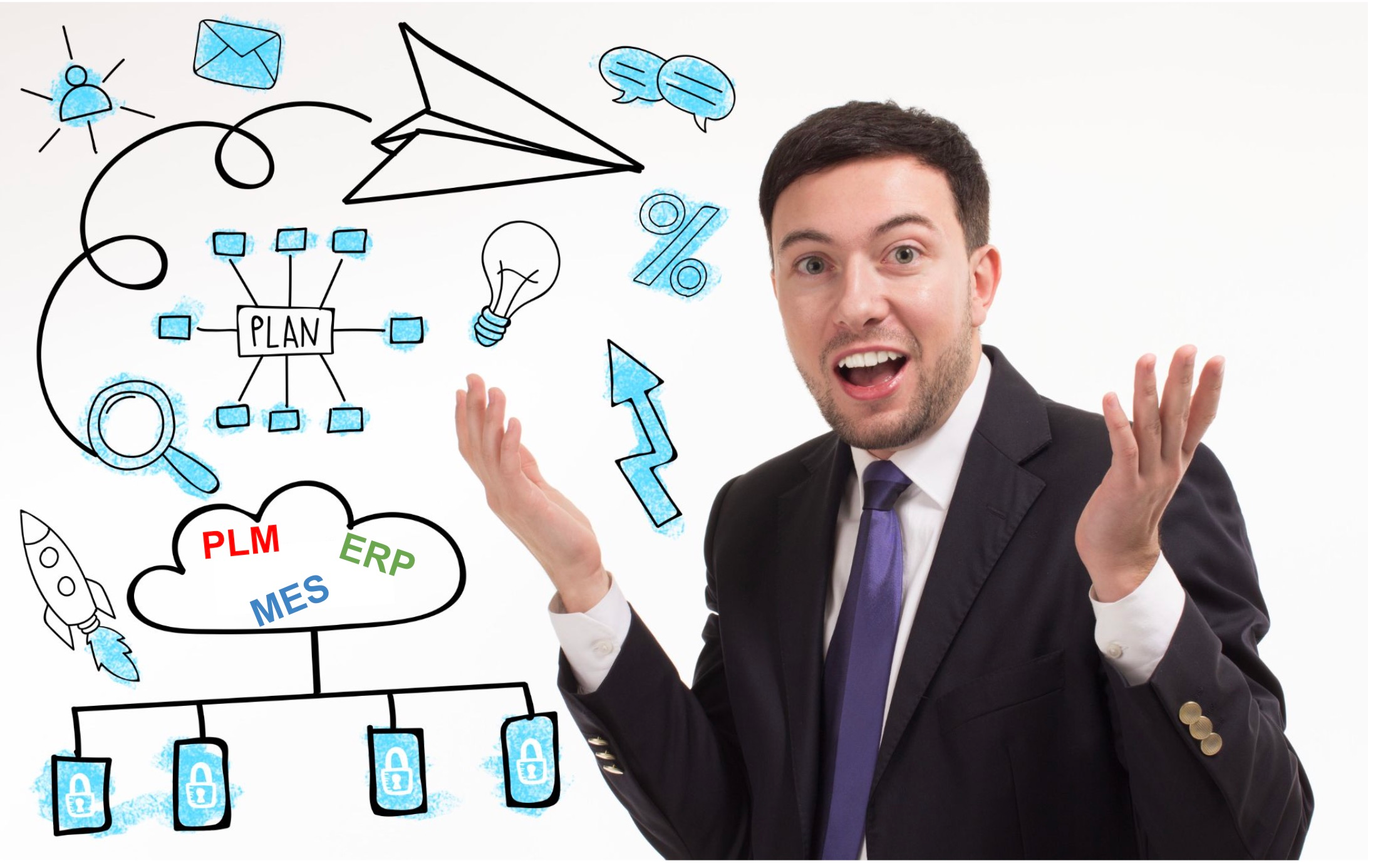
The question “PLM vs ERP” is often coming when I’m talking to companies, or people solving engineering and manufacturing process problems. Many companies, particularly startups, often grapple with this pervasive question, “Do I need a PLM (Product Lifecycle Management) system, or should I opt for an ERP (Enterprise Resource Planning) solution?” If you google this question, you will find tons of articles coming from multiple vendors explaining why starting from one or another solution is important. PLM vendors are in particular great at explaining why PLM must come before ERP. Better articles will explain to you that PLM and ERP are the perfect match and they need to live in harmony. But the real answer is different. Let’s talk about it.
Each engineering system (no matter if you call it PLM, ERP, product innovation, or virtual twin solution) is practically a bundle (a package) of tools to solve specific problems. Each software company packages it based on its strategic belief and ICP (ideal custom profile) they sell to. While it is perfectly fine for a software business, it doesn’t help you as a customer trying to figure out what you need.
Here is a common misconception I’ve seen many times – the belief that focusing on these three-letter acronyms (TLA) and their corresponding bundles will somehow magically solve all operational inefficiencies. Guess what – it will not help. You typically end up with a bunch of disconnected software packages and bigger problems.
The primary source of confusion lies in a misunderstanding of what these systems are meant to achieve. Instead of focusing on the bundle definitions of what vendors sell as PDM, PLM, ERP, MES, and other solutions, it’s far more beneficial to shift focus toward understanding your company’s specific needs, and how to optimize data, process, and people. These names (PLM, PDM, ERP, etc) reflect traditional software business “packaging” of solutions, which may not necessarily apply to the state of process complexity in your company or specific needs and business processes.
Here are a few steps to help you navigate the landscape of software solutions for selecting the right approach in organizing product development, supply chain, and manufacturing:
1. Analyze your People, Process, and Data
Start by analyzing the people you work with, the processes you need to support, and the data you need to handle. You’ll want to understand how your teams interact, what workflows need to be optimized, and what kinds of data you’re working with regularly. This analysis is a fundamental part of the ‘Unstoppable PLM Playbook’. Just as an example, if you build custom projects (eg. complex engineering equipment) that take 1 year to complete, your product development process can be completely different from building some electronic gadget (software wrapped in plastic) and selling it to thousands of customers initially. If your production process requires an assembly line in-house you need different software (and process support) rather if you work with contract manufacturers and outsource your design and production.
2. Reverse Engineer your Needs
Once you have a clear understanding of your people, processes, and data, begin to think in reverse. Which systems can handle the types of data you need to manage effectively? What systems support the processes you have identified as crucial? Which ones provide a satisfactory user experience to your teams?
It is important to start from data because it is the foundation of all processes and the outcome is directly dependent on how efficiently you can manage the data you have. For example, if your product is a simple set of 9 components, focusing on a complex bill of materials solution might be an overkill. However, if you build a complex and configurable product including mechanical, electronics, and software components, you better find a way to manage the complexity of BOMs and all information. The same about processes, regulatory aspects and user efficiency, and user experience. Think about data handovers, which are becoming really critical in modern product development and manufacturing – moving data between systems can be painful and lead to many mistakes.
3. System and Service Selection
Having delineated your business process needs and understanding the manufacturing process you need to support, you can now consider different systems and services. Keep in mind, it’s not about selecting a PLM or an ERP per se. Instead, you’re looking for a solution that best aligns with your needs – one that can manage your data properly, support your processes, and provide a seamless user experience.
It requires a bit more time than selecting a specific ERP system or PLM system but makes your hands dirty to understand the features, functions, and capabilities of the system. Here is the good news – in a modern SaaS world you should be able to try any software you want to buy before making your decision. The days when manufacturing companies were buying PLM software based on PowerPoint slide decks are finally over. Actually, if you cannot get a system to try and a company is offering you instead to speak to their salespeople, I’d call it a red flag. Nothing wrong with sales, but the fact software is not instantly available to you is an indicator of how the software system is built (think about companies hosting old PLM/ERP packages using AWS or Azure. They cannot host the instance of the software before you buy it, because it is costly. So, ask for a 2-4 weeks trial to check the software firsthand.
Once you’ve got access to the trial, focus on how to get a specific data set or handle the most important data and functions to support the process you need. For example, the creation of BOMs, procurement, or shop flow assembly functions. Focus on data and process, but not on TLAs.
4. Stay Agile and Adapt
You may think that the process I described above is mostly applicable to small manufacturing businesses and startups. Actually not. The same process applies to large businesses. Let’s say you selected a system for a small manufacturing company with 10 engineers working with multiple CMs and you’re growing. As you do so, your supply chain management, engineering process, and manufacturing methods will be changing. Which will trigger a software “retooling” and replacement. Even when your business is scaled up and running smoothly, it’s essential to maintain a growth mindset. The same about very large companies. Focus on how to measure your current processes and how to improve them will lead you to the next set of improvements. It is part of the Unstoppable PLM playbook mindset – focus on how to measure business performance and goals, setting KPIs, and selection of system capabilities to be implemented. Once you passed a full circle of technology selection, process, data, and user experience implementation, get back to the measurement of a business outcome and get ready for the next agile unstoppable PLM cycle.

Keep in mind – always focus on addressing business challenges and repeat the ‘Unstoppable PLM’ exercise as necessary to decide what you need at any stage of your manufacturing process development. No process is staying frozen. Selecting a specific PLM system or ERP software won’t solve the problem forever, you need to select the tool based on your needs and analysis and then evolve as you grow.
What is my conclusion?
Traditional “packaged software envelopes” such as PDM, PLM, ERP, etc. can indeed be confusing. It can happen if you select a solution for a manufacturing startup or if you think about how to “retool” a large enterprise manufacturing business. You should focus on the specific process, data, and user experience needs of your business before jumping into a sea of “bundles and TLSs”. By focusing on the specific needs of your business rather than the software solutions themselves, you can better navigate this landscape and decide what software service you need.
Modern enterprise resource planning and PLM software systems are coming using the SaaS model that allows you to evaluate and have first-hand experience with the system. Also, keep in mind things like how easy you can get support and fixes if something will go wrong. Buying from small and agile companies can give you an advantage because these companies are building software and collaborating with their customers. Be careful with 10-20 years old PLM and ERP systems “frozen in life” and companies that stopped making changes in them a decade ago.
Remember, TLAs and packaged bundles can be confusing, but you don’t need to focus on them – they are not solutions in themselves. The key to optimizing your operations lies not in finding the “right” tool, but in understanding what work and function you need the tool to perform. Just my thoughts…
Best, Oleg
Disclaimer: I’m co-founder and CEO of OpenBOM developing a digital thread platform including PDM/PLM and ERP capabilities that manages product data and connects manufacturers, construction companies, and their supply chain networks. My opinion can be unintentionally biased.