I’m continuing the discussion about Digital Thread Evolution. In the first article, I introduced you to the purpose of digital thread and shared my take on the four phases of digital thread development. Check this out here – Digital Thread Evolution Part 1.
This is my Part 2 article and I want to talk about the current state of digital thread development and the historical status quo of information management in industrial companies. In my digital thread evolution map, it is the first level (on the left).
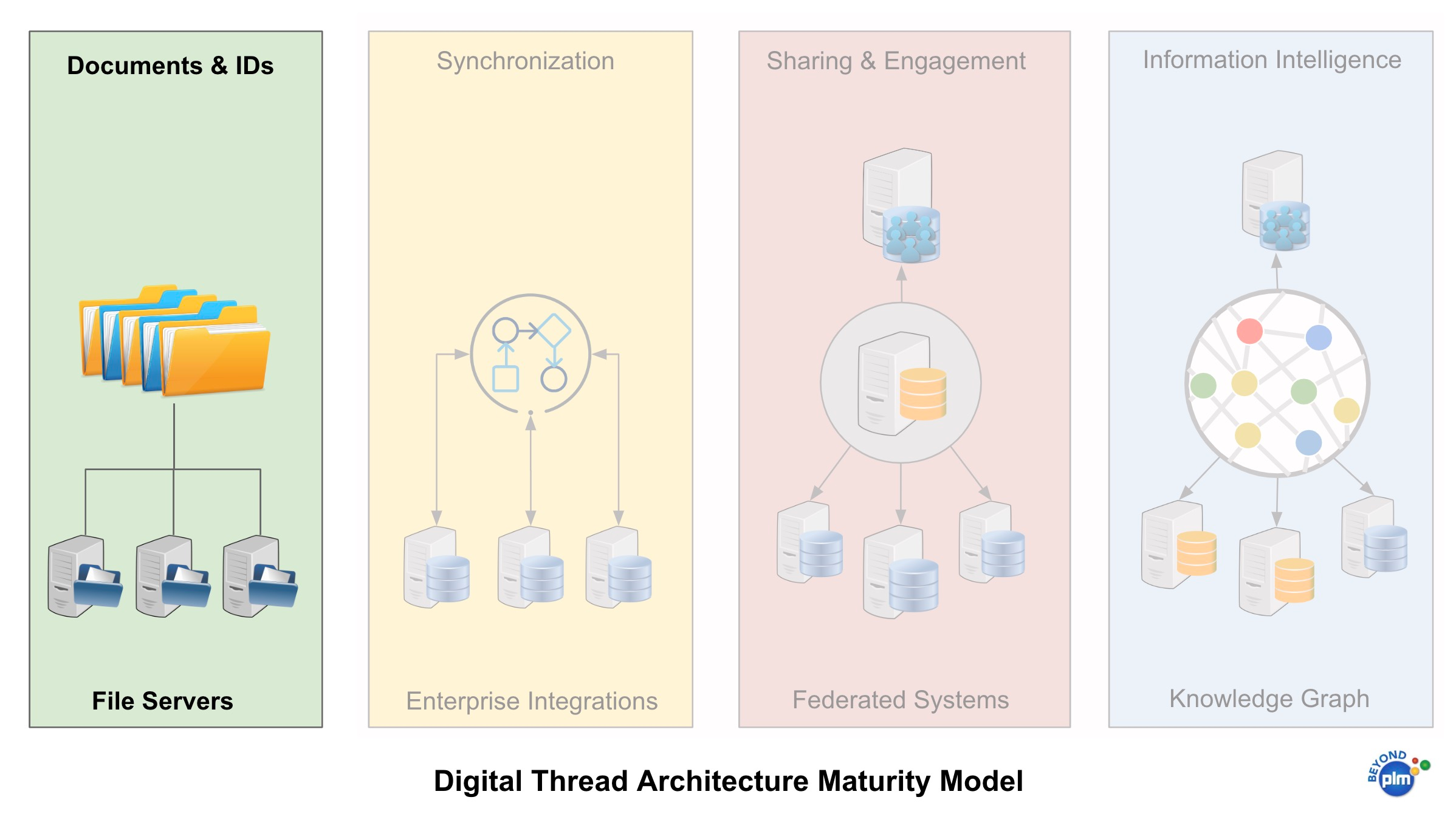
Data Management Status Quo
The foundation of engineering and manufacturing software went back to two data sources – (1) design and (2) manufacturing planning. After the first “digitization” effort of design, data was moved from paper to CAD files, which were stored everywhere and managed in different formats – native 2D and 3D and also many derivative formats. PDF is one of the most prominent formats used in product lifecycle management (PLM) even today as a medium to keep released information (also used a lot in supply chain management).
Manufacturing planning was all about the management of BOM (sometimes called a “single BOM” or “single repository” of item master data and BOMs). Here is a good place to learn about it -5 Books to Start You Bill of Materials Education. These BOMs later became a foundation of MRM (manufacturing resource planning) and MRPII software. The amount of databases, homegrown MRP systems, legacy databases, and just ‘smart’ spreadsheet systems in production planning is huge, but all of them are siloed and not very well (or at all) connected to the rest of the product information.
Another growing source of information is MRO (simply maintenance and service) includes data about existing products sold and maintained by manufacturing companies. The number and demand for this information are growing, but at this point, they live in their own siloed world. I will talk about it later.
The status quo of product information is presented by a large number of different files and legacy databases and data management systems. Local area networks (LAN) and recently cloud file storage is a place where DIY product lifecycle management (PLM) and digital thread begins.
Intelligent Part Number and Digital Thread Foundation
A large amount of files and databases brings the question of how to connect and link this information together. How can I find what is in a specific 3D CAD or PDF drawing file, how is it related to a specific product that was manufactured last month, and what product revision we requested from CM (a contract manufacturer) last week? Those are very painful data management problems. The way industry is solving it is by organizing a system of Part Numbers that represents a sophisticated reference base to answer a single question – what is included in a specific assembly? What is in the file? How to find an Excel (record) about the BOM, file, PO, etc?
My observation is that the Part Numbering system in every company combined with the file management system represents the most frequently used now digital thread foundation. Even if a company is using computer-aided design (CAD), product data management (PDM), product lifecycle management (PLM), enterprise resource planning (ERP), supply chain management (SCM), and other systems to manage the product development process, files and “smart” part numbers are used as a foundation of a PLM system, product lifecycle, and digital thread. These systems of files and corresponding smart part numbers are often used as the most reliable way to get up-to-date information when it is needed for process management in a company.
How to scale up beyond documents
As businesses grow, so does the complexity of product lifecycle and the complexity of work-related, companies are looking for better PLM solutions capable to scale product lifecycle management beyond the level of “document” and smart part numbers.
To help manufacturers scale up beyond document-based processes and maximize efficiency while maintaining compliance across all operations, the question of how to organize a digital thread in a better way is the one that becomes very urgent. The businesses are struggling to manage their processes using current legacy systems. Global manufacturing business processes, distributed teams, new regulations, the complexity of supply chain, new business models, introduction of new services and connected products – all these things together are bringing the need to have a better way to manage a digital thread and use it as a source of intelligence for decision making.
To make it happen, companies need to step up and scale beyond the current “document” based digital thread. It requires new data management technologies and new PLM platforms to make it happen. The first step in this journey is to stop thinking about documents and start thinking about “granular data”.
What is my conclusion?
The digital thread status quo is represented by documents (files) and a system of “smart” part numbers helping manufacturing companies to navigate through the large number of information generated during product development processes, manufacturing, and the entire product lifecycle. A current digital thread is not sustainable and leads to mistakes in design, and production planning, missed customer feedback, lost information in document management system systems, delayed production, increased cost, and many other challenges that can be eliminated by bringing a new and modern PLM software with new capabilities. The process is not simple and requires gradual migration in all aspects of product lifecycle management – technology, people, processes, and market conditions. Just my thoughts…
PS. What comes next? Wait for my Digital Thread Evolution – Part 3.
Best, Oleg
Disclaimer: I’m co-founder and CEO of OpenBOM developing a digital cloud-native PDM & PLM platform that manages product data and connects manufacturers, construction companies, and their supply chain networks. My opinion can be unintentionally biased.