
Combining multiple systems in manufacturing sector to work together is always a complex thing to do. In the engineering and manufacturing world, PLM and ERP software integrations is a greatest example of complexity. Combining complex business processes and engineering disciplines including mechanical engineering, electrical engineering, electronic design, software and applying them to complexity of business management software system multiplied by complexity of supply chain management. In my my article today, I’d like to discuss how modern computer engineering disciplines such as an advanced data management and graph models can help here.
The Growing Complexity of Engineering and Manufacturing Processes
In today’s dynamic business landscape, the complexity of engineering and manufacturing processes continues to escalate. Products are no longer simple assemblies of mechanical parts but rather intricate combinations of mechanical, electronic, and software components. Moreover, consumer demands for customization have led to a wider needs to use product variants and configurations. To compound matters, supply chains and manufacturing operations have become increasingly distributed across the globe, necessitating adaptability to the realities of modern disruptions and constraints such as geopolitical instability and supply chain bottlenecks. In this context, the integration of Product Lifecycle Management (PLM) and Enterprise Resource Planning (ERP) systems emerges as a critical challenge, as it requires the seamless organization, management, and distribution of data across multiple systems.
Here is an example of digital thread and complexity of system landscape explained in one of the works by Prof. Martin Eigner.
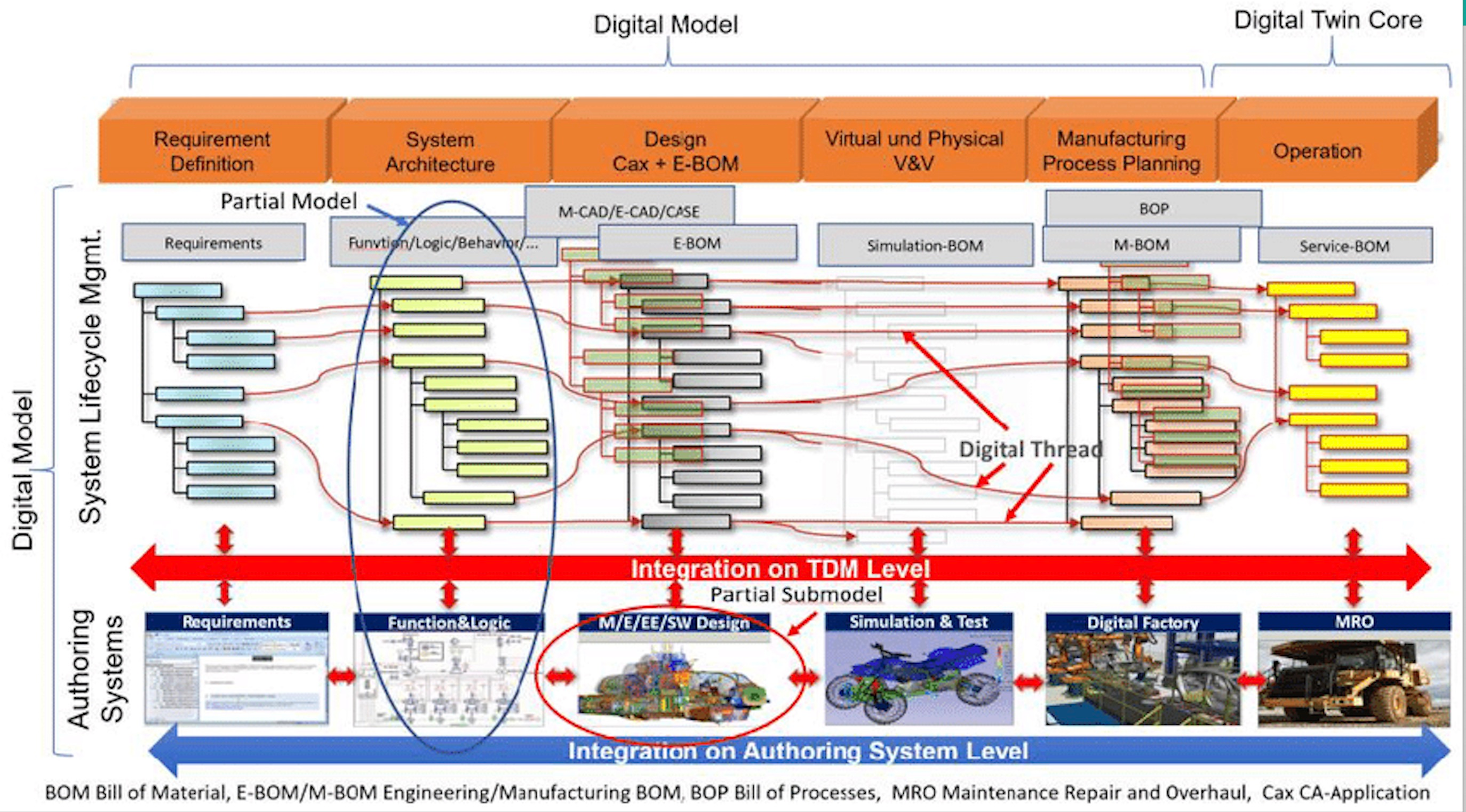
Integration Complexity of PLM-ERP
Traditional approaches to PLM-ERP integration often fall short in addressing the multifaceted challenges posed by modern product development and manufacturing environments. The complexity transcends simplistic data mappings; for instance, a single part may have varying definitions based on factors such as manufacturing location, supply chain options, and regulatory requirements.
The complexity of integration between these systems is skyrocketing and it cannot be done by a simple mapping of data, exporting spreadsheets and transferring information using spreadsheets and simple batches. We need to acknowledge that data is more complex that mapping part A in PLM to part B in ERP and vice versa. There is a process where the same part A can be defined as part B, C, and D dependent on manufacturing location, supply chain option and other condition.
Prof. Dr. Jorg Fischer’s work has shed light on innovative integration paradigms such as Object Type Cascade and Generic Structure Embedding offering models of data organization between PLM and ERP systems (he calls it “ERP near PLM”), which recognizes complexity data integration between multiple systems. Check the link above. Here are examples:
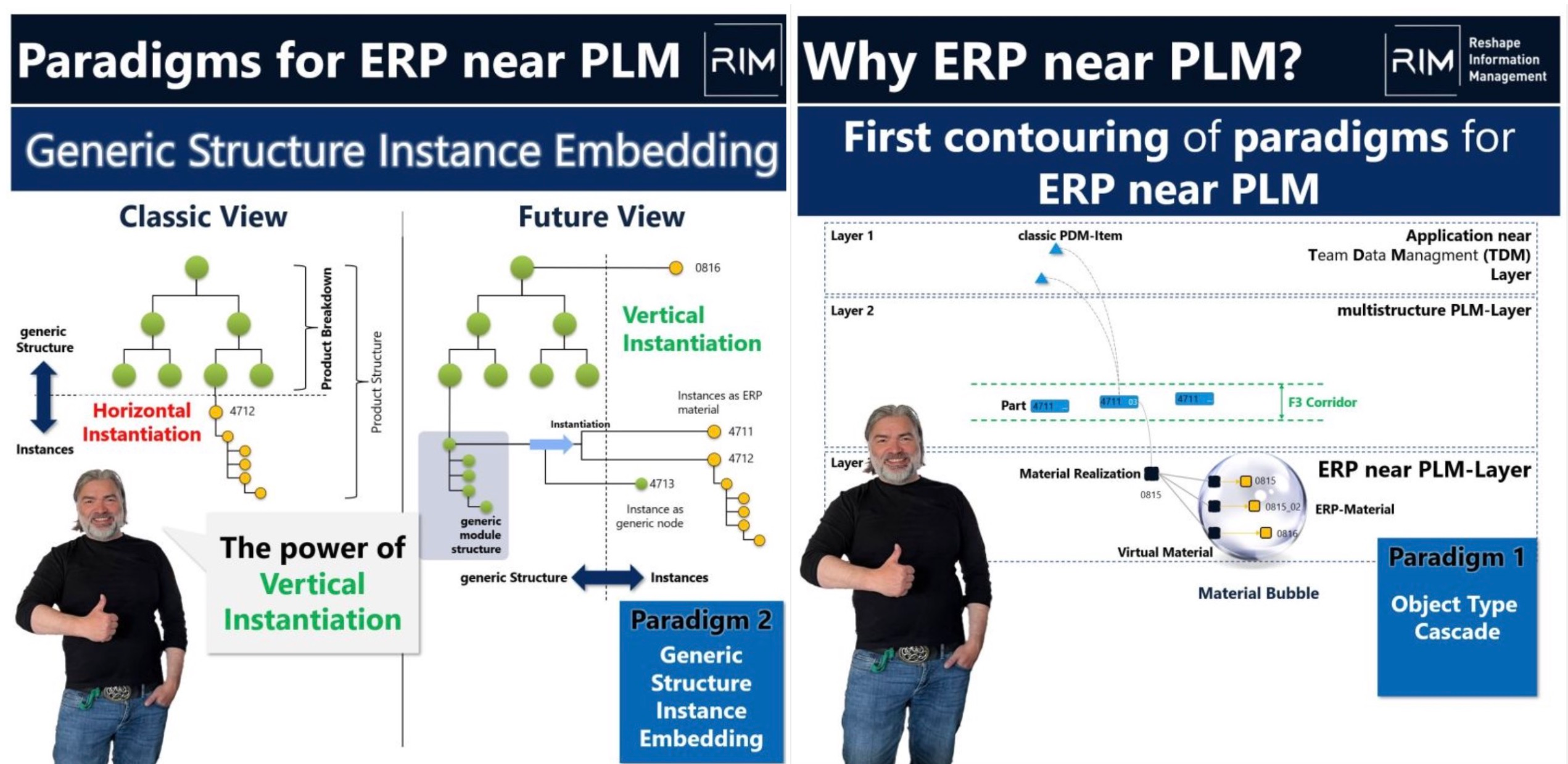
These paradigms underscore the need for advanced technologies that recognize the nuanced interdependencies of manufacturing process, specific of mass production and custom product development, manufacturing techniques, and how it reflects the integration between data entities within PLM and ERP systems.
The conclusion I want to suggest about the complexity of integration can be summarized as the following 3 points:
- Data is extremely complex in both systems;
- There multiple conditions describing dependencies (not a simple 1:1 map and
- Information flow to support the process is part of the conditions (eg. a specific product configuration, manufacturing location, a specific supplier).
Evolution of PLM-ERP Integration
Over the past two decades, the landscape of PLM-ERP integration has evolved significantly. Various techniques have been developed, ranging from rudimentary export/import methods to advanced middleware solutions.
PLM-ERP integrations techniques were developed by multiple PLM, ERP and other vendors for the last 20+ years and provided many sophisticated tools to transfer and map data. You can see multiple examples and integration attempts such as simple export/import (can work sometimes) to integration middleware software and even company agreements to create out of the box integration between two products such as Teamcenter and SAP.
However, the advent of digital thread solutions represents a paradigm shift in integration strategies. Digital thread solutions enable a connected data model approach, where information flows seamlessly between PLM and ERP systems, transcending traditional batch processes. This evolution marks a departure from the siloed approach to data management, towards a more holistic and interconnected ecosystem.
Digital Thread and Advanced Integration Data Models
Digital thread solutions offer several advantages in simplifying PLM-ERP integration. By adopting modern product models and digital thread architectures, organizations can streamline data organization and enhance connectivity between disparate enterprise systems and disciplines (eg. mechanical engineering, electrical engineering, software and computer engineering) . These models facilitate the management of rules and conditions, enabling seamless information exchange across the product lifecycle. Moreover, digital thread solutions promote agility and adaptability, allowing organizations to respond swiftly to changing market demands and regulatory requirements. The examples of such complex digital thread implementations are coming from many industries – automotive, defense, oil and gas industry, and even civil engineering that actively moving towards industrial principles in construction.
The development of digital thread solutions brings a new approach into PLM ERP integrations. Now it is not recognized as a “batch” integration anymore. We should look on a connected data model helping to create a data model and a process that setup information and supports information flow between different silos of data (ERP and PLM) as well as capable to manage complex rules and conditions. When the problem is defined in a such a way, I’d suggest to check what is the best tools to make it happen?
The candidates to these roles can be each of the systems (PLM, ERP), but also can be other integration platforms. Regardless on what system is used, I’d like to focus on some specifics of data organization and data model. In my earlier articles, I was talking about advantages of modern product models and digital thread. Check two articles – Simplifying PLM and Digital Threads using Web of Data and Connected Services and 3 benefits of using graph based digital thread product models for PLM-ERP integrations By providing rich graph based model, PLM systems can support complex data structures for integration. What is important here is flexibility in data organization and building relationships between two systems.
Graph Model-Based PLM-ERP Integration
Graph-based models emerge as a promising solution for addressing the complexities of PLM-ERP integration. Unlike traditional data models, which rely on rigid hierarchies and structures, graph models offer a more flexible and scalable approach. By representing data entities as nodes and their relationships as edges, graph models enable the creation of dynamic and interconnected data structures. This flexibility is particularly beneficial in managing complex dependencies and configurations within PLM and ERP systems.

Graph Model based PLM-ERP integration. I believe graph based models provide much more robust and flexible way to organize data that can withstand complex integration requirements and data model customization required by different companies. This is where OOTB approaches rarely work (which is again the reason why all PLM-ERP integrations are so complex).
Graph models and graph databases (eg. Neo4j) were taking on some of a very complex data management solutions, also related to Bill of Materials. Check the following story from Neo4j and US Army:
Most enterprise manufacturers use vendor applications: CRM systems, work management systems, accounts payable, accounts receivable, point of sales systems, and so on. Due to this approach, you need to store and model data as a graph where a native graph stores interconnected master data that’s neither purely linear or hierarchical. Likewise, emerging BOM trends add even more layers of data challenges. Compliance requirements are more strict. Counterfeit parts are pervading the market. There’s consolidation among parts manufacturers, and parts life cycles are becoming shorter. Meanwhile, tech innovation has shown to increase risk of availability while simultaneously contributing to obsolescence. A graph database flexible data model makes it easy to evolve master data as needs change over time.
In my earlier article –The importance of graphs for future PLM platforms, I was talking about usage of graph data models to collect and connect interdisciplinary data from multiple systems.
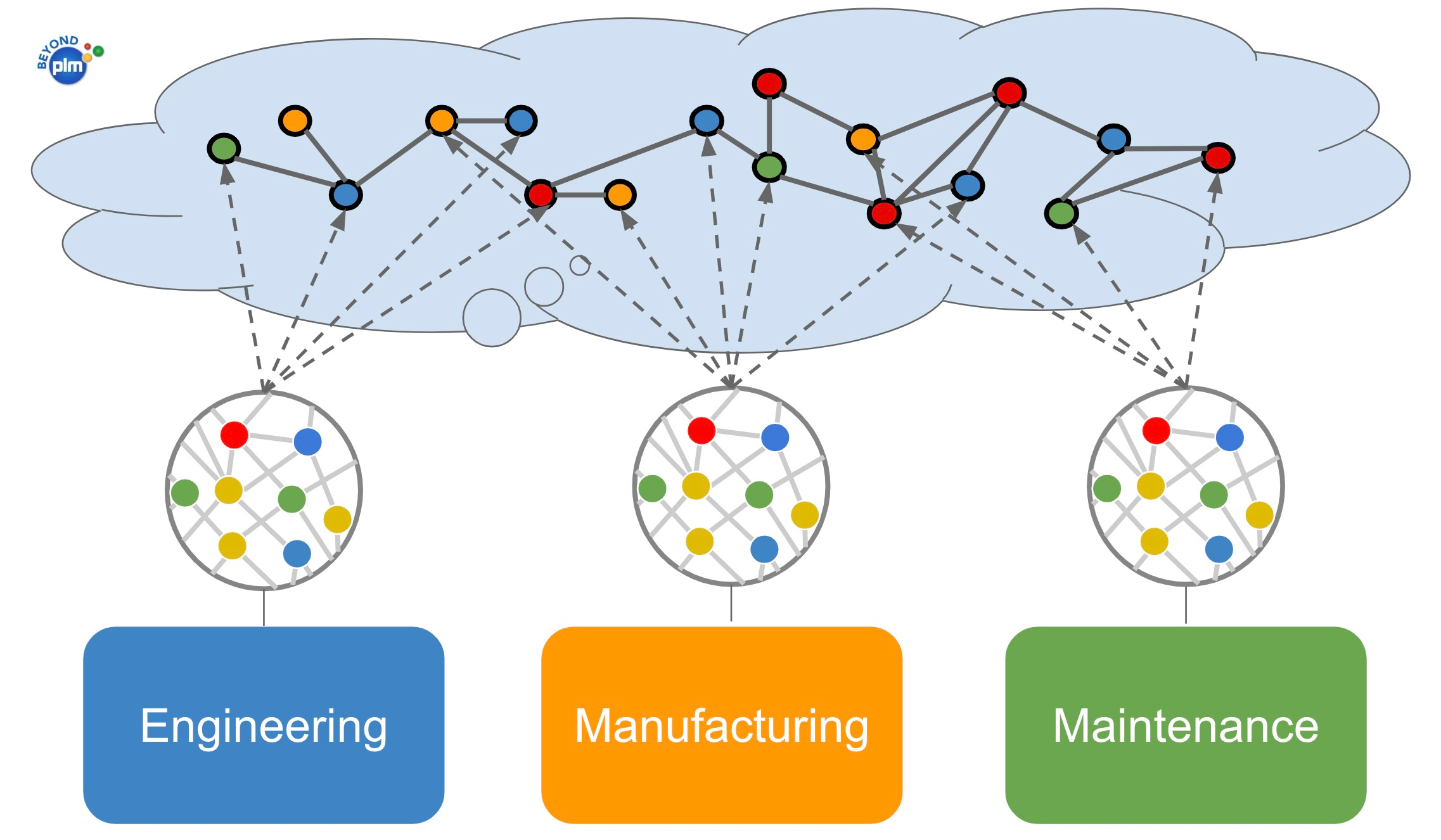
An example of graph organization to integrate PLM and ERP can be creation of multi-view product structure with different BOM type relationship and flexible relationships describing additional conditions and dependencies. In such a way, a “Generic Structure” relationships can be combined with “EBOM” relationships to represent ERP near PLM layer described by Prof. Dr. Jorg Fischer. I will come to more specific examples of how it can work in my articles later.
What Is My Conclusion?
As businesses navigate the complexities of modern product development and manufacturing, the integration of PLM and ERP systems remains a critical element of successful implementation. Complexity of integrations between multiple systems and digital thread implementation brings the need for robust and flexible data modeling to support these data and processes.
Existing PLM and ERP often coming from decades of data modeling histories and using old and not flexible enough data modeling tech. New data management capabilities and especially introducing of graph based data models for development of modern PLM can offer a new ways to organize and support digital thread.
The emergence of digital thread solutions and graph-based models offers new opportunities to overcome integration challenges and unlock operational efficiencies. By embracing innovative data management capabilities and adopting agile integration strategies, organizations can establish a robust foundation for success in today’s rapidly evolving landscape.
Just my thoughts…
Best, Oleg
Disclaimer: I’m co-founder and CEO of OpenBOM developing a digital-thread platform with cloud-native PDM & PLM capabilities to manage product data lifecycle and connect manufacturers, construction companies, and their supply chain networks. My opinion can be unintentionally biased.