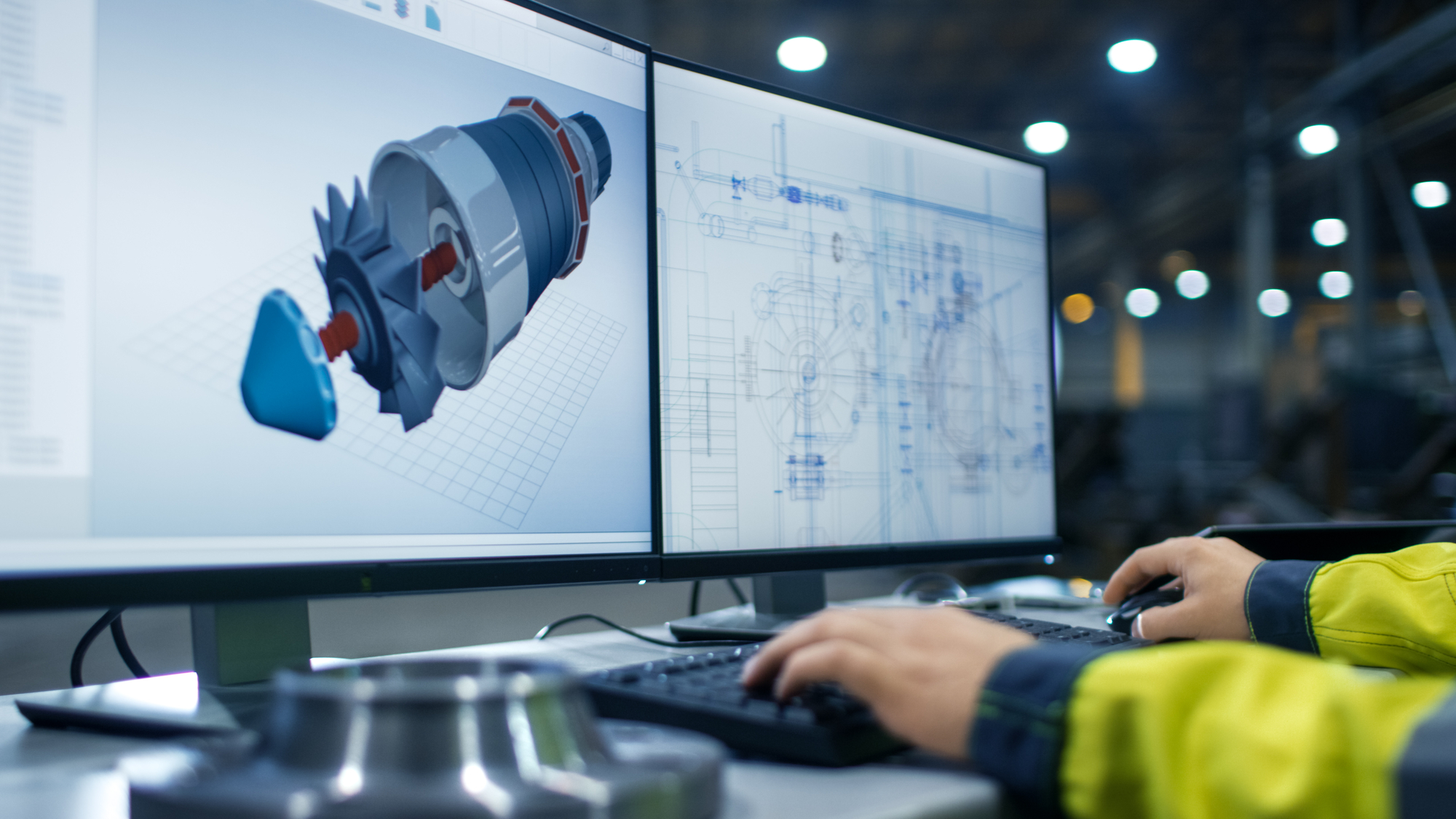
In product design, managing complexity is a persistent challenge that organizations face every day. Whether we’re looking at mechanical design, electronics, or software, the complex and interconnected nature of these disciplines often leads to vast silos of information, which are typically managed and stored as files in product data management (PDM) systems.
Modern product lifecycle management (PLM) is focusing on digital twins and digital thread is very often missing design data management functions considering this phase of PLM development is done. However, the problem of CAD data access by internal and external users is still very critical for engineering processes. Revision control and access to the entire history of design data is not simple, quality assurance teams are not well connected to design data, and the product development process often relies on multiple CAD files delivered via email or internal network, or cloud hosting. Overall, it represents a big problem to establish digital business processes and to support global teams.
Historical Perspective of PDM Development
For the last 20 years, the product data management (PDM) software business passed multiple development stages. It started as an important addition to CAD packages solving a painful problem. The availability of product-related data represents a big problem. After a bit more than a decade of successful PDM business, CAD vendors murdered product data management PDM software, acquired leaders and made each of their CAD packages come with a dedicated PDM system (eg. Solidworks/Enterprise PDM, Autodesk Inventor /Vault, CATIA ENOVIA, NX/Teamcenter, Creo/Windchilletc.) While 3rd party CAD integrations are possible, there is always a question about their longevity alongside “mothership PDM functions”. The last decade of cloud innovation which has started with the introduction of GrabCAD Workbench (RIP), Autodesk Fusion 360, and Onshape, started a new wave of PDM software – cloud-based and embedded into CAD systems. Read some of my previous articles about it.
How CAD Vendors Murdered PDM Business
You might think that PDM “story” is done. Old systems will die, and new cloud CAD services are coming with the inclusion of PDM features. Leading vendors are offering hosted PDM/PLM software to support their existing file-based CAD systems.
While what I said above is true, the PDM problem is not gone. It is transforming. Here are a few interesting trends that I can see happening with customers.
- The majority of CAD systems in production are still file-based. While the PDM problem is most probably solved by CAD vendors for large customers, SMB/SME companies are desperately looking for free/affordable PDM options (the recent event of GrabCAD discontinuation demonstrated the number of companies looking for free PDM)
- Existing PDM systems are capable to manage CAD files, but are very limited in their capabilities to become a hub for design information. In most of cases, customers are following best practices of transforming CAD files to neutral geometry (STEP, PDF, etc) and using file-based cloud services or emails to distribute it downstream.
- Existing PDM licensing models are focusing on selling expensive licenses to engineers and don’t provide much to the rest of the organization (especially it is true for old PDM software that requires a VPN to connect outside of LAN).
- Product complexity leads to situations where multiple CAD and PDM software must be used (eg. mechanical, electrical, PCB, etc). Existing PDM systems are not well prepared to handle these scenarios. Even more, modern cloud CAD systems are following a more siloed approach and focusing on absorbing design functions under a single CAD roof (eg. Fusion360 and PTC Onshape added PCB design to their MCAD packages).
In my view, the current status quo is that customers still massively rely on files (mostly CAD-neutral formats) to deliver information downstream and also to exchange data in complex engineering design processes. This status quo is a big element of inefficiency and a source of mistakes. Moreover, it is a significant problem for companies’ future digital transformation plans and the establishment of connected information flow and closed loop of information between multiple organizations (engineering, manufacturing, sales, maintenance).
A future challenge for the industry is to support the rapid evolution of digital technologies which will shape new trajectories in downstream design integrations, steering us beyond the strictly file-based approaches of the past. How it can happen? Let’s talk about it.
The Challenges of File-Based PDM Integration Approaches
Traditional file-based PDM systems, although widely used, present various limitations. In the face of intricate multi-disciplinary design data, file-based models often struggle to keep pace with the dynamic nature of product development, owing to their limited ability to handle complex relationships and dependencies across various design elements (mechanical, electronics, software). This is further compounded by the growing size and complexity of design data, which demands a more fluid, scalable, and interconnected data management approach.
Additionally, file-based PDM systems inherently promote siloed workflows. Each discipline — mechanical, electronics, software — tends to generate its data in isolation, and the resultant file-based approach restricts visibility and interactivity across domains. Such an approach lacks the agility to respond to the rapid changes in product design and fails to optimally leverage the multi-disciplinary data inherent in today’s design processes.
CAD in the Cloud: A New Source of Design Data
Computer-Aided Design (CAD) tools are increasingly moving to the cloud, which allows for more agile, collaborative, and scalable design processes. This shift is leading to a radical transformation in how we view design data. Rather than being tied to CAD files, design data is now managed by cloud CAD systems and stored in CAD databases. However, this data is still siloed. Think about a company using two cloud CAD systems services – PTC Onshape and Altium 365. These two systems are managing two independent cloud storages for design.
In this context, CAD tools become more than just a means to create design files; they become the source of design data. Cloud-based CAD systems provide a unified, interactive platform for design data, replacing isolated files with interconnected data structures that enable real-time collaboration, version control, and data management.
With the right level of API support and CAD vendor openness, the opportunity for a cloud-based CAD approach makes it easier to capture, share, and manipulate design data across multiple disciplines, facilitating seamless integrations and a more holistic view of product design. But this is still a dream for most of the scenarios. Customers are massively seeking how to export data from cloud CAD systems to neutral geometry files (STEP, PDF, DXF, etc). It is happening because of a lack of trust, prohibitive licensing, and requirements of 3rd party organizations (Eg. contract manufacturers)
Design Web Services: Tapping into Multi-Disciplinary Data
The proliferation of cloud CAD and cloud PDM digital technologies is also giving rise to design web services (REST APIs), that can harness multi-disciplinary design data. These web-based platforms can provide interfaces for integrating design tools and data across different disciplines, bridging the gaps that traditionally existed in file-based systems.
Through web APIs and standardized protocols, design web services enable real-time data exchange and collaboration, which can solve the problem of design data integrations. This approach can help to provide a digital umbrella above siloed desktop and cloud CAD systems that can focus on digital data continuity and information availability.
The Imperative of Downstream Design Data Availability
There’s an increasing recognition of the need to make multi-disciplinary design information available downstream for procurement and production planning, beyond the scope of engineering and design departments. Traditional file-based scenarios, with their lack of visibility and accessibility, are proving difficult to meet this requirement.
In this context, a service capable to fuse design information from files, cloud-based CAD systems, and other software can present a promising solution. By promoting data transparency and accessibility, these technologies can support the full lifecycle of products’ digital thread. It will enable more informed decision-making and also fosters a culture of continuous improvement and innovation.
What is my conclusion?
As we look toward the future of product design, I can see the approach to managing design data digitally available evolving. With CAD systems moving to the cloud and becoming a source of design data, and the growing prevalence of multi-disciplinary data, we’re seeing the emergence of design web services integrations that are better suited to handle the complexity of modern product design.
These developments underscore the urgent need to move beyond old-fashioned, file-based scenarios. By embracing these new trajectories in downstream design integrations, we can unlock the full potential of design data, creating more efficient, effective, and collaborative workflows that drive product innovation and deliver superior value.
Just my thoughts…
Best, Oleg
Disclaimer: I’m co-founder and CEO of OpenBOM developing a digital-thread platform with cloud-native PDM & PLM capabilities to manage product data lifecycle and connect manufacturers, construction companies, and their supply chain networks. My opinion can be unintentionally biased.