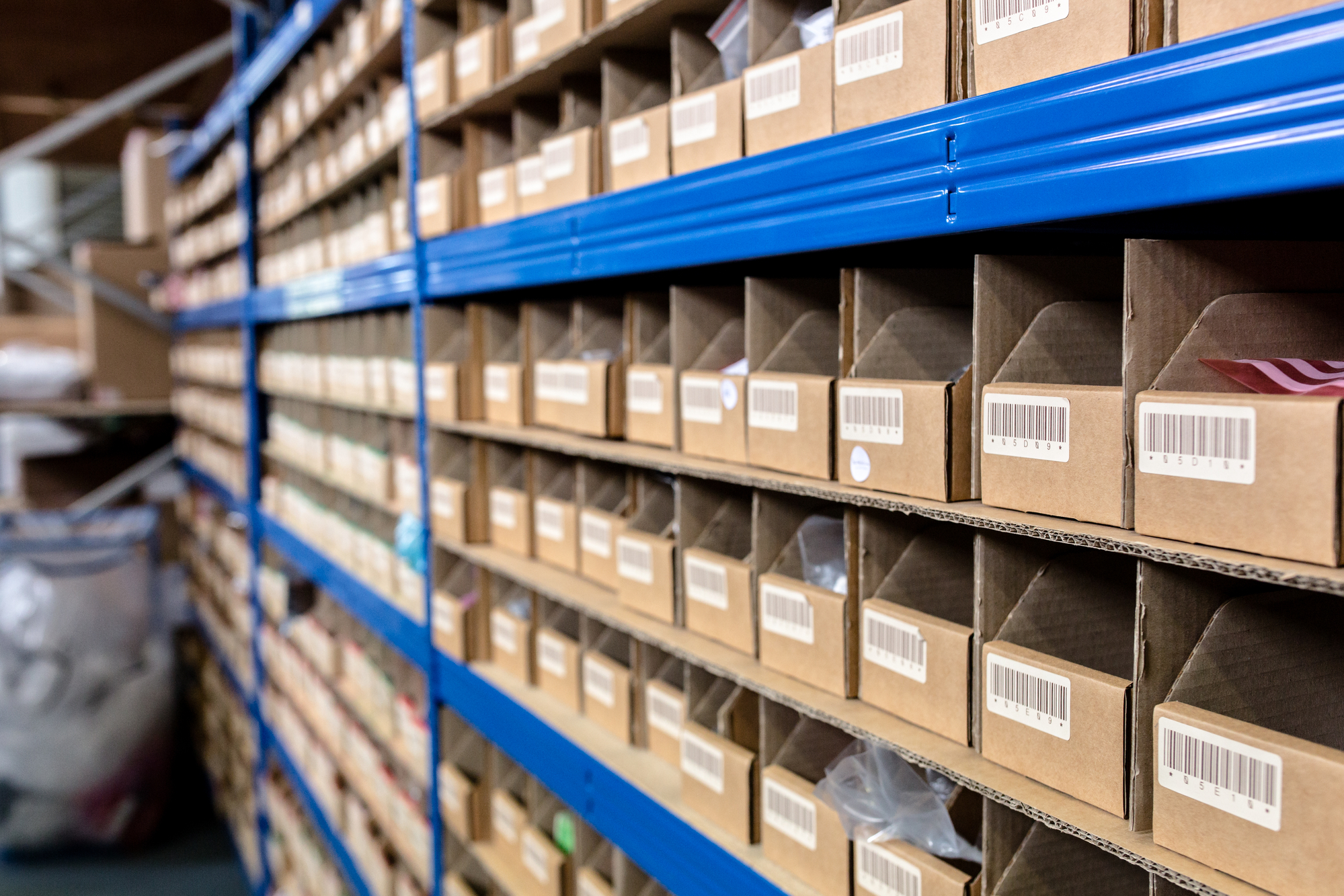
For years, manufacturing companies managed the division of two disciplines PLM and ERP in a very simplistic way – PLM for engineering, and ERP for manufacturing. The division represented the natural forces of two vendors. PLM’s roots were in CAD, design, and engineering, and ERP’s roots in MRP, and procurement planning. The line dividing PLM and material requirements planning (ERP) systems always triggered many discussions. It included endless debates about data integration between engineering BOMs and manufacturing, transferring data from CAD to ERP, finding all components required for production BOM, creating engineering bills of materials (EBOM), and others. For the last few years, the discussions about the role of MES and how the role of all three systems can be intertwined – PLM, ERP, and MES.
Bill of Materials is the lifeblood of all engineering and manufacturing processes. You need a variety of bill of materials representation to successfully design, manufacture and maintain products. Therefore, no surprise, the complexity of bill of materials management is the first thing that needs to be unwinded to find a way to reduce the complexity of modern product lifecycle management (PLM).
PLM simplification?
It was stated many times that engineering and manufacturing are complex disciplines and therefore you should not expect an easy path speaking about the manufacturing process, engineering BOM, manufacturing BOM, and bill of materials in general. The greatest and very sad (for me) conclusion was made by Jos Voskuil that PLM has become complex (or too complex to be understood by a single person).
While I understand the reasons for PLM complexity, I believe in the power of simplicity. There are many great reasons why simplicity always wins over complexity. My favorite is this one – Seven Reasons Why Simplicity Always Wins with my favorite passage:
The most complex it is, the slower it will be. The simpler it is, the faster it can be executed. The more time you spend preparing, understanding, thinking, and second-guessing, the slower you’ll be and the less you’ll execute. Simplicity is the key to quick decisions, bold action, and instant adjustments.
The complexity is hard to remember and hard to understand. People don’t like complexity in any form – it is hard to remember, it is hard to operate, it is hard to explain to others.
Check some of my previous articles about PLM and complexity:
The hard things about simple PLM
How to make PLM simple, but not simpler
The last article answers many of the questions about how to simplify PLM and keep it relevant in the context of modern manufacturing complexity. You can check the following diagram from the unstoppable PLM playbook that explains how different solutions can scale based on the complexity of organizations and the processes they need to support.
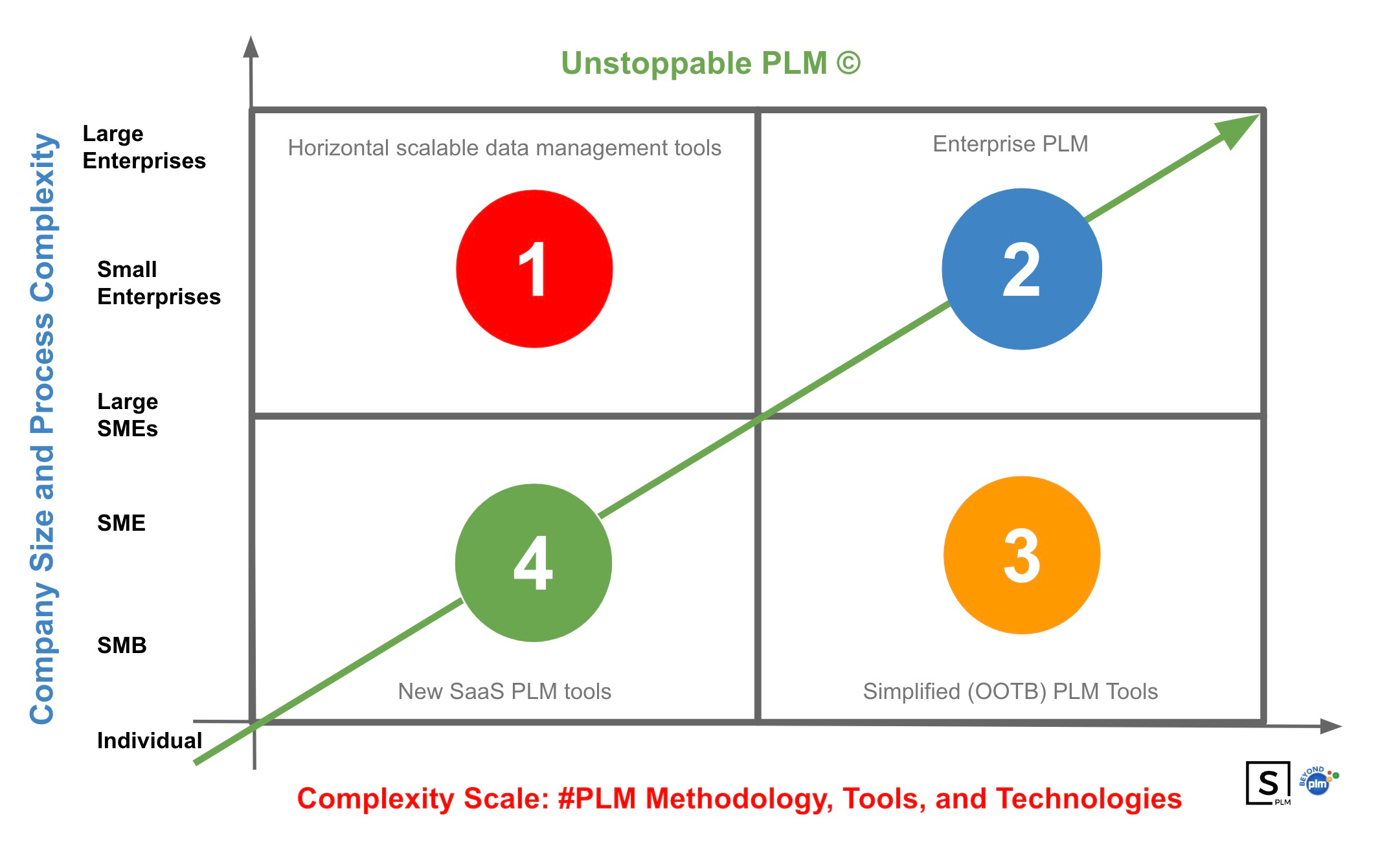
The Role of MBOM in the PLM Complexity Crossroad
The two most important processes needed to build products are engineering and manufacturing. In simple words, you need to get your design done, define everything you need to build a product from an engineering bill perspective, then pass the outcome to production and it is part of the manufacturing bill and everything that is needed for enterprise resource planning (MRP and procurement) perspective. As you can see the bill of materials and a lot of related data are heavily involved to make these processes happen.
This is a place where many companies are getting overwhelmed with the level of complexity that is needed to make this connection right, link engineering to manufacturing, connect the design and production process, translate raw materials, and pass an accurate BOM between multiple environments (PLM and ERP) and, finally sell a complete and shippable product to customers.
For the last few years, I can hear more and more debates about the role of MBOM in streamlining engineering and manufacturing processes. PLM vendors traditionally stayed away from manufacturing BOMs, but these days see more interest in controlling MBOM, MES functions, and everything related to manufacturing process planning. The recent turbulence in the supply chain triggered a lot of interest in the ability of enterprise resource planning systems to mitigate supply chain risks. But to do so is very hard without a detailed connection to product design and engineering processes.
In my view, MBOM is the first and most critical element in establishing a connection between engineering and manufacturing processes. Therefore, MBOM is the place where I recommend starting the simplification process in data and process management.
Here are the top three most important questions to ask about an MBOM when starting the process of engineering to manufacturing data management simplification:
- Is the MBOM accurately and comprehensively detailing every component required for production? This is the primary purpose of an MBOM: to provide a precise, step-by-step guide to assembling the product. It must include every component, assembly, and sub-assembly, right down to the smallest parts.
- Does the MBOM align with the Engineering Bill of Materials (EBOM)? The EBOM outlines the product design, while the MBOM describes how to build it. The MBOM should therefore be a practical application of the EBOM, accounting for real-world manufacturing conditions and constraints.
- Is the MBOM structured in a way that streamlines procurement and production efficiency? The MBOM should not only list components, but also includes all information needed for sourcing, and production planning information including the order in which they’re assembled, potentially reducing production time, minimizing errors, and improving efficiency. It should also consider the layout of the production floor, tooling requirements, and time required for each step.
Remember that a good MBOM is not static, but a living data set. It should be updated regularly to reflect changes in design, supplier details, manufacturing processes, or material availability.
How to make minimum viable MBOM?
I like the concept of minimum viable products in every sense – from real manufactured products as well as thinking about data management processes, optimizing data transfer, and organization communication between systems. Here is my take on 10 important elements of manufacturing BOM you can start with to think about the organization of MBOM.
- Part Details: This includes all the raw materials, parts, assemblies, and sub-assemblies that go into making the final product. Each item should be identified with a unique part number and name.
- Quantity: The exact quantity of each component required for manufacturing one unit of the final product should be mentioned.
- Sequence of Assembly Process: It’s important to list the order in which components are assembled. It includes what components order in the assembly.
- Routing Information: This is the detailed manufacturing process that needs to be followed to assemble the product, including operations, machines, tools, and labor.
- Version/Revision Information: The version or revision level of each part or assembly should be listed, ensuring that everyone uses the most up-to-date specifications.
- Sourcing (supplier) Information: This might include suppliers for parts and raw materials, along with their contact information, and possibly even pricing or lead time information.
- Link to EBOM or Design: The MBOM should reference the corresponding Engineering Bill of Materials (EBOM) data such as design documents, production documents, etc. It is usually can be linked (or attached) in the way of files (eg. STEP) or connected to your EBOM management system. This provides a connection between the engineering of the product and the built product.
- Phantom Assemblies: Usually debatable if need to be included, I found it often to include them because they represent an assembly process. Phantoms are used for sub-assemblies that are immediately used in the next higher-level assembly and not stocked or treated as an independent parts.
- Scrap Factor: It is a factor used for ordering planning. Some parts require usually a larger input quantity to yield the required output quantity, this should be noted in the MBOM.
- Manufacturing Notes or Instructions: This includes any additional information that could be helpful in the manufacturing process, such as safety precautions, quality checks, or special handling requirements.
What is my conclusion?
How to connect two processes efficiently – engineering and manufacturing. This is all that MBOM is about. How to find what components are required for manufacturing, including all assembly processing steps and all materials, such as packaging materials and documentation. it is about accurate data transfer from engineering BOM to production and procurement planning.
From my experience, priority on MBOM can give a big ROI in PLM implementations because it streamlines the connection between the two most important processes in every manufacturing company. You can think that data magically will transfer from engineering desks, CAD systems, and engineering heads to manufacturing planners, and procurement departments, and you will get everything you need on the production floor for a smooth production process, but you’re wrong. Therefore, MBOM simplification is a starting process or connecting the two most important processes in every manufacturing company, allowing the biggest business return and the greatest simplification of processes.
Just my thoughts…
Best, Oleg
Disclaimer: I’m co-founder and CEO of OpenBOM developing a digital thread platform including PDM/PLM and ERP capabilities that manages product data and connects manufacturers, construction companies, and their supply chain networks. My opinion can be unintentionally biased.