In the rapidly evolving landscape of manufacturing, data has emerged as a pivotal asset, often referred to as the “new capital.” According to CIMdata PLM research, existing practices of PLM software usage are still very much focused on the traditional product lifecycle and product data management use cases.
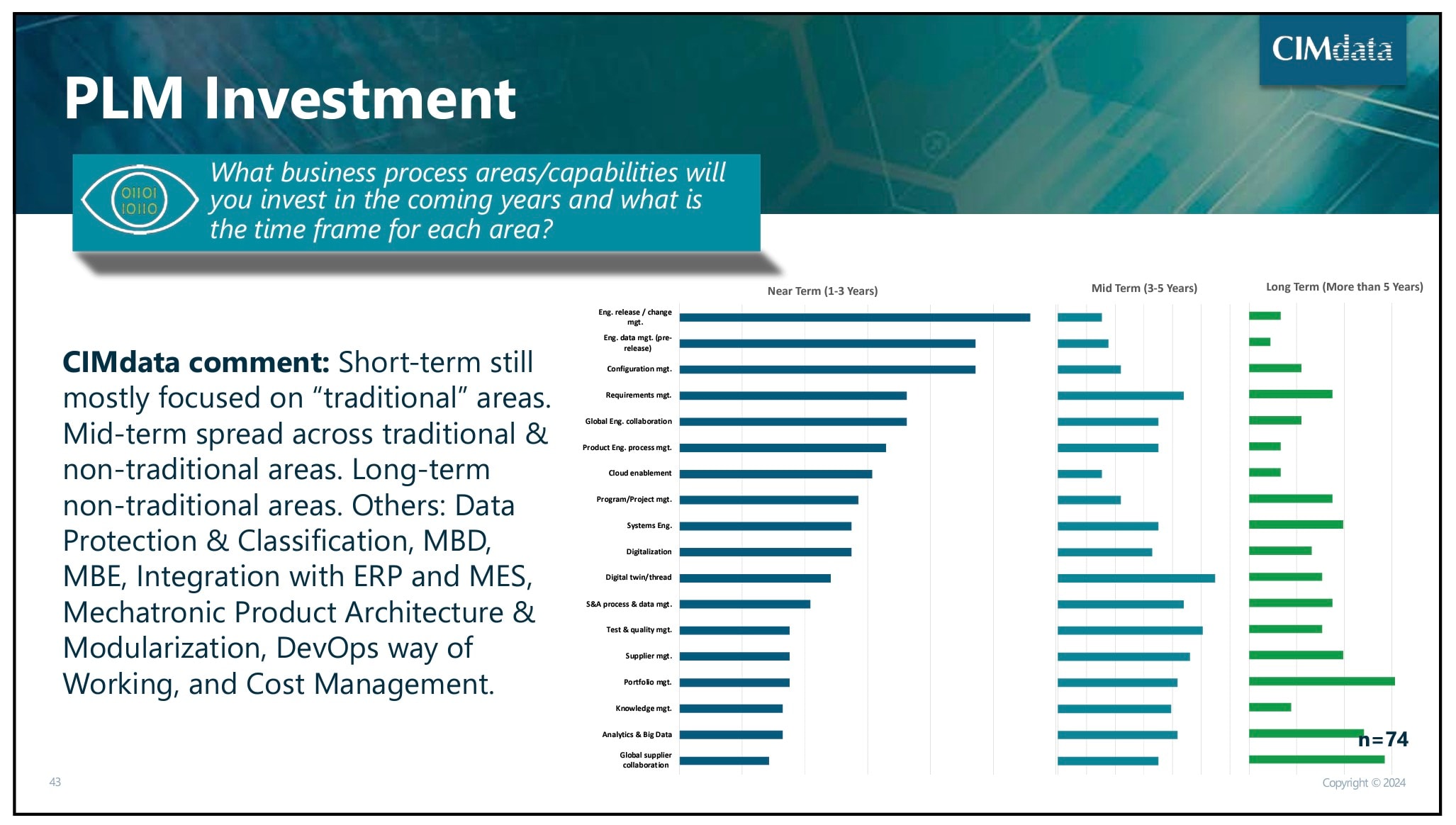
The shift from traditional PLM solutions practices (mostly document driven engineering release) to data-driven strategies is unlocking unprecedented opportunities for efficiency, productivity, and innovation. Data is becoming a critical asset and thinking about Data Lifecycle Management is becoming more and more appropriate. As we look ahead to 2030, the challenges and opportunities of data within Product Lifecycle Management (PLM) systems are becoming increasingly important. In my article today, I want to speak about challenges and opportunities engineering teams and manufacturing companies can find related to data usage.
The New Capital: Why Product Data Matters in Manufacturing
Data is fundamentally transforming the manufacturing industry, creating new avenues for operational excellence and competitive advantage. A recent article in Forbes Data As A New Capital In Manufacturing highlights how data is being leveraged to enhance various aspects of manufacturing, from predictive maintenance to supply chain management and optimization. Sensors embedded in machinery, for instance, can collect and analyze data to predict potential failures and schedule maintenance proactively, reducing downtime and preventing costly breakdowns. This predictive capability is not just about saving time and money; it’s about enabling a more resilient and responsive manufacturing process.
Moreover, real-time monitoring of manufacturing processes allows for the immediate detection of defects and deviations from quality standards, ensuring consistent product quality and reducing waste. The integration of data across the supply chain further optimizes inventory management, improves delivery times, and enhances customer satisfaction. By analyzing customer feedback, usage patterns, and field performance data, manufacturers can also refine product designs to better meet market demands. This data-driven approach extends to every corner of the manufacturing process, from energy consumption to environmental impact, enabling companies to adopt more sustainable practices.
Realizing Data’s Potential: The Challenges Ahead
Despite the clear advantages of data utilization, many manufacturers face significant challenges in fully harnessing its potential. According to a recent report by the National Association of Manufacturers (NAM), a staggering 86% of manufacturers believe that effective data usage is essential for competitiveness. However, realizing this potential is a challenging task. The gap between available data sources and their actual utilization is a notable area for improvement as the industry looks toward the future. Manufacturers must figure out how to organize and analyze their data effectively, ensure that their data is trustworthy and align their business strategy closely with their data strategy.
For years, PLM vendors and implementors were preaching manufacturing companies and engineering teams with the ideas of ditching inefficient data management methods and organizing information in a better way. The same reports shows surprising and shocking facts: engineers and manufacturing teams keep their reliance on spreadsheets, with 70% of manufacturers still entering data manually and 68% using spreadsheets for analysis. This reliance on outdated methods poses a significant barrier to the full realization of data’s potential. Moreover, while 44% of manufacturing leaders report that the amount of data they collect has doubled over the past two years, only 25% have high confidence that the right data is being collected, and most have only moderate confidence in their analytic capabilities.
Top challenges include the fragmentation of data across different systems and formats (53%), difficulty accessing data (28%), and a lack of skills to analyze data effectively (28%). Despite these hurdles, 95% of manufacturers acknowledge that data enables faster and higher-quality decision-making, underscoring the critical need to address these challenges head-on.
Reimagining Data Usage in PLM and Digital Transformation
As we plan ahead for 2030, the landscape of PLM and digital transformation is poised to explore a significant shift. Here are two key trends that analysis from EY found related to data access and cloud solutions:
Customers’ Data Access
The expansion of data access across value chains is challenging traditional roles within the manufacturing ecosystem. Manufacturing customers are gaining unprecedented access to data from various organizations within their value chains, from computer aided design (CAD) and CAM providers to machine tool manufacturers. This expanded access is driving commoditization and standardization, benefiting manufacturers by increasing data availability and transparency.
However, it also presents challenges for traditional hardware suppliers, who may find their application knowledge advantage eroding as it becomes digitally accessible. This shift opens the door for tech companies to introduce new value into the value chain, potentially tapping into profit pools that were previously out of reach.
Cloud Engineering and Manufacturing Tools
Cloud manufacturing platforms are revolutionizing how companies design and order components and assemblies. These platforms offer instant quotes, reducing lead times for prototyping and improving access to component quotes and alternative sourcing options. While the long-term impact of these solutions is still unfolding, they have the potential to disrupt existing customer-supplier relationships, particularly in component manufacturing. By reducing the CAD-to-quote lead time and accumulating know-how across manufacturing processes, these platforms could shift the balance of power in the industrial products sector, especially for small and mid-sized manufacturers.
Adapting to the New Data-Driven Reality
The rise of data as a new capital in manufacturing is not just a trend; it represents a fundamental shift in how companies operate and compete. To thrive in this new environment, manufacturers must embrace connectivity, responsiveness, and digitalization. Connected products offer greater transparency into customer demand, enabling more responsive and proactive services. Digitalizing the customer interface will be crucial as a new generation of engineers expects easier user interfaces and seamless integration across applications.
Furthermore, the push for higher levels of customization and smaller batch sizes will demand greater efficiency in managing production processes, optimizing machine use, and ensuring predictable lead times. Manufacturers that can successfully navigate these challenges by reimagining how data is used within their organizations will be well-positioned to gain a competitive edge in the coming decade.
What is my conclusion?
The importance of holistic data lifecycle management is becoming more and more obvious. Companies are looking to optimize business models and business processes using reliable data. It enables manufacturers to develop new information models for real time data and digital twin. Imaging a modern PLM tool that integrates data, helps more efficient data sharing, increase production efficiency for global manufacturers. As we move toward 2030, the ability to manage data across its entire lifecycle will become increasingly critical. New PLM tools and focus on up to date data and streamline process management. The systems must evolve to support holistic Data Lifecycle Management, enabling manufacturers to unlock the full potential of their data. By addressing the challenges of data fragmentation, accessibility, and analysis, and by leveraging emerging trends like cloud manufacturing and expanded data access, manufacturers can transform data from a mere resource into a strategic asset that drives innovation, efficiency, and growth.
In this new era, reimagining how data can be used is not just an opportunity—it’s a critical competitive factor and in some ways an element of survival for many companies. The companies that embrace the power of holistic data management will be the ones that set the pace for the future of manufacturing industry in the decades to come.
Just my thoughts…
Best, Oleg
Disclaimer: I’m the co-founder and CEO of OpenBOM, a digital-thread platform providing cloud-native PDM, PLM, and ERP capabilities. With extensive experience in federated CAD-PDM and PLM architecture, I’m advocates for agile, open product models and cloud technologies in manufacturing. My opinion can be unintentionally biased.