
In the fast-paced world of manufacturing business, staying ahead of the competition requires efficient management of product development, manufacturing, and supply chain processes. While it sounds like an obvious thing to do, for many manufacturing companies I meet and talk to, it represents a dilemma that sounds simple – where we should start.
Manufacturing businesses manage product lifecycle regardless of what software systems are in place. You can manage design sketches on paper and create a Word file with the list of components to buy and manage orders using Excel and Amazon. In that case, it would be your very inefficient PLM+ERP solutions.
Every company starts from the place where their team has the most experience. Everyone brings the experience of how they solved the problems before combined together with their field of responsibilities – design, production planning, procurement, and finance. For someone, it can be first to set up a system to manage CAD files or to ensure a modern cloud CAD design software system is in place. For some other businesses, production planning combined with financial systems will be the key component.
Traditionally, large organizations have relied on separate systems to handle product lifecycle management (PLM) and enterprise resource planning (ERP). However, in the modern realities of manufacturing this old dilemma is being transformed by the emergence of modern Software as a Service (SaaS) applications.
Digital transformation brings changes to both small and large manufacturing organizations, asking questions about how to organize integrated information flows and to streamline processes that before were siloed in large organizations and in peoples’ heads. New agile product development methods offer a comprehensive solution that addresses the limitations of the past, bringing about a new era of streamlined operations and enhanced productivity.
Old PLM vs ERP Challenges and Modern Manufacturing Businesses
In the past, PLM and ERP systems were distinct and often incompatible entities. PLM systems focused on product design, engineering, and collaboration, enabling organizations to manage the entire lifecycle of a product from concept to retirement. On the other hand, ERP systems provided centralized management of various business processes, such as finance, procurement, inventory, and sometimes customer relationship management (CRM) and Manufacturing Execution System (MES). This division often resulted in information silos, duplicated efforts, and fragmented communication, leading to inefficiencies and bottlenecks. This is the reality for many large industrial companies I’m familiar with.
Manufacturing technologies and processes changed dramatically over the last decade enabling a huge wave of manufacturing innovation. You can start your manufacturing business literally out of your basement by hiring engineers, design contractors, and contract manufacturing companies. Distribution channels are also transforming. For many growing companies, it allows them to build the strategy of scaling their businesses, bringing capital, scaling up production efforts, and selling products using a modern omnichannel strategy.
For many of these companies, the question of how to support product lifecycle management in this modern digital environment is remaining supercritical. While most businesses are coming with their traditional experience, the question “Should I buy ERP” or “Should I buy PDM/PLM software” to solve the problems comes very quickly. But the decision is not simply because old siloed methods don’t work well in modern connected manufacturing environments.
Agile Product Development and Integrated SaaS Services
I wrote an article last year – How to move beyond debates about what comes first PLM or ERP, I shared my thoughts about how companies can start thinking about business functions and not software system boundaries. It is more important to understand what you need to do, how to organize the process, and how one or another system can help you.
Modern software examples help you to understand how you can organize your work by allowing people to work in parallel and also to integrate fast using integrated software and seamless information flow. Check Onshape Introduction to Agile Product Design. The industry numbers speak for themselves:

Onshape article shows you how to save time by allowing to people to work in parallel. Check – How Can Agile Product Design benefit you?

Here is a good example coming from a recent LiveWorx 2023 conference. The following picture shows you the benefits of agile work.

Autodesk Fusion360 article speaks about how companies can improve their TTM (Time to Market) by applying agile product development principles. Here is my favorite outline.
- Establish real-time communication with your supply chain partners.
- Gain greater visibility into part shortages and other issues that impact production.
- Shorten your engineering change order (ECO) cycles through automated reviews and approvals.
- Aggregate bills of materials (BOMs), quality documents, design files, and other essential records into a single source of truth.
The following OpenBOM article – OpenBOM Basics: Agile Product Development, Inventory, and Purchasing gives you an idea of how integrated SaaS products can accelerate and transform the processes moving from old fashion waterfall processes to the modern agile new product development process (ANPD)

PLM+ERP+MES: The Rise of SaaS Applications
Modern SaaS applications have revolutionized the way businesses manage their operations. By offering integrated solutions with functions breaking traditional PLM, ERP, and MES boundaries and simplification of integration of PLM, ERP, and MES SaaS services, these applications offer a unified approach to product development and business management. Organizations can now benefit from seamless collaboration, real-time visibility into processes, and a holistic view of their entire operations.
Benefits of Integrated SaaS Applications:
- Improved Collaboration: Integrated SaaS applications enable cross-functional teams to collaborate effectively. Departments like design, engineering, manufacturing, and supply chain can work in sync, eliminating communication gaps and reducing errors. This leads to faster decision-making and increased innovation.
- Streamlined Workflows: With integrated systems, organizations can streamline their workflows and eliminate redundant processes. Data flows seamlessly from design to production, procurement to inventory management, and sales to customer service. This ensures accuracy, reduces lead times, and optimizes resource allocation.
- Real-Time Visibility: SaaS applications provide real-time insights and analytics, empowering organizations to make data-driven decisions. By having access to a centralized database, managers can monitor project statuses, track key performance indicators (KPIs), and identify bottlenecks promptly. This visibility enhances operational efficiency and enables proactive problem-solving.
- Scalability and Flexibility: SaaS applications offer the advantage of scalability and flexibility. As businesses grow, they can easily adapt and expand their operations without worrying about infrastructure limitations. Organizations can add or remove functionalities as per their evolving requirements, allowing them to stay agile in a competitive marketplace.
- Cost Savings: Adopting SaaS applications eliminates the need for on-premises infrastructure and maintenance. Organizations can save on hardware costs, software licensing fees, and IT resources required to manage separate PLM and ERP systems. Moreover, SaaS applications typically operate on a subscription-based model, providing cost predictability and affordability.
Future: Breaking Boundaries and Integrating Data
We’re moving into Data-Driven Business where data will become much more important than application boundaries. The traditional PLM vs ERP dilemma is gradually becoming obsolete as more organizations recognize the value of data and integrated SaaS applications. The future of product development and business management lies in these unified platforms, where seamless collaboration, real-time visibility, and enhanced productivity are the new norm. As technology advances, we can expect further innovation in areas like artificial intelligence, machine learning, and predictive analytics, providing organizations with even more powerful tools to optimize their operations.
Check my earlier article – Integrated PLM Platforms and Multi-Cloud Web Services. I shared my thoughts on how multiple applications coming from different vendors will allow supporting integrated processes to support digital processes.
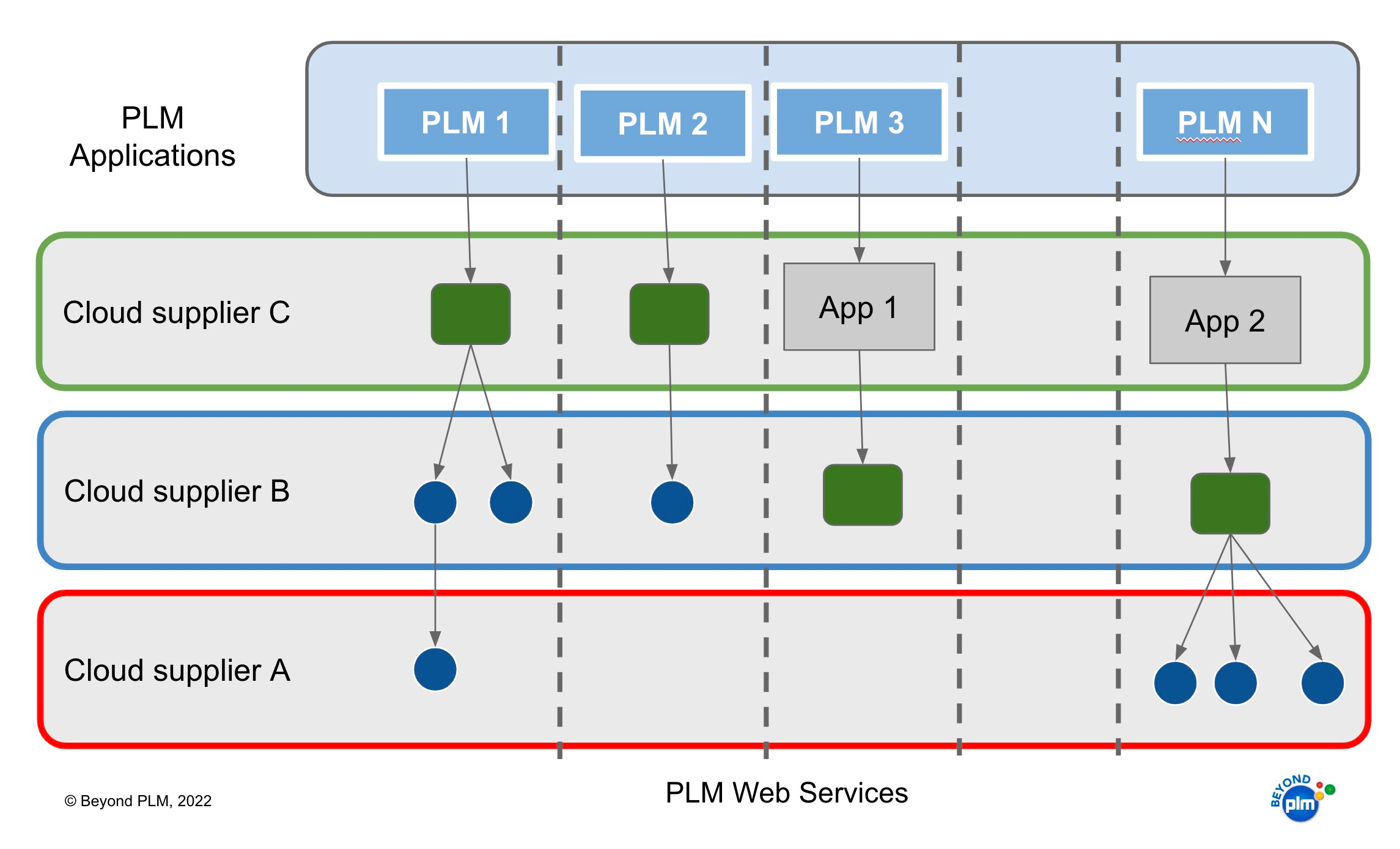
What is my conclusion?
The old PLM vs ERP dilemma has found its resolution in modern SaaS applications and digital transformation trends. Companies of any size should start by thinking about their processes and data and then need to manage to support them. It brings new product lifecycle management, product data management, and supply chain management thinking. Product data management is moving from CAD file management to integrated product development processes, digital product lifecycle replaces old fashion emails and Excel file exchanges. You can start from a few SaaS services to support design, engineering BOM and procurement and grow into multi-cloud services provided by multiple vendors. Integrated platforms offer a holistic solution that combines product lifecycle management and enterprise resource planning functionalities. By breaking down information silos and enabling seamless collaboration, organizations can achieve streamlined workflows, real-time visibility, and enhanced productivity. Standard REST API integrations and seamless data flow combined with flexible data management capabilities are key differentiators of the platforms that will come to replace old and rigid PLM and ERP dinosaurs. Just my thoughts…
Best, Oleg
Disclaimer: I’m co-founder and CEO of OpenBOM developing a digital thread platform including PDM/PLM and ERP capabilities that manages product data and connects manufacturers, construction companies, and their supply chain networks. My opinion can be unintentionally biased.