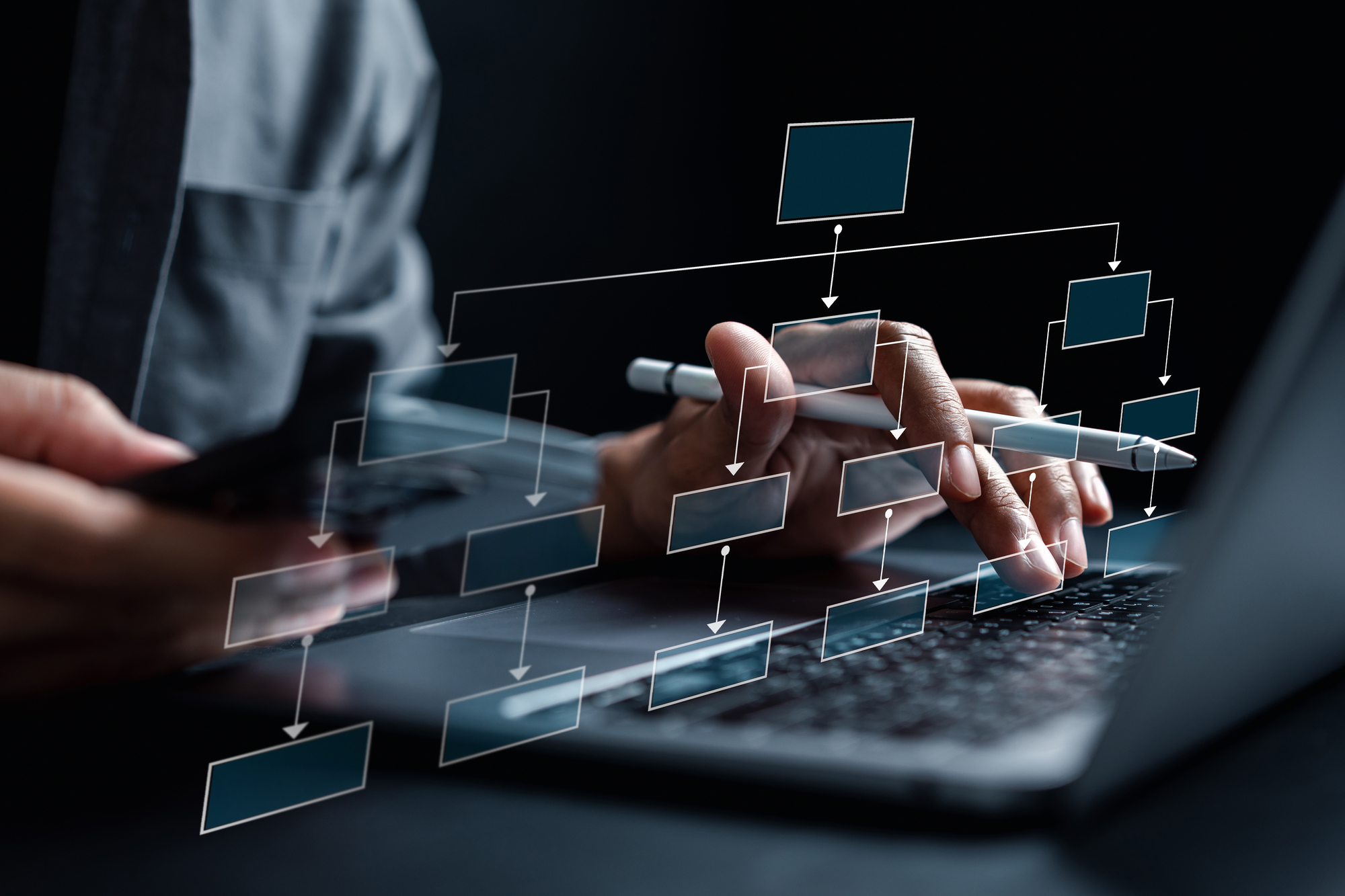
Product Lifecycle Management (PLM) and enterprise resource planning (ERP) systems represent the foundation of the product development and business processes. They support multiple aspects of product development processes – computer aided design, engineering, manufacturing, production, supply chain management and many others. The connection of these two systems is one of the most disputable topics when it comes to implementation of business processes in the manufacturing industry. It is important for a wide range of use cases from mass production to engineering to order (ETO) and configure to order (CTO) processes.
For the last few months, I’ve been following a few very interesting conversations on LinkedIn lead by Prof Martin Eigner and Prof Jorg Fischer about managing of data in both PLM and ERP systems and complexity of mapping and integrations product development and manufacturing processes that dependent on the interplay between PLM and ERP. As such the topics that draw my special attention were related to 1/ Part revision process and how it impact PLM/ERP data management; 2/ Managing EBOM and MBOM, and 3/ Managing of Drawings and MBOMs in bother PLM and ERP software.
In this article, I want to share my thoughts about what makes PLM and ERP complex together and how to bridge these systems to support modern product development. Also, I want to talk about three possible ways to integrate and bridge both PLM and ERP systems:
- Simple Synchronization
- EBOM to MBOM process
- Digital Thread Product Model
Let’s get into more details and start from what problem we need to solve.
What problems are we trying to solve?
Every company I ever came to implement and support engineering and manufacturing processes, I eventually came to the point when the question of integration between engineering systems (CAD, PDM, PLM) and manufacturing (MRP/ERP) systems arose.
Very often, the question was bluntly asked as – how to sync engineering data to ERP. However, a few steps down to the understanding of the problem, it became obvious that even if the task (sync data to ERP) sounds simple, the reality is that there are two separate processes that operate using different rules. How to bridge these two processes together and support using systems a company has in place is the problem that companies are trying to solve.
The history of both worlds (PLM and ERP)
Both PLM and ERP systems went through the complex process of evolutionary development, which made them as we know them today. To understand these historical steps is important because they give you an idea about gaps (both functional and architectural) and might give you an idea of how to resolve the problem.
Historically, engineering was presented by a “drawing” (later CAD system), and manufacturing was presented by an MRP (BOM) managed system. If you’re looking into the roots, I recommend these two books that represent the best of “classic” BOM management and MRPII planning: Orlicky’s Material Requirements Planning and Dave Garwood: Bill of Materials for lean enterprise books.
Historically, the engineering process was ended by the creation of a Drawing, and MRP was focusing on the management of a “single” BOM focused on material planning and scheduling. The role of engineering was to finish a design and make a drawing with the Part Number (usually equal to the document number), which was thrown over the wall of manufacturing for production (procurement) planning, production scheduling and order management. Together they represented business management software that is expected seamlessly integrate and work together. But they are different…
The engineering world was managed by “revisions” of documents. Each design iteration was ended by a new drawing with a specific rev that later was sent (and saved) in the MRP system associated with a specific Part Number. There was no reason to revise the part number as long as all changes in drawing revisions were interchangeable. Once engineers made a non-interchangeable change, a new Part Number was created (blind man rule).
To conclude, the engineering (design) structure was managed by a document “revision,” and the manufacturing (planning) world was managed by a part effectivity (date) to control procurement and assembly process.
What is different in a modern PLM and ERP environments?
The modern industrial revolution and the evolution of both engineering and manufacturing processes created the environment where complexity dictated new rules. Product complexity, including configurations, mechatronics, and software, is combined with ordering processes (ETO, CTO, BTO), and global manufacturing introduces an overall complexity of data management before a product even leaves the manufacturing dock. Beyond that, complex product maintenance, connected products, reconfiguring products using software components, and changing business models (selling services, not products) are making product development and data management complexity skyrocket.
Here is the problem… Both systems for product lifecycle management (PLM) and ERP (MRP) developed and advanced for the last 20-30 years are still conceptually using the same model – revision lifecycle on the engineering side and effectivity/FFF rules on the side of MBOM management.
In a spirit of fairness, both systems developed different processes in a “grey” and overlapping space. Some ERP mechanisms adopted revision control (especially for document management), and PLM has developed advanced BOM management to support enterprise BOM with different BOM representations (eBOM, mBOM, sBOM, etc.), also introducing mechanisms of effectivity in BOM for both variants and dates.
3 Ways To Bridge PLM and ERP in 2024
As manufacturing companies are exploring digital transformation and looking at how to streamline processes, the question is how to intertwine digital processes involving both PLM and ERP is becoming more critical. In my article today, I wanted to share some ideas about how companies can bridge both PLM and ERP systems.
Simple Synchronization
KISS (Keep It Stupid and Simple). This method is often the simplest one to integrate engineering (PLM) and manufacturing (ERP). Keep both systems separate, define attributes in a data model that can help sync data between systems. Usually, those are Part Numbers with some additional parameters in the PLM system that can help to identify Item (Material) Master. Syncing data (usually one way from PLM to ERP) and sometimes updating Part information back from ERP to PLM – this is the scope of these integrations.
Implement EBOM-to-MBOM Process in PLM
This approach is based on the expansion of the PLM system and the implementation of both EBOM and MBOM in the PLM system. The advantages of this model are to have full control over the engineering to manufacturing process, including BOM restructuring, ECO, and other elements of data mapping done in the PLM system. The outcome (MBOM) is synchronized with ERP bidirectionally to keep the ordering/procurement process performing its work.
Bridge Product Model and Develop Integrated Application Services
This is one of the most advanced approaches. The core element of this integration approach is a comprehensive advanced product model that is capable of holding multi-application data covering multiple disciplines. It includes a semantic model of product data and its relationships and is capable of supporting business process applications using both PLM and ERP system APIs. This approach was first introduced in different “integrated hubs” used for EAI and EBS systems, later used by various Integration as a Service systems.
A growing interest in the development of bridge product models can be explained because these models can also go beyond “integration” logic and provide a variety of services to implement Digital Thread solutions. Check my earlier article – How to build a product model for digital thread.
What is my conclusion?
Modern development of digital processes and complexity of product development, manufacturing, and maintenance created a demand for more advanced “process-oriented” services to support integration of both PLM and ERP systems into a single digitally connected solution. Although early days “transactional sync” systems are still functional and relatively simple to implement, I can see “bridge models” taking a leadership role in the future process of creating a digitally connected environment. Just my thoughts…
PS. What tools can be used to bridge PLM and ERP and how they can be implemented is a separate topic. I will talk about it in my future articles.
Best, Oleg
Disclaimer: I’m co-founder and CEO of OpenBOM developing a digital-thread platform with cloud-native PDM & PLM capabilities to manage product data lifecycle and connect manufacturers, construction companies, and their supply chain networks. My opinion can be unintentionally biased.