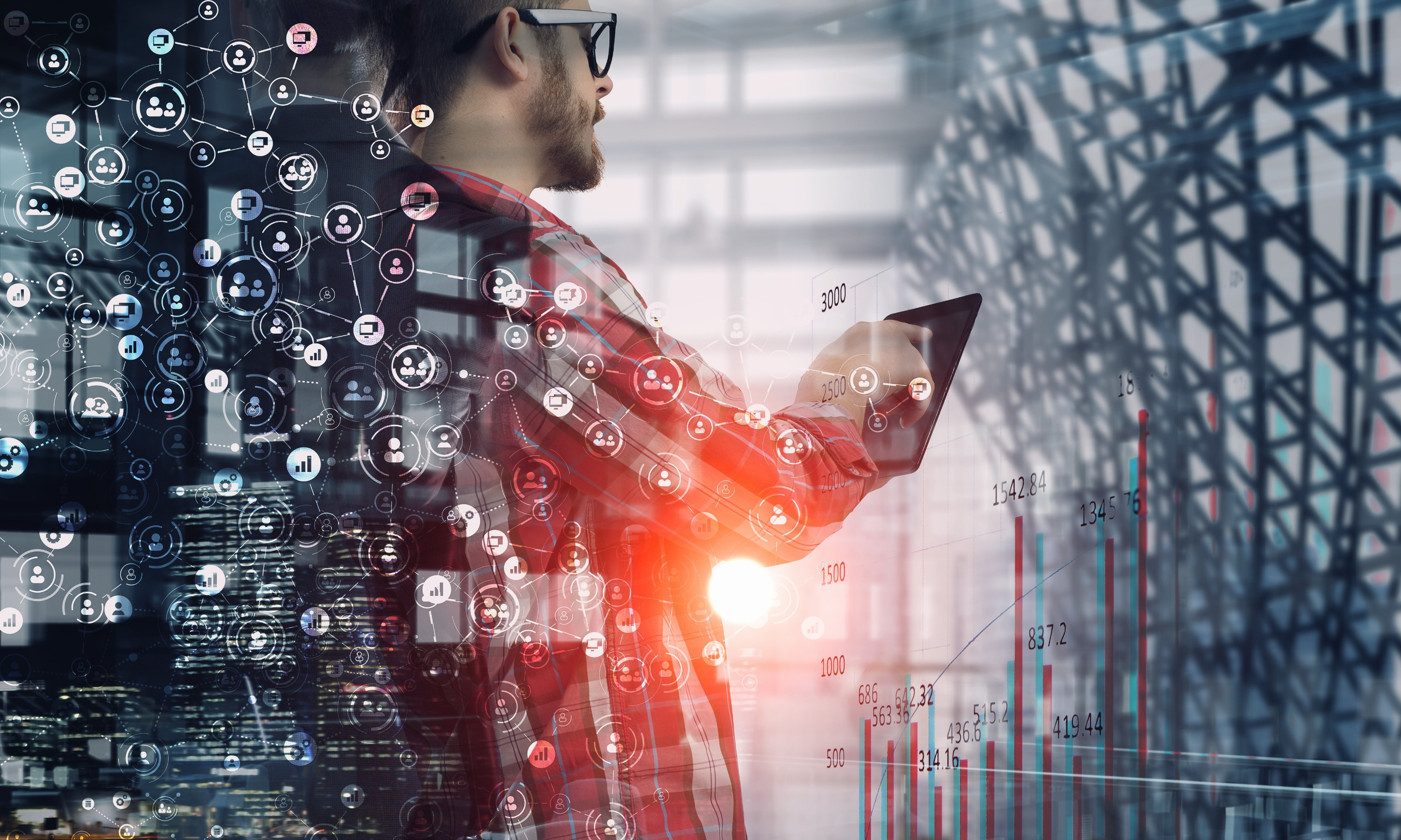
In the land of product development and manufacturing, the traditional Product Data Management (PDM) systems have long stood as the backbone, ensuring the structured organization, storage, and retrieval of product-related documents.
According to the reviews of analysts to find that traditional use cases are still dominant in PLM and most of them are focusing on CAD data management and engineering release data management. Here is my article from the last year after CIMdata Industry and Market Forum summarizing mytop 5 important things about the state of PLM in 2023.
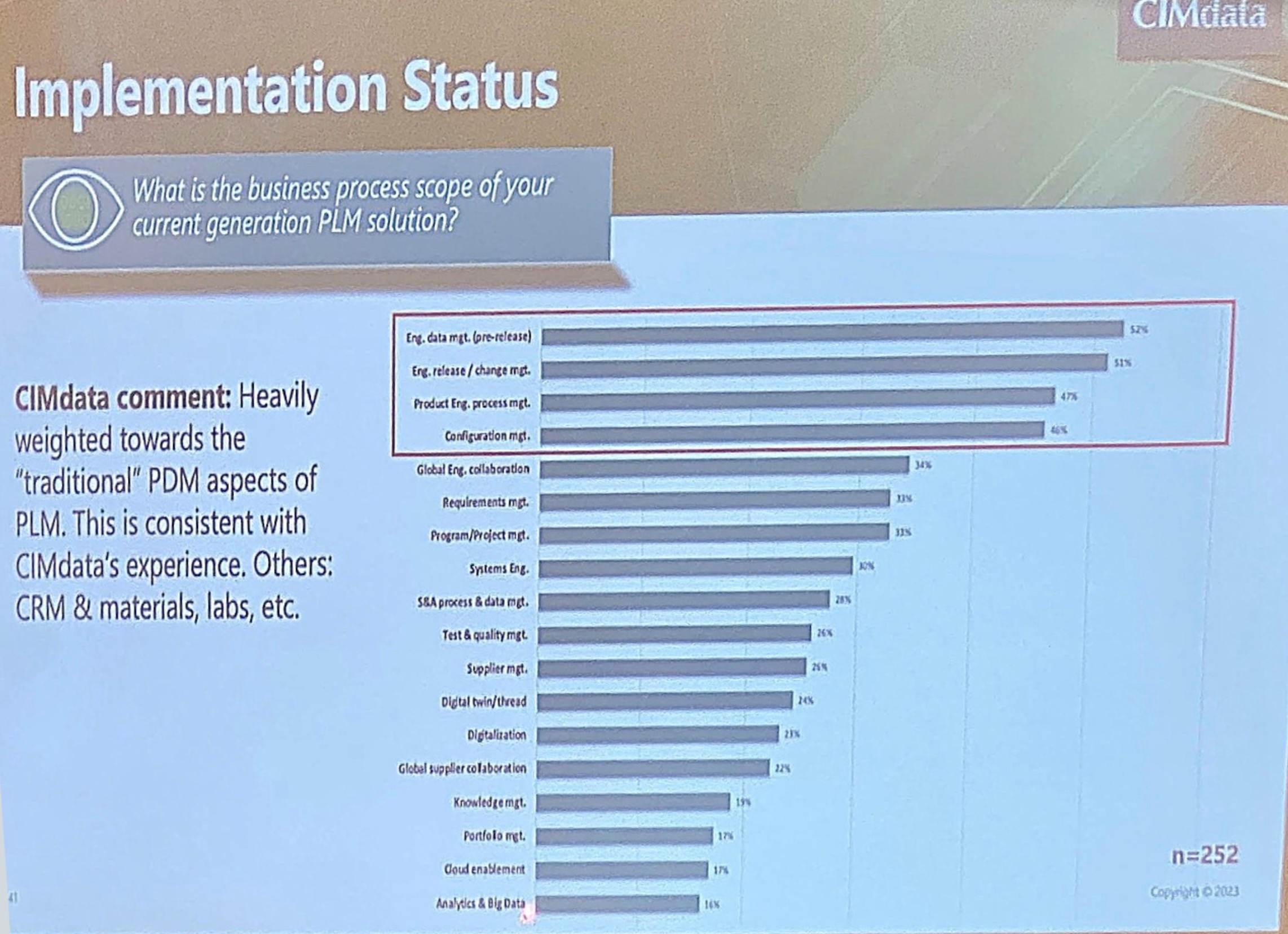
However, as industries evolve and explore digital transformation, the limitations of these document-centric paradigms are becoming increasingly apparent. The document driven model is limited. At the same time, there are top three challenges in a manufacturing when it comes to the point of how to manage data:
- Complex products including mechanical, electronics, software systems working together
- Distributed nature of business processes when multiple companies need to work together
- Legacy software systems, including traditional product data management and document management software heavily relying on document-centric approach.
The future lies in a more dynamic, efficient, and interconnected approach: transitioning from documents to data-centric models. This shift promises to revolutionize how organizations handle product information, making processes more streamlined, innovative, and aligned with the digital transformation era. Let’s talk about it in more details.
The Limitations of Traditional PDM Systems
Traditional PDM systems focus on managing files and documents related to product development, such as CAD files, design documents, and specifications. While they provide a structured way to store and access these documents, they inherently focusing on a traditional scenario of changing files and engineering document approval. While this is a very important process by itself, it creates a siloed approach when engineering data is separated into document management software (traditionally each CAD system is offering its own PDM system). Even if PDM system is capable to manage files from multiple CAD systems, the approach is to manage revisions of these documents and to get a “released set of document” for each specific CAD at the time when change is actually made.
These result of this process create silos of information, making it difficult to integrate data across different departments and integrate computer aided design (CAD) between multiple disciplines and software platforms. Imaging MCAD, ECAD, PCB and ALM systems each working independently as document management systems and producing not synchronized output for the release process.
As a result, organizations face challenges in collaboration, data consistency, and real-time data access, which are critical in today’s fast-paced market environments. You will get a released set of document from MCAD separately from PCB design and also out of sync with the software team using different tools. How to solve this problem?
The Rise of Data-Centric Models
Data-centric models represent a paradigm shift, focusing on the data itself rather than the documents that contain the data. In this approach, data is stored in a structured, interconnected format, accessible by various applications and systems. This model facilitates a more holistic view of product information, enabling seamless integration across different platforms and departments. By prioritizing data over documents, organizations can enhance collaboration, improve data quality, and accelerate decision-making processes.
How to implement data-centric models to support design and engineering product development processes? There are two important elements of this transition process:
- Introducing flexible data records capable to manage information and use file as an attachment.
- Enabling real-time collaboration features and allowing to data and files to stream freely and (most importantly) asynchronously from multiple data sources to a consolidated multi-disciplinary data structure.
Here are a few examples of such approach implementation I found with systems like Autodesk Fusion360, OpenBOM and PTC Onshape.
Check the picture below and the article about how to collect data from multiple document management systems (PDM) and design data sources in a single multidisciplinary data set with all product related data.
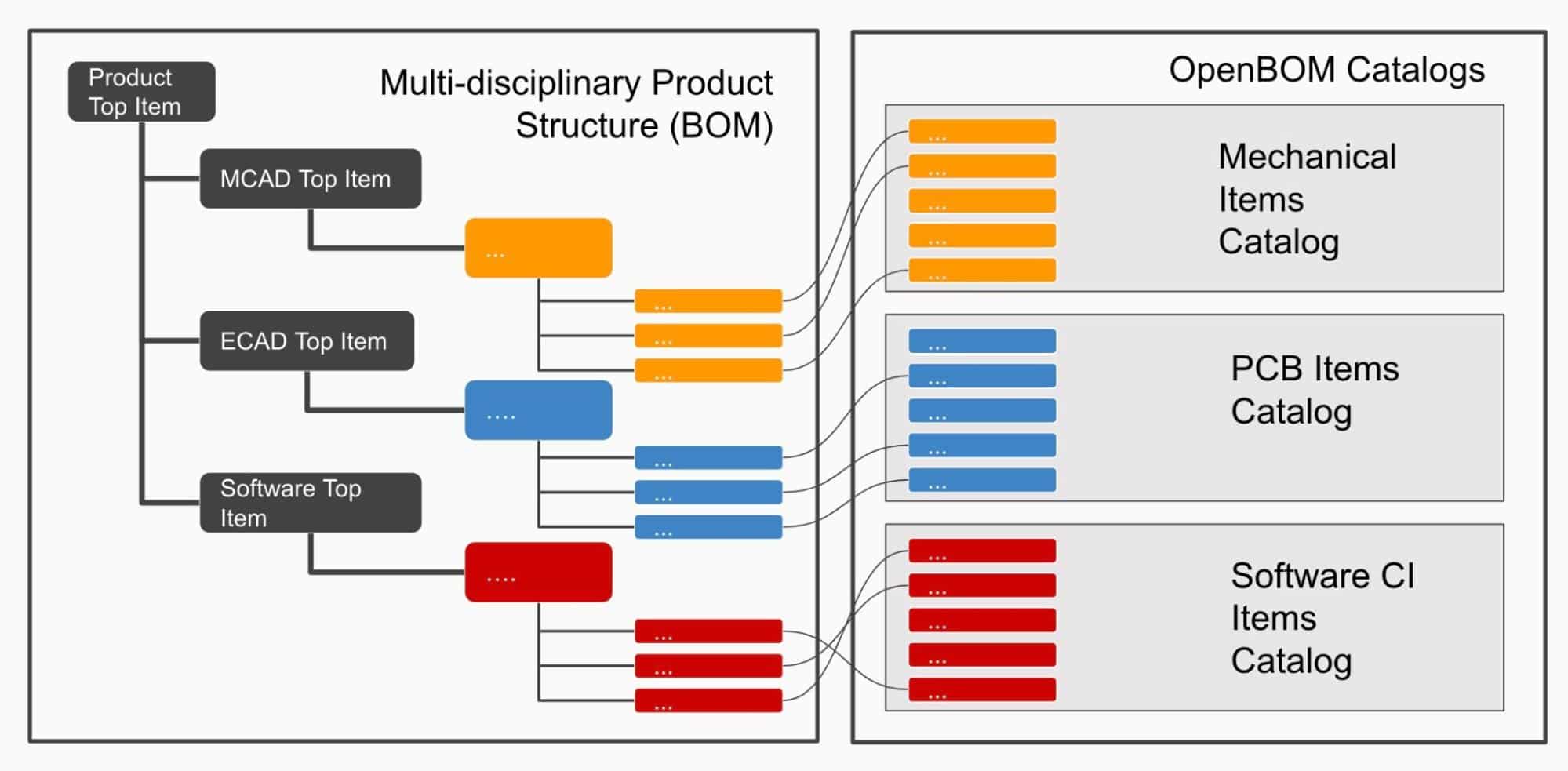
Onshape Team collaboration feature allows to multiple people to make changes simultaneously and allowing to edit information by multiple engineers without data locking.
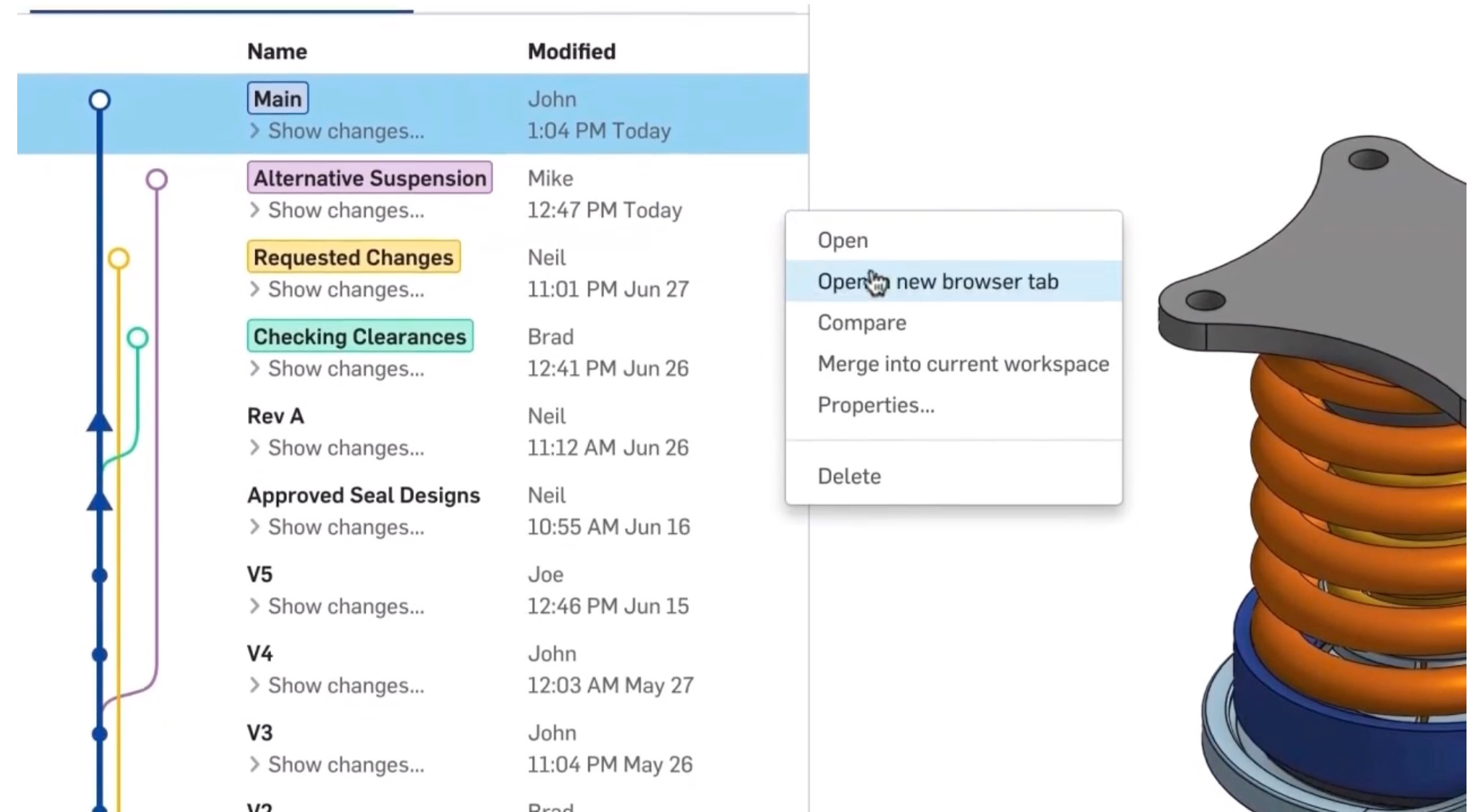
Another example of data drive approach can be found in Autodesk data model APIs implementations. Check the article about Manufacturing Data Model APIdemonstrating how data can be extracted directly via cloud service without the need to work with files.
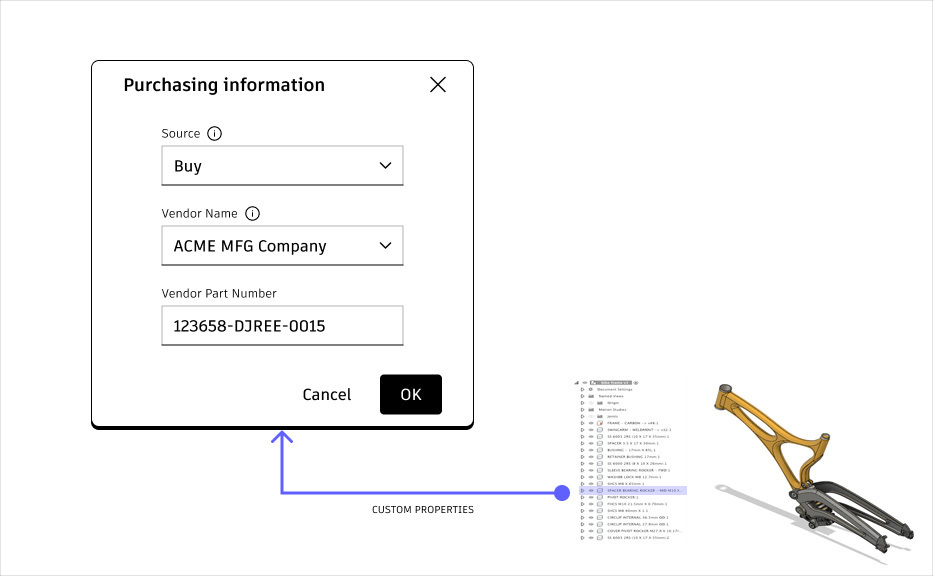
Implementing the Transition
An important question is how to move from a document management world into a data-centric world. A large number of design is still done using document-driven approach and CAD/PDM bundles are one of the most popular and mature combination used by many systems.
The way to make it is to establish a product data model that is capable to capture information from multiple design silos into a single product data model. Check my earlier article about how to build a digital thread model and use it to consolidate multiple elements of product data. Another article – Do we need a product model for digital thread explains how a product model can become a place for traceability. In our case with moving from PDM document management software to PLM, you will need to establish a product model to represent multiple data silos.
An important steps in the implementations:
- Assessing Current Data Practices: Check current CAD/PDM systems, identifying data silos, evaluating the effectiveness of existing PDM systems, and pinpointing areas for improvement. The key element here is to figure out how to capture data from multiple design silos.
- Developing a Product Data Model Framework: How to put the data in the center. You need to establish a way to manage data, establish policies to data updates and lifecycle changes. The key element is to establish data quality, access, and security of the data across the organization. It is data foundation of the organization. Now, everyone is getting data from here instead of relying on old fashion “released documents”.
- Investing in Technology, Training and Change Management: Equipping employees with the necessary skills and fostering a culture that embraces change are critical components of a successful transition. A traditional technology is good for document management software, but it doesn’t fit well modern data-centric paradigm and creating of data central repository to serve product lifecycle management holistically across all design and engineering data and multiple disciplines.
Benefits of Moving from Documents to Data
What are benefits of moving to data centric approach. I put below important benefits for any organization moving to data centric approach.
Enhanced Collaboration and Integration: Data-centric models promote a unified view of product information, breaking down silos between departments. This interconnectedness supports better collaboration and allows for more integrated workflows, enhancing the overall efficiency of product development processes.
Improved Data Quality and Consistency: With a single source of truth for product data, organizations can significantly reduce errors and inconsistencies. This leads to better product quality, faster time-to-market, and lower costs associated with rework and delays.
Agility and Flexibility: Data-centric models provide the agility needed to adapt to changing market demands and technology advancements. Organizations can more easily modify product information, integrate new tools and processes, and respond to customer feedback.
Facilitating Digital Transformation: Transitioning to a data-centric model is a crucial step in digital transformation. It enables the adoption of advanced technologies such as artificial intelligence (AI), machine learning, and the Internet of Things (IoT), which require access to reliable, structured data to provide insights and drive innovation.
What is my conclusion?
Document driven approach in CAD design and product development is limiting organizations. A complex product design, complexity data relationships and release processes are killing organizations and leaving them to work in a very inefficient way.
However, moving from traditional PDM to holistic data management approach is not a simple tasks. It is a journey that demands vision, commitment, and strategic planning. However, the benefits of making this shift are profound, offering organizations the ability to innovate faster, improve product quality, and compete more effectively in the digital age. As we move forward, the transition from documents to data will not just be an option but a necessity for those looking to thrive in the evolving landscape of product development and management.
Just my thoughts…
Best, Oleg
Disclaimer: I’m co-founder and CEO of OpenBOM developing a digital-thread platform with cloud-native PDM & PLM capabilities to manage product data lifecycle and connect manufacturers, construction companies, and their supply chain networks. My opinion can be unintentionally biased.