
Manufacturing processes are getting more complex and it leads to an increased level of complexity in the implementation of major enterprise systems – namely ERP, PLM, and MES. To the fairness, I should add CRM, CPQ, and some others to the equation too. But these three are super fundamental for anything that industrial companies are planning to achieve from the manufacturing process standpoint in ETO, CTO, and MTS processes. Before jumping forward, I want to bring a slide that I captured at CIMdata PLM Market and Industry Forum 2023 a few weeks ago. It speaks about PLM investment challenges.
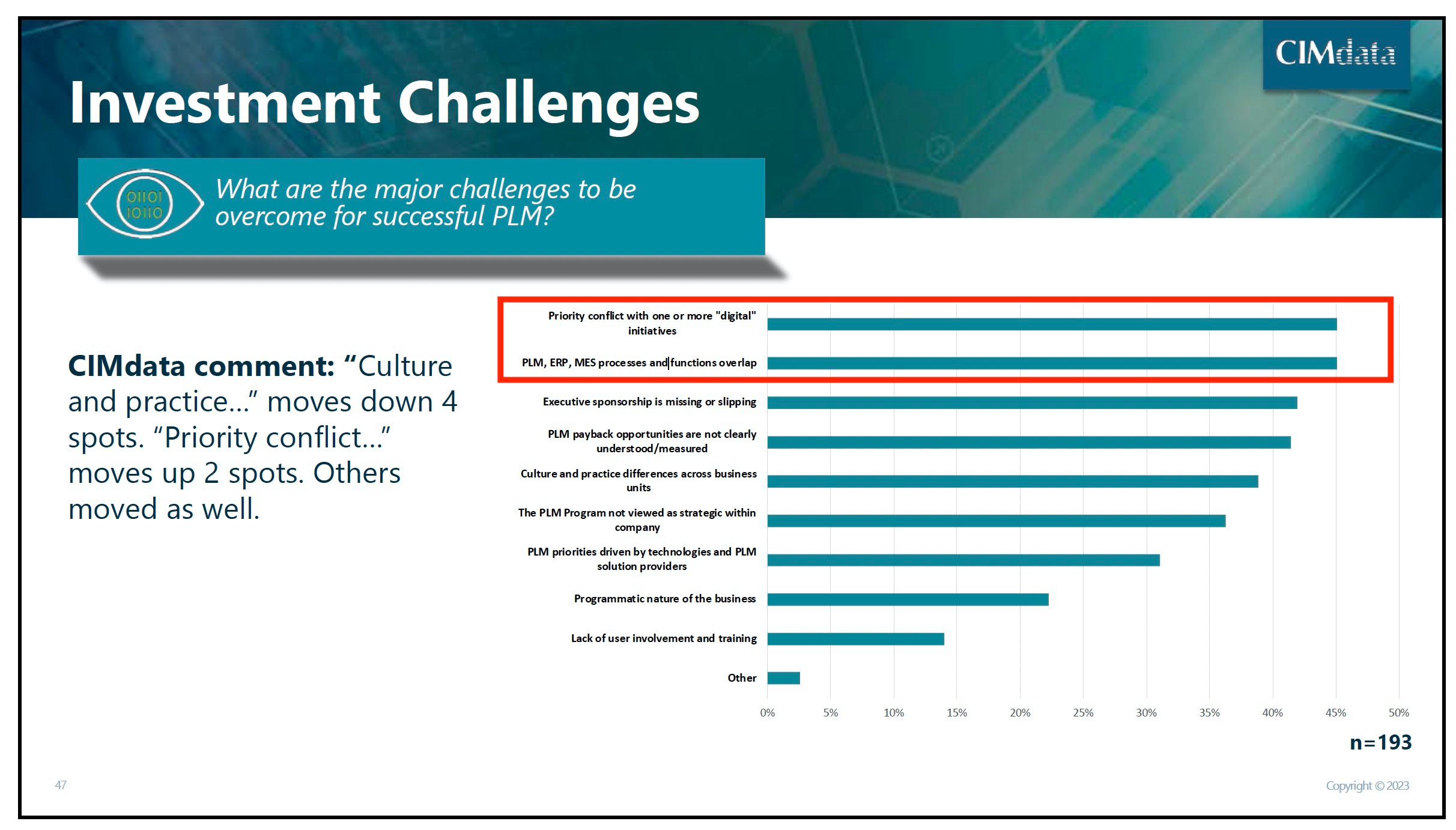
As you can see from the slide, the top two challenges are (1) priority conflict in digital initiatives; and (2) PLM, ERP, and MES processes and functions overlap. I think, the appearance of these two topics on the top of the list, as well as the magic triangle between three major enterprise systems, speaks for itself – companies are struggling in data management, and diverse data sets coming into play when companies are planning their major product lifecycle management processes.
A New Role MES Plays with PLM and ERP?
My attention was caught by multiple articles written by Prof. Dr. Jörg W. Fischer – PLM ERP MES – MES flirts with PLM – the ERP-MES dual relationship finally comes to an end! Check the article here. For all my English readers, including myself, the writing is in German (Google and ChatGPT do a decent translation these days, so you should be able to read it).
Here is the most important passage from the article (translated by Google to English):
The role of MES has changed in recent years. There is a close connection between MES and PLM (Product Lifecycle Management). This is because production requirements have evolved towards personalized, customizable and sustainable production. Since all master data has a lifecycle requires tighter integration of data and processes throughout the lifecycle of a product, from design to manufacturing and maintenance. MES plays a key role here, linking data from PLM to actual processes on the shop floor, enabling process monitoring and optimization.
Therefore, the automation pyramid needs to be redrawn to reflect the closer link between MES and PLM and to highlight the importance of MES as a bridge between product development and manufacturing. The two-way relationship between ERP (enterprise resource planning) and MES is also coming to an end, as ERP systems are often no longer sufficient to meet today’s manufacturing needs. Instead, an integrative view is emerging where ERP, MES and PLM are viewed as part of a larger system that integrates data and processes across the entire lifecycle of a product.
And this is the pyramid, Prof. Dr, Jorg W. Fischer is talking about.
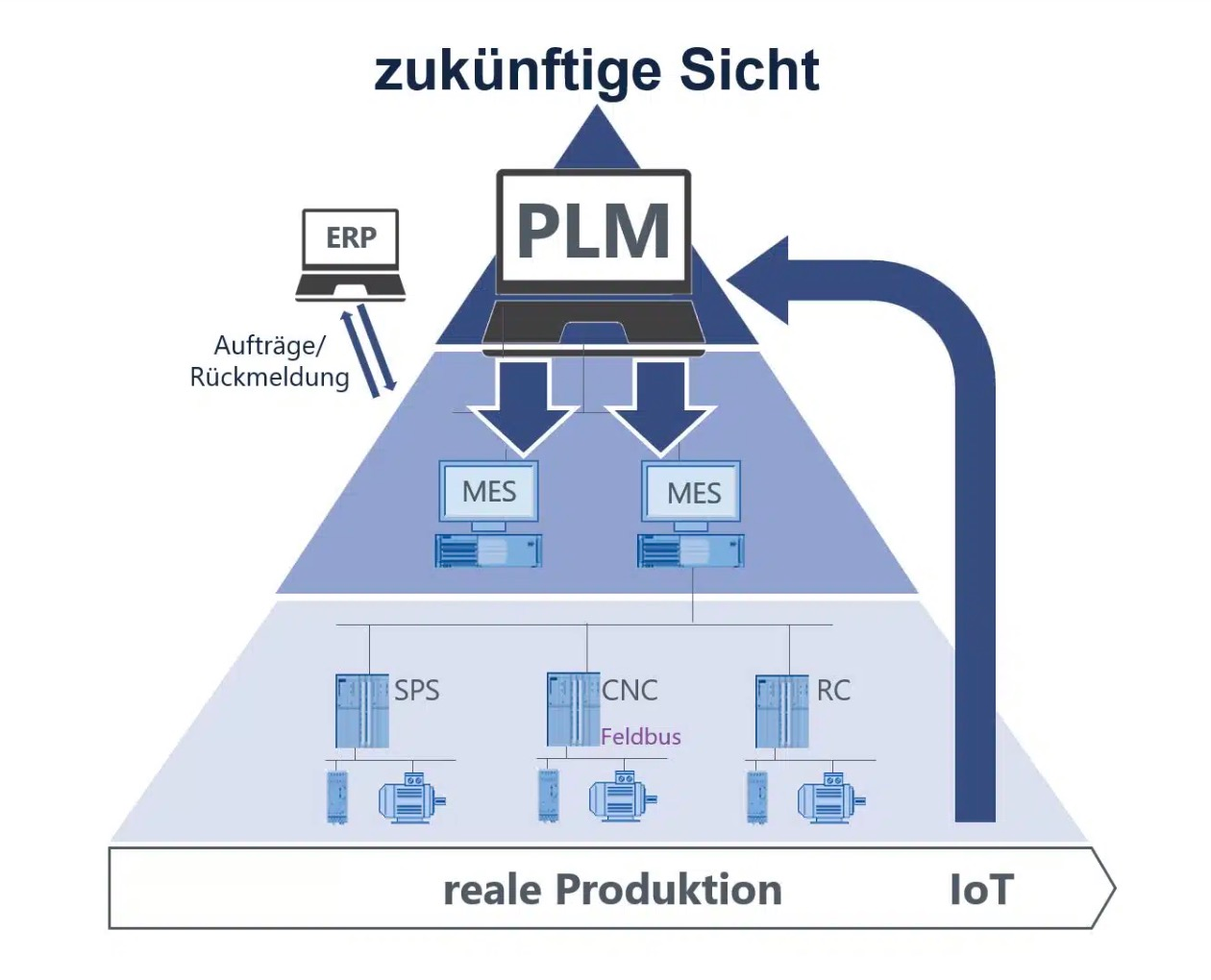
The articles made me think about the topic I initially introduced in my article back in 2016 – How to turn PLM, ERP, and MES into a single 360-degree system. Although more than seven years old, this article is still very relevant because it speaks about the same topic Prof. Dr, Jorg W. Fischer is discussing in his publications – how to seamlessly integrate multiple sources of data – the integrative view is emerging where ERP, MES, and PLM are viewed as part of a larger system that integrates data and processes across the entire lifecycle of a product.
In my 5 blog series – PLM and Digital Thread Evolution, I discussed multiple aspects of how multiple systems of records (SOR) such as PLM, ERP, and MES can evolve into integrated information systems representing a product knowledge graph of all information. Check my article – The Importance of Knowledge Graph For Future PLM Architectures.
Why BOM Conflict?
In my 10-year-old blog – BOM: Apple of Discord Between PLM and ERP, I talked about growing debates about how to organize the most important piece of information – different bills of materials. By BOMs, I mean comprehensive data structures holding information about product data in every system. Here is my summary:
BOM is one of the most important information pieces in product development. It comes on different stages of development – design, engineering, manufacturing, supply, etc. Because of different reasons – technical, political, and organizational, the most widely adopted BOM implementation practice is to split BOM into separate pieces (views) reflecting application domains. At the same time, modern business and manufacturing practices require better integration of processes around BOM. PLM vs. ERP. Engineering BOM vs. Manufacturing BOM. The debates about how to organize them in a better way are heating up in every organization.
Fast forward to 2023. The complexity has grown enormously. At least 3-way communication is needed between PLM, ERP, and MES. Here are my five points of conflict between these environments in traditional PLM implementations.
- Differences in BOM structure: PLM, ERP, and MES systems can have different BOM structures, making it difficult to reconcile the BOM across these systems. For example, PLM systems may have a more detailed BOM structure that includes sub-assemblies and individual components, while MES systems may only require a high-level BOM structure for manufacturing purposes.
- Inconsistent BOM revisions: BOM revisions can be managed independently in each system, leading to inconsistencies in the BOM across different systems. For example, a revision of a BOM in the PLM system may not be reflected in the MES system, leading to production errors.
- Data integration and transfer problems: A variety of data integration issues can occur when transferring data between PLM, ERP, and MES systems. For example, the PLM system may not transfer BOM data correctly to the ERP system, leading to discrepancies in the BOM.
- Lack of synchronization: One of the most fundamental parts of the PLM environment – a single source of truth can be in question when all three systems will go out of sync. BOMs need to be synchronized across different systems to ensure that all stakeholders have access to the latest BOM data. Failure to synchronize the BOM can lead to production errors and delays.
- Part numbers and Identification: Different systems may have different part numbers for the same component, leading to confusion and errors during production. For example, the PLM system may use a different part number for a component than the ERP system, leading to an incorrect part being used during production.
So, what to do about it, and how to solve these problems? For many years, companies were trying to establish clear BOM management processes across multiple systems. Point-to-point integrations were replaced with data hubs, bridges, integration data orchestrations, and many other systems and approaches. While it has had some success and with the right vision leadership and implementation budges was successful, it didn’t bring an ultimate solution for the problem. Therefore I can see it as an opportunity for PLM Product Knowledge Graph.
PLM Product Knowledge Graph Opportunity
The idea of the “PLM Holy Grail” was always around in the PLM community. An ideal ‘platform’ capable to centralize all the data about products and processes was an unachievable myth everyone placed as a vision, but never approached in practice. We might have a chance now. Here is why…
For the last decade, I discussed and worked on multiple opportunities to create an overlay system capable to hold information from multiple sources and domains. PLM-ERP integrations, federated PLMs, integrated semantic search, and cloud-based platforms. These are only a few names to mention. Some of these projects were more successful and some of them failed. However, voices to create an overlay are getting stronger and some examples of these systems started to show up in practical use. Check my article – A post-monolithic PLM world – data and system architecture, which will give you an idea of how companies can achieve the goals of the overlap in a future data-driven environment. More article to come. Stay tuned…
What is my conclusion?
To make things happen you need a combination of three main factors: (1) Technological maturity; (2) Organizational readiness; (3) Major trends to support the transformation. We might be coming close to fulfillment of all three, which was not the case for my last 20+ years in the PLM industry. All together, it makes me think that the technologies that were developed for the last 15+ years combined with the digital transformation of industrial organization combined with critical aspects of the industry and major geopolitical trends (supply chain, manufacturing transformation, etc.) can create the environment to make industrial companies to make a switch. Human civilization has undergone multiple large phase transitions – agricultural, industrial and these days we are in the next “networked” technological transition.
Just my thoughts…
Best, Oleg
Disclaimer: I’m co-founder and CEO of OpenBOM developing a digital-thread platform with cloud-native PDM & PLM capabilities to manage product data lifecycle and connect manufacturers, construction companies, and their supply chain networks. My opinion can be unintentionally biased.