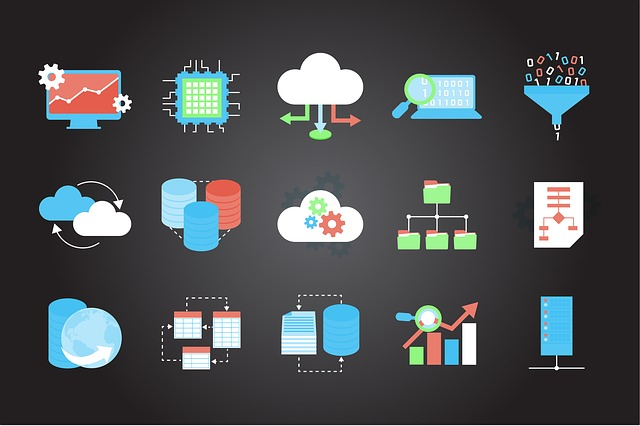
There are a lot of factors to consider when it comes to choosing the best PLM systems and solutions for manufacturing companies. It doesn’t matter if you’re selecting a solution for a startup, SME, or large manufacturing enterprise. The decisions are not simple. In the old school PLM and enterprise software selections, one of the main decision dilemmas was to choose between two fundamental approaches called “best-of-breed” and “single system”. The first approach was taking you to identify the best solutions that you need for individuals, departments, and many possible problems, use cases, and situations. The approach was leading to the need to integrate these solutions together. The opposite approach of selecting a single vendor with a system that is fully integrated, however, might be a compromise in terms of capabilities and other characteristics.
Is the same dilemma still hold in the modern digital realities? Let’s talk about it…
A Day Of Reckoning For PLM Monsters?
Back in the 1980s and 1990s, a long time ago before the idea of digital transformation was introduced, every enterprise software solution provider was building point solutions. Everyone was focusing on a specific aspect of company development – design, engineering production, accounting, manufacturing planning, payroll, taxes, maintenance, compliance, etc.
Between the 1990s and the first decade of the 20th century, ERP and later PLM providers started to play a more dominant role. The realization of how to provide integrated packages became dominant in sales and marketing. Everyone understood that by selling “a single package”, you can get a customer under your full control and continue to sell additional solutions bolted into the same platform. It spurred the wave of M&A activity and the growth of the larger enterprise application suites. In PLM business, CAD vendors embarked on a journey of building enterprise PLM platforms connecting multiple solutions together.
The strategy to sell a “single system” with the emphasis on building a “single source of truth” was very strong (I have to admit that until very recently, the same approach was still very strong in PLM sales and industry). A competing approach of best-of-breed required complex EAI (enterprise application integrations), was expensive and, as a result, many enterprises were leaning towards their system decision. After all, the “no one ever was fired from buying IBM solutions” meme was strong and actively used by large brand names in the industry.
But over time it became clear that the vision of a single system looks good on paper, but it has many flaws in reality. One of the biggest flaws when the vision of a “single system” was based on the strategy of poorly digested acquisitions from multiple companies. Another challenge of building enterprise PLM solutions on old inflexible systems that hard to adapt and develop forward as companies were discovering the need for new features and capabilities driven by new business processes and requirements.
These days, we are living in the time of reckoning for the big PLM monsters we all built. The legacy PLM and ERP monsters that consumed tons of investment from manufacturing companies are fast agings and, as manufacturing businesses are discovering urgent needs in digital transformation, these old monsters are stuck in the middle of the decision about what to do next.
Of course, large brands have big budgets to re-brand their aging platforms with new fancy names and digital stickers, but it doesn’t really help them – their inside is deeply rotten and, as you dig into the solutions they sell, you will find old SQL server databases, PDM application services from the 1990s and other archaic tools. Companies are locked to move forward, and cannot upgrade tools to the new environment and integrate new equipment and processes together.
Rethinking Best-of-breed vs single suite?
How to build a modern successful implementation of product lifecycle management and enterprise resource planning solutions to support business needs and to enable organizations to support digital thread, modern customer experience, agile supply chain management, machine learning, and, on a fundamental level to allow to companies to save money and target audience of their customers looking new capabilities, latest features, real-time integration of product real-time data and services together. What is the new software and new solution that can provide these new capabilities and how to change the selection process enterprise manufacturing companies need to follow to select PLM and other tools to support business today and to conform to all software implementation requirements for products and services?
Integrations and complexity were one of the biggest problems that lead companies to follow the “single systems” strategy. New SaaS, cloud-based solutions, software openness, and modern REST APIs are the foundation of the change coming to manufacturing companies. This is where the “aha moment” is happening and the modern digital thread begins.
Modern digital services do not require long installation cycles and can be immediately available after quick registration. Usage of multi-tenant solutions made enterprise PLM digital services affordable and available instantaneously. They allow to start with simple processes and later expand to support new requirements. These SaaS solutions are in continuous development adding new features, and functionality and making fixes and improvements. There is no need for “upgrades” because SaaS platforms are taking care of upgrades in a transparent and inclusive way.
Finally, web technologies contributed to the idea of how to simplify integrations and deliver it to end users with the need of deploying time-consuming integration service providers developing custom integrations between proprietary software products. REST APIs are secured and can be integrated with reasonable additional costs. Modern secure apps are available on all environments including mobile devices and provide secured access management to all information needed for distributed teams – thanks to powerful real-time data collaboration technologies.
What is my conclusion?
This is not a question about PLM system (or software), but about how organizations manage products across their lifecycles from cradle to grave. The idea is how to look in the time perspective about process management and, most importantly, at the information (data) flow in your company and all connected teams and organizations such as contractors and suppliers. In the past, the idea of “best-of-breed” was introduced as a way to select tools and services that have the best fit for what your individuals, teams, and organization needs. It was a long-standing dilemma of comparing the value of using the right tool for the right job to a single vertically integrated solution coming from a single vendor. Legacy PLM and other enterprise systems are using close data philosophy, complex and experience to integrate. As we move in the world of cloud services, and open and collaborative applications, the opportunity to connect them together and to build a digital thread of product information with a foundation of multiple BOM structures is more and more appealing to manufacturing companies, and contractors, and suppliers. Integration of additional services is easy and very often can be done using the plug-n-play approach. Widely available and easy-to-use REST APIs allow to build integrations and connect information, people and processes together. Just my thoughts…
Best, Oleg
Disclaimer: I’m co-founder and CEO of OpenBOM developing a digital cloud-native PDM and PLM platform that manages product data and connects manufacturers, construction companies, and their supply chain networks. My opinion can be unintentionally biased.