Earlier this week, I attended the DXM 2024 (formerly PLM Innovation) event that took place in San Antonio TX. Organized by UK based Market Key, this event is known for its customer oriented approach and the discussion focus format. Market Key doesn’t focus on creating a crowded event, but on introducing a platform for customers and experts in product lifecycle management to connect in a calm and relaxing environment.
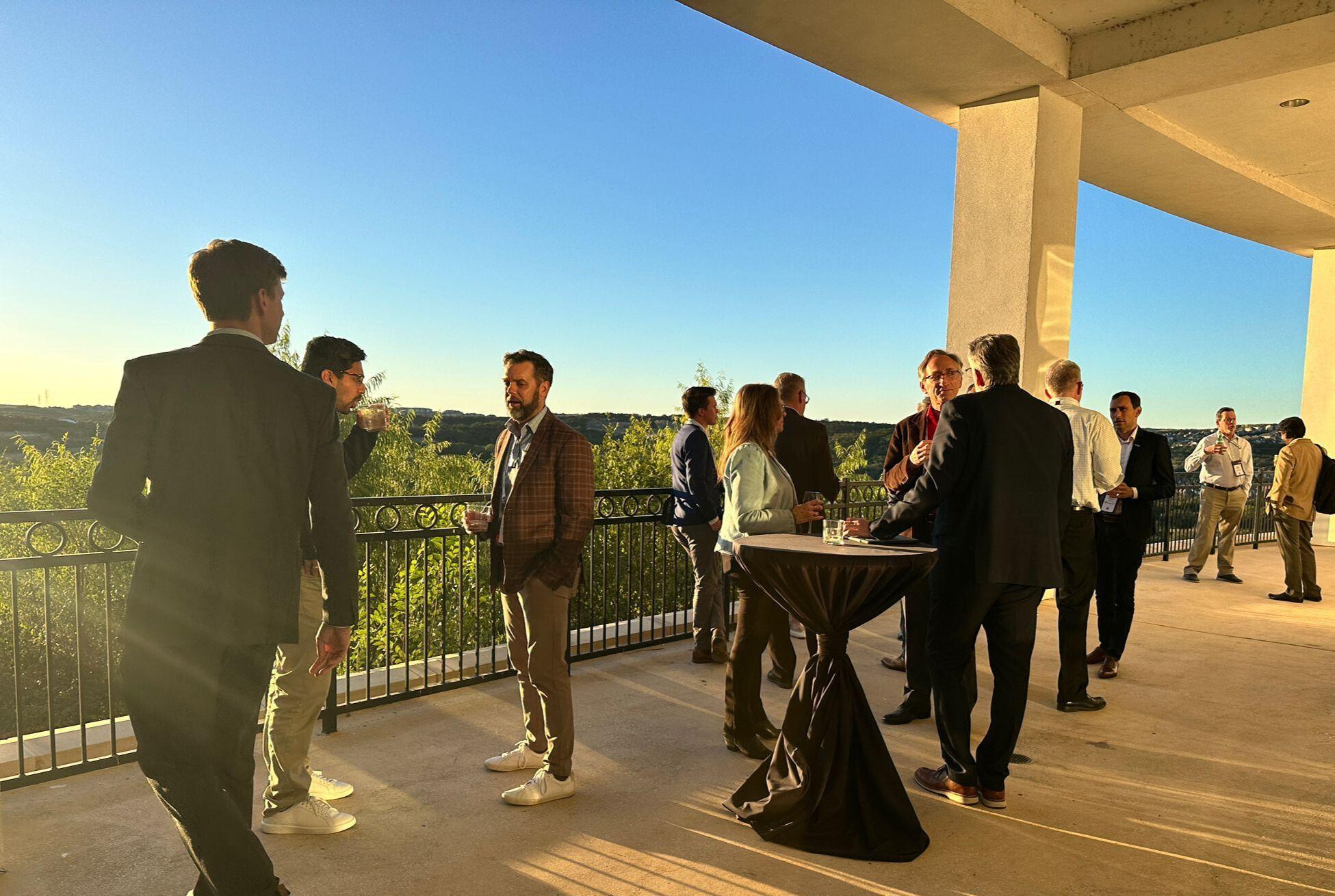
You can appreciate the relaxing atmosphere of networking and opportunity to ask questions from presenters as well as a routable discussion – pick your topic.
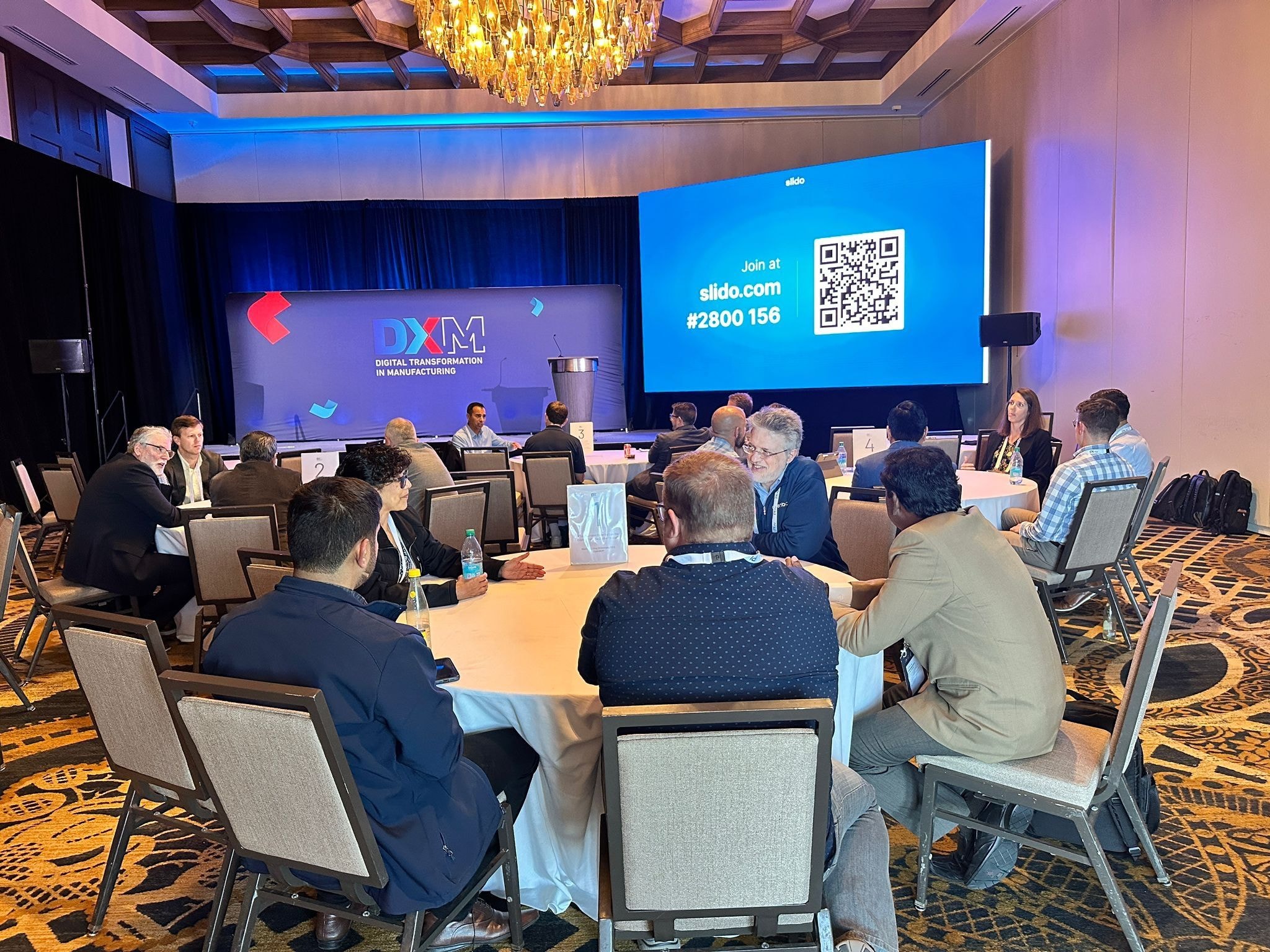
You can check the agenda, the names of the presenters and topics online. I only was able to attend the day two, which features the presentation by Jaswinder Walia, CIO Engineering, GE Aerospace, the discussions about future workforce in manufacturing presented by Purdue University and Georgia Institute of Technology University as well to attend the roundtable discussions, my presentation about Expanding Digital Footprint in manufacturing and the presentation about importance of change management by Alan Mendel, CRO & Chief Strategist, CIMdata.
GE Aerospace Presentation
The key points of GE Aerospace presentation was to share the transformation into a single PLM environment, challenges they experienced and future steps and expanding digital tools including the strategic development of digital threads.
The challenges includes huge data volumes, disconnected systems and multiple data access points.
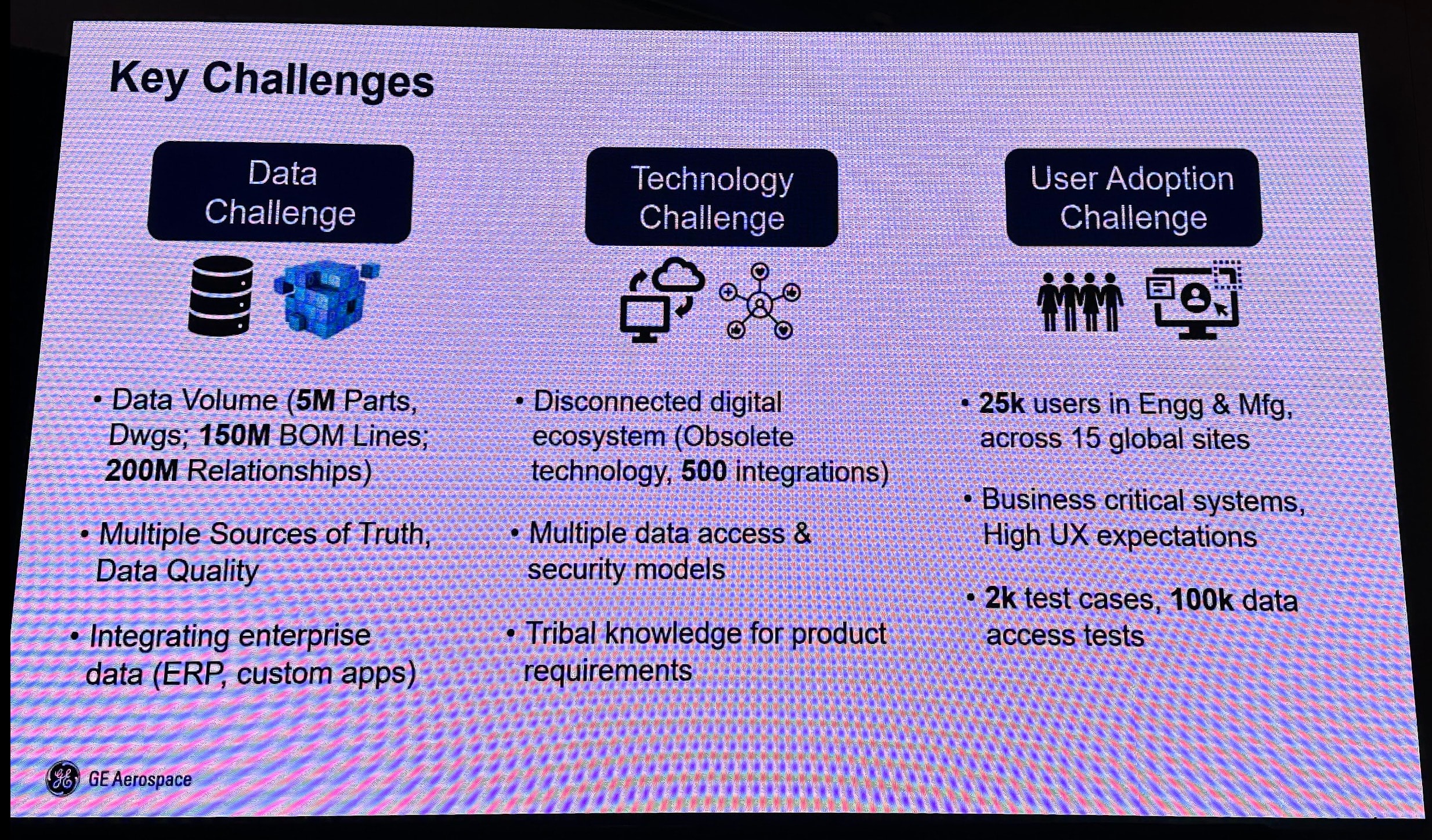
The solution for that was development of one integrated system that uses a single PLM backbone, but expanding services with additional capabilities and functions.
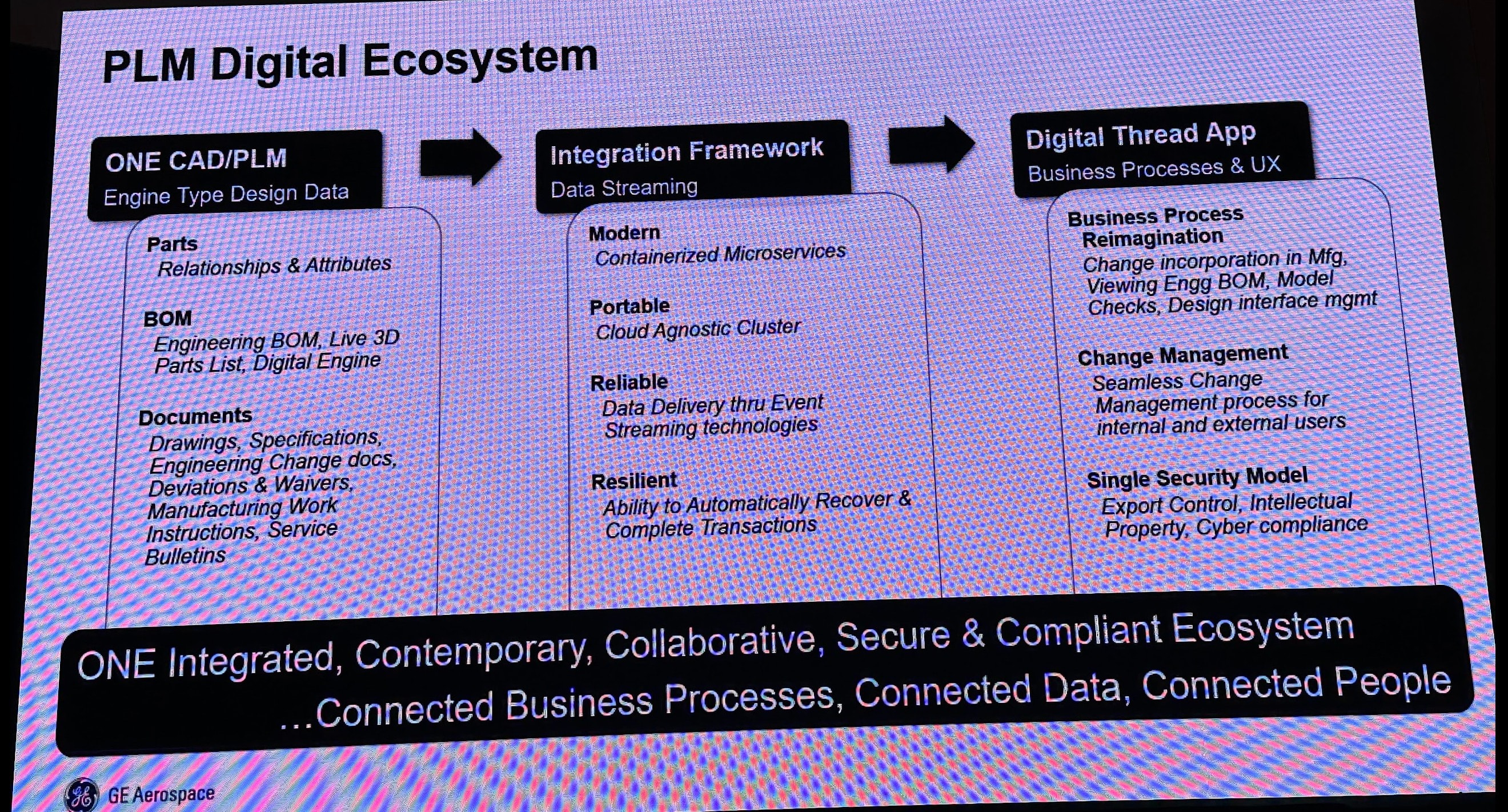
One of the most interesting was a gradual development of AI capabilities by leveraging data from different systems to provides tools that can help to improve efficiency and decision making process.
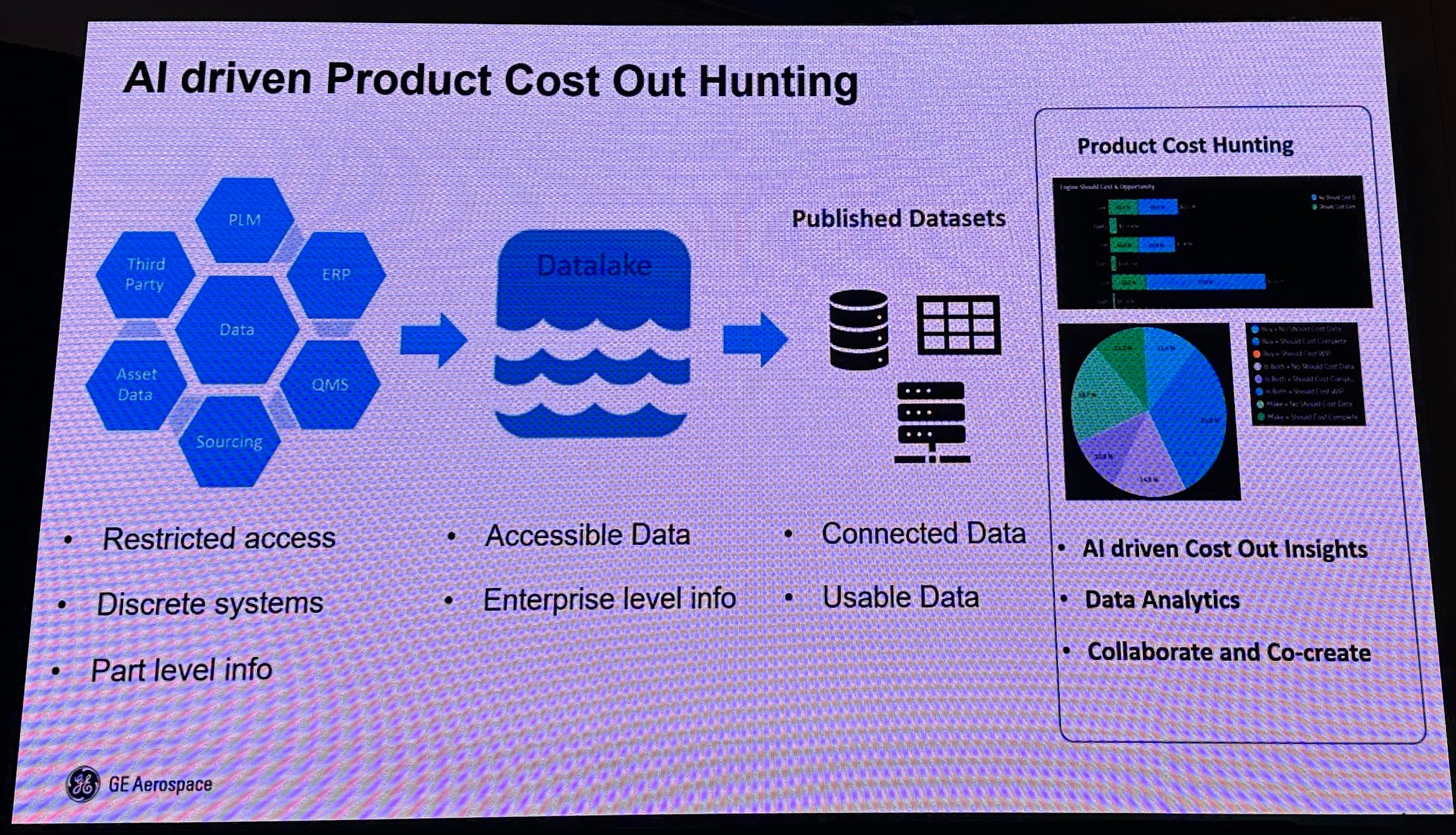
Expanding Digital Footprint to Achieve Operation Efficiency
In my presentation Expanding Digital Footprints to Drive Higher Levels of Operational Efficiency, I shared my observation and experience I collected building OpenBOM on digital transformation and how new technologies can support manufacturing companies in forming a new digital information levels and benefits it can bring. There are key reasons that moving manufacturing companies to think about digital transformation.
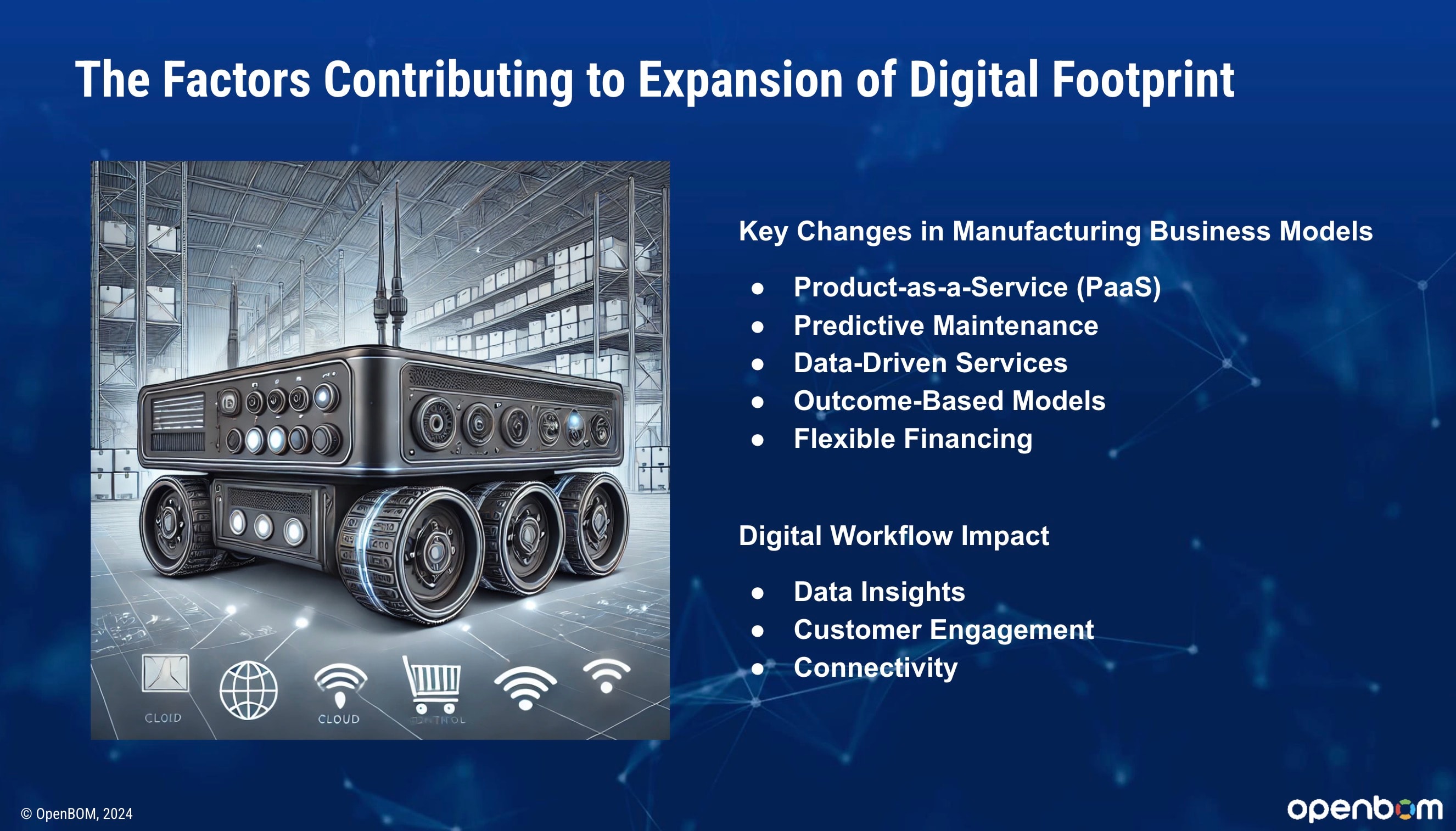
I also explored the evolving drivers of a new digital footprint in manufacturing. Business models are shifting toward Product-as-a-Service (PaaS), predictive maintenance, data-driven services, outcome-based models, and flexible financing options. These transformations are being powered by digital workflows that offer enhanced data insights, stronger customer engagement, and greater system connectivity.
Here is one of the biggest challenges of data management in the manufacturing. Each company has its data silos and disconnected systems. A typical manufacturing environment relies on the files sharing. Even as 68% of industrial CEOs report increasing investments in digital transformation. The concerning reality is that only 25% of manufacturers trust the organization and reliability of their data. While everyone likes to see a full digital environment (check the right side of the slide below), the reality is more like the left side.
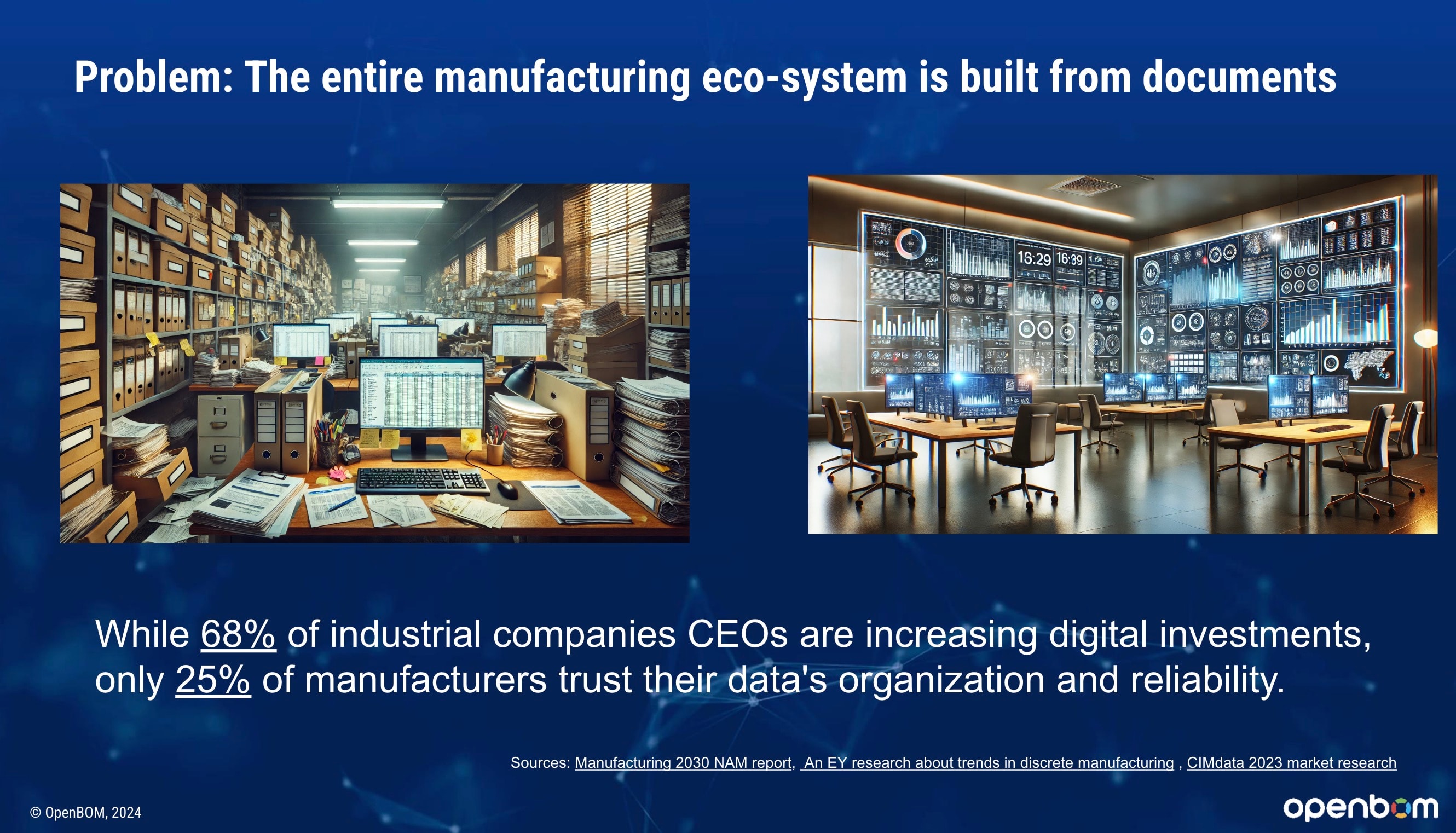
This disconnect underscores the need for a stronger foundation to manage and leverage data effectively, turning it into a reliable asset for decision-making and operations. In the following slides, you can see a trajectory of existing PLM tech and architecture (slide credit Prof Martin Eigner)
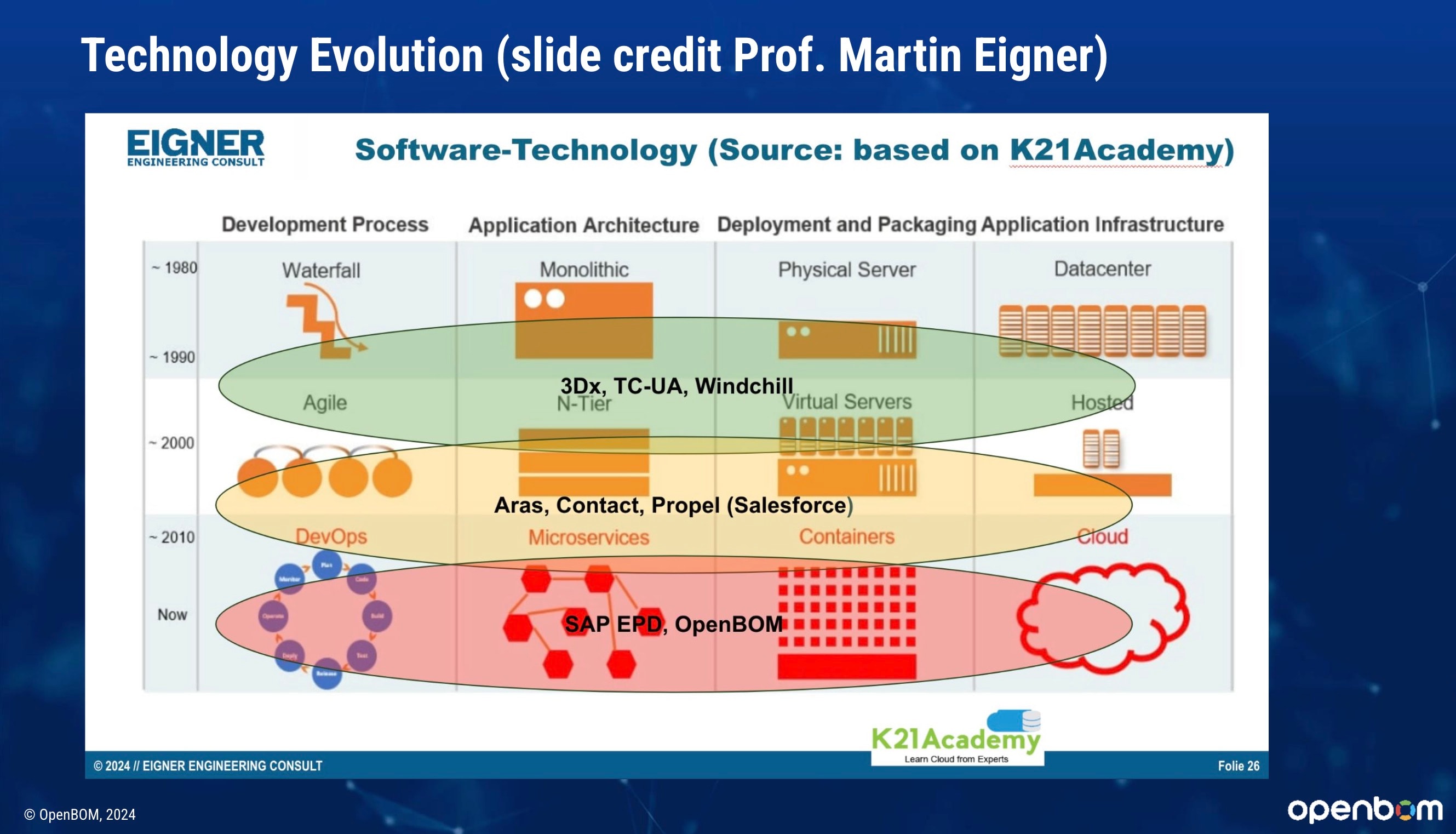
To support this evolution, traditional PLM architectures need to move beyond document-centric models, which lack the scalability and flexibility required to meet the demands of modern manufacturing.
I discussed the potential of emerging technologies, including graph-based data models and linked data architectures, to revolutionize data management and product lifecycle processes. These innovations enable seamless data connectivity, the development of product knowledge graphs, and the creation of a new digital platform layer that integrates with both legacy systems and modern applications.
Here is an example of work done by Martin Eigner and his PhD students in development of graph based semantic system capturing data from multiple enterprise systems to organize the seamless data access and digital thread.
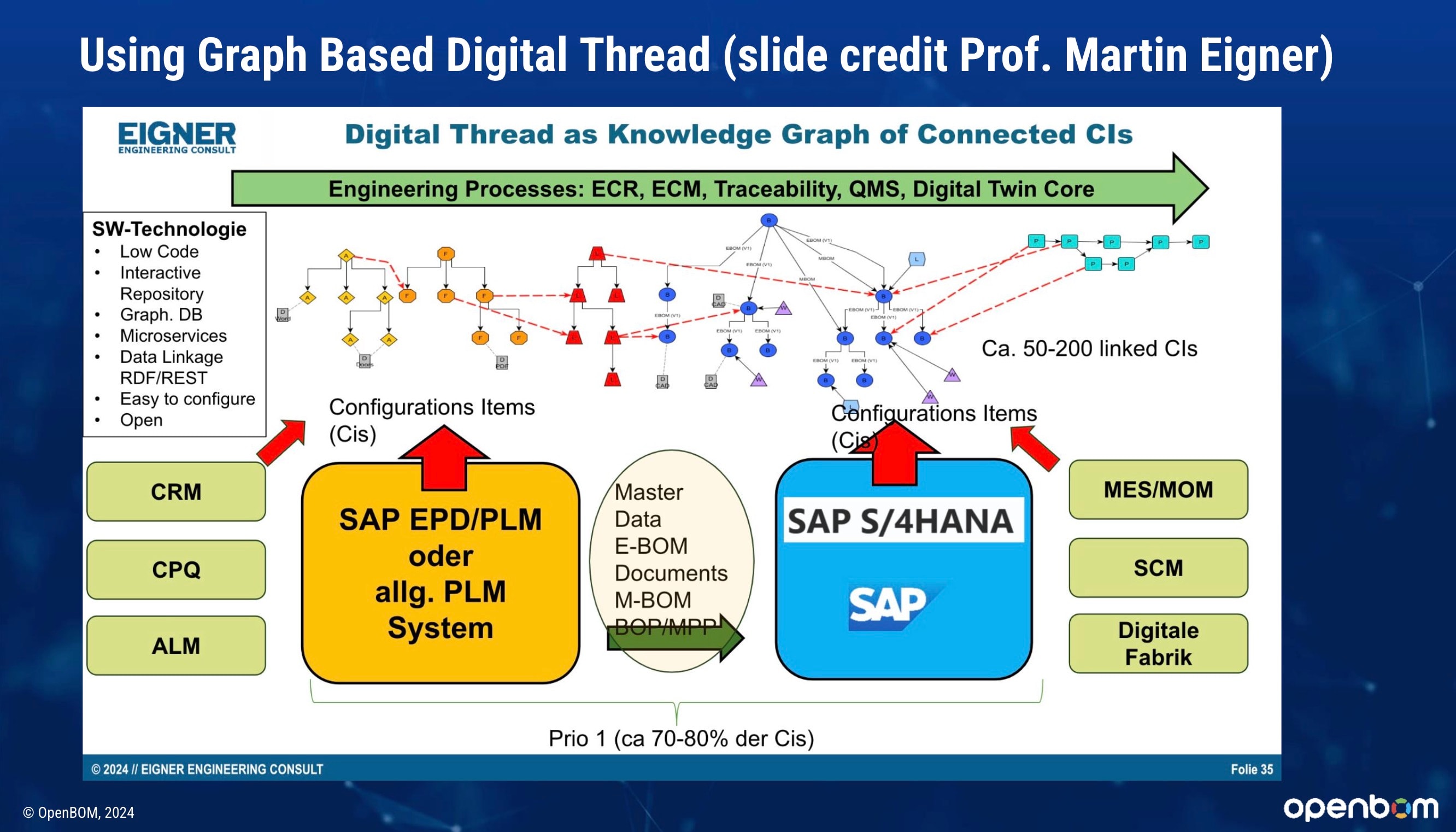
Another example of architecture to support flexible data linking and connectivity between multiple data silos and digital thread is OpenBOM Product Knowledge Graph.
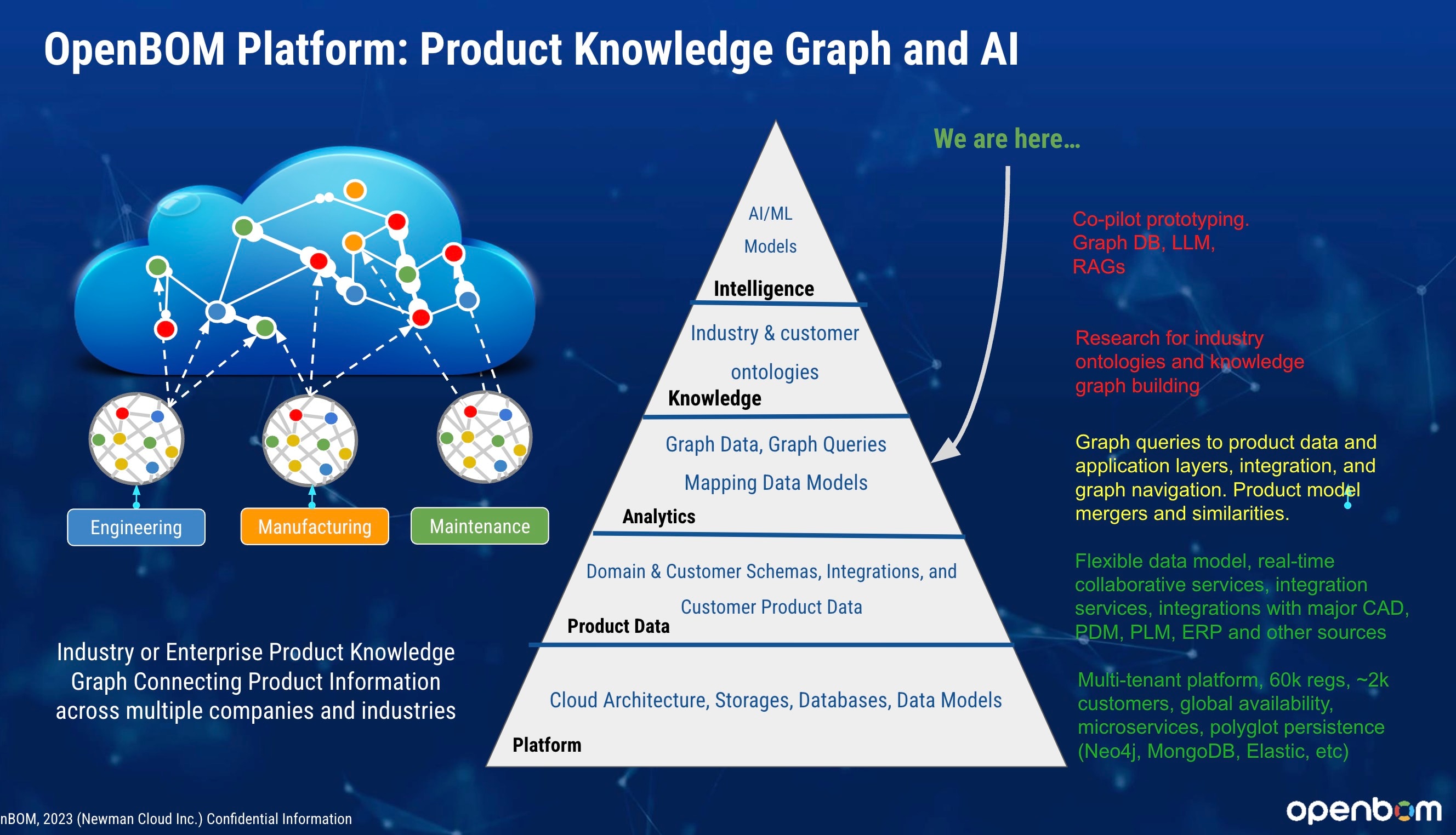
The architecture of OpenBOM supports creating of multi-tenant data management technology and system connecting multiple data silos and organizations.
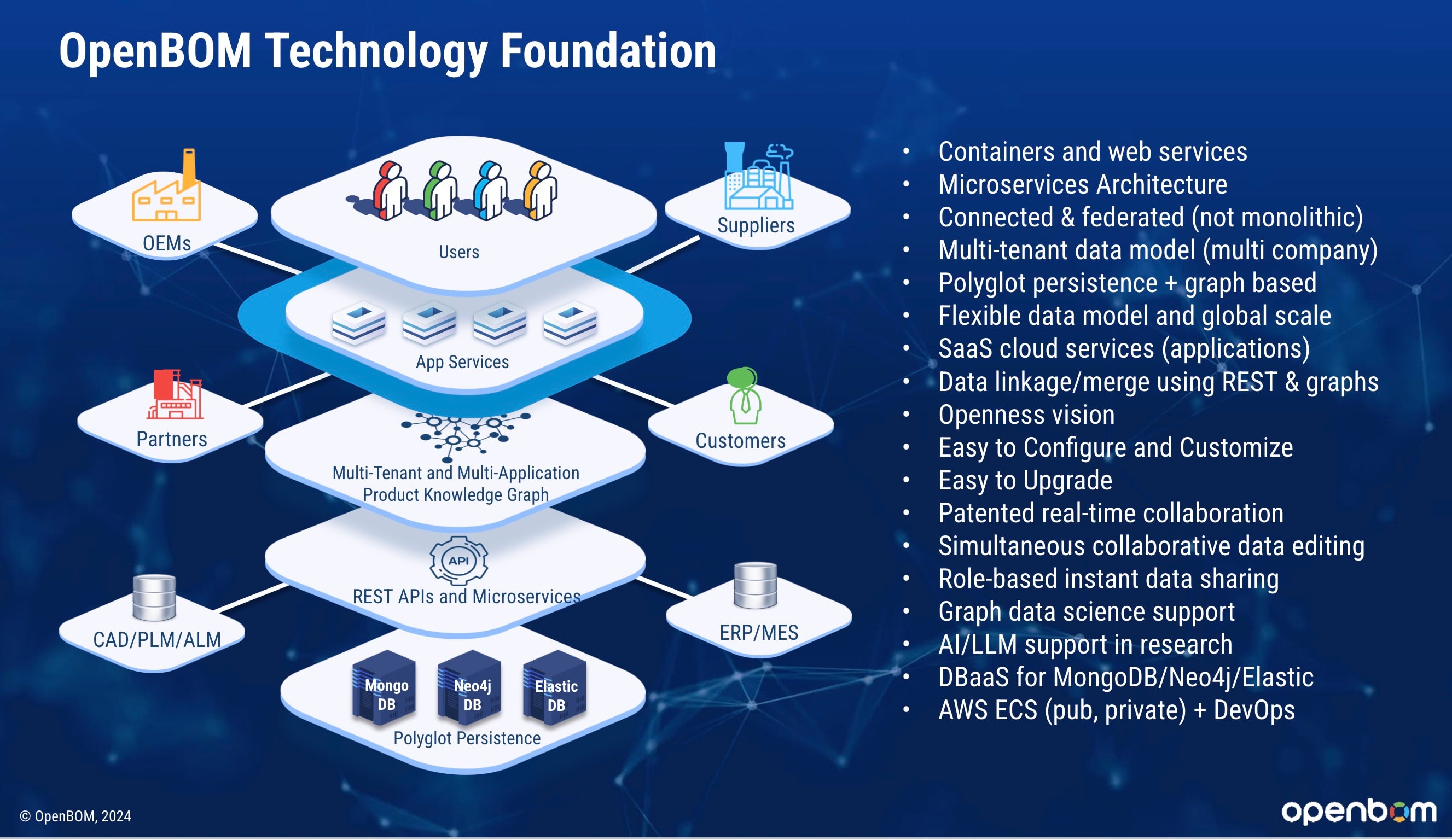
Here are examples of creating an engineering digital thread from multiple design systems using OpenBOM technology.
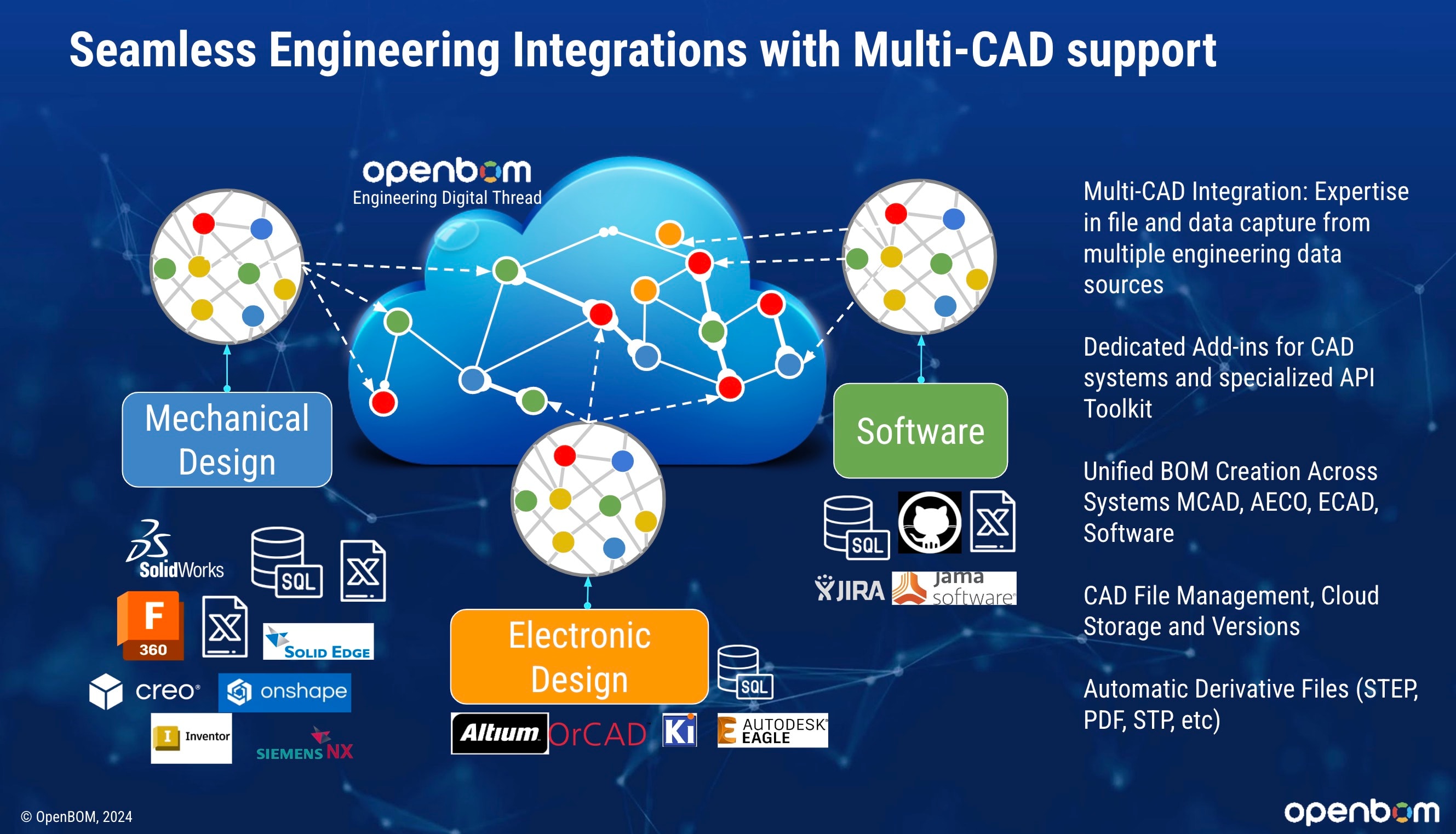
To help manufacturers implement these changes, I emphasized the importance of shifting from document-based approaches to data intelligence, creating open and connected data architectures, and integrating new application services with existing systems. AI tools, when supported by reliable data, can further enhance decision-making and operational efficiency, paving the way for a more robust and connected digital transformation.
You can review the slides from my presentation here.
What is my conclusion and the path forward?
The challenges of data management in manufacturing are real, but so is the potential for transformation. The technological landscape has changed and companies are increasingly looking for ways to leverage digital technologies to create systems that are not only more reliable but also more versatile. There are bunch of things here you can learn and re-use for you company innovations. Cloud made these systems easy available for evaluation and seamless deployment. At OpenBOM, we’ve experienced firsthand how graph-based models and semantic technologies can create a solid foundation for the next generation of digital platforms. As Martin Eigner’s research demonstrates, the key lies in embracing new approaches to product data management while staying flexible and open.
Finally, the technology is here, but as Alan Mendel mentioned in his CIMdata presentation, there is a need for organizational change and focus on business goals to make it happen. Just my thoughts…
PS. I’d love to hear your perspective. Are you seeing similar challenges and opportunities in your digital transformation journey?
Best regards,
Oleg
Disclaimer: I’m the co-founder and CEO of OpenBOM, a digital-thread platform providing cloud-native PDM, PLM, and ERP capabilities. With extensive experience in federated CAD-PDM and PLM architecture, I’m advocates for agile, open product models and cloud technologies in manufacturing. My opinion can be unintentionally biased.