s explore this transition through three critical questions I mentioned above and also to highlight the benefits of modernizing PLM data management.
Where is this part used?
In a traditional Excel-based approach, answering this question requires manual cross-referencing across multiple sheets and files. This process is not only time-consuming but also prone to errors. Misplaced data or outdated information can lead to incorrect assessments of a part’s usage, potentially disrupting production schedules and increasing costs.
With cloud data management, all information is centralized and updated in real-time. Advanced search functionalities and intuitive queries allow users to quickly trace a part’s usage across all products and assemblies. This real-time visibility ensures that teams have accurate and up-to-date information, facilitating better decision-making and impact analysis.
AI enhances this further by providing predictive analytics. AI can analyze historical usage patterns and forecast future demand, enabling proactive planning and inventory management. This predictive capability helps in anticipating changes in part usage, thereby optimizing the supply chain and reducing downtime.
How much did we pay for this part in the past?
Tracking historical costs in Excel can be cumbersome. Multiple versions of spreadsheets and the need for manual updates often result in inconsistent and inaccurate cost data. This lack of transparency can obscure opportunities for cost savings and make it difficult to negotiate better terms with suppliers.
Cloud data management systems streamline cost tracking by providing a single source of truth. All financial transactions and cost data are stored centrally, ensuring consistency and ease of access. You can pull all revisions of the product with cost rollups and esitmations. Detailed cost history can be retrieved instantly, allowing for comprehensive cost analysis and trend identification.
AI tools take cost analysis a step further by identifying cost-saving opportunities. By analyzing historical cost data, AI can suggest optimal purchasing strategies, identify cost anomalies, and recommend suppliers offering the best value. This automated analysis not only saves time but also enhances financial decision-making.
Who are the most critical suppliers for our products?
Identifying critical suppliers through Excel requires manual data consolidation from various sources, which can be error-prone and inefficient. This manual process often lacks the depth needed to assess supplier performance and risks comprehensively.
Cloud data management enables seamless integration of supplier information from multiple sources, providing a holistic view of supplier performance. It allows for real-time monitoring of supplier metrics, such as delivery times, quality, and cost efficiency. This integrated approach ensures that critical suppliers are identified accurately and managed effectively.
AI capabilities further enhance supplier management by assessing risks and predicting potential disruptions. AI can analyze a wide range of factors, including geopolitical events, financial stability, and market trends, to evaluate supplier risks. This proactive risk management enables organizations to develop contingency plans and maintain supply chain resilience.
What is my conclusion?
If you’re thinking about how to improve your product development and operations, start with these three questions I mentioned above. They will give you the answer on the question – WHY – you cannot stay with outdated age old spreadsheets and hope that you will get it right. The complexity level of modern product data management and lifecycle is too much to be handled by Excels.
Transitioning from traditional Excel-based PLM Software to cloud data management and AI-driven solutions offers significant advantages. Real-time data access, predictive analytics, and enhanced decision-making capabilities are just a few of the benefits that modern tools provide. By addressing critical questions such as part usage, historical costs, and supplier importance more efficiently and accurately, organizations can achieve greater operational efficiency, cost savings, and supply chain resilience.
In an era where agility and accuracy are critical for any company operations, relying on Excels is a sin that manufacturing companies cannot afford. Embracing cloud data management, a modern PLM system for product lifecycle, and AI is not just an option but a necessity. Moving away from outdated Excel-based approaches allows organizations to unlock the full potential of their PLM processes, driving innovation and competitiveness in an increasingly complex market landscape.
Just my thoughts…
Best, Oleg
Disclaimer: I’m co-founder and CEO of OpenBOM developing a digital-thread platform with cloud-native PDM & PLM capabilities to manage product data lifecycle and connect manufacturers, construction companies, and their supply chain networks. My opinion can be unintentionally biased.