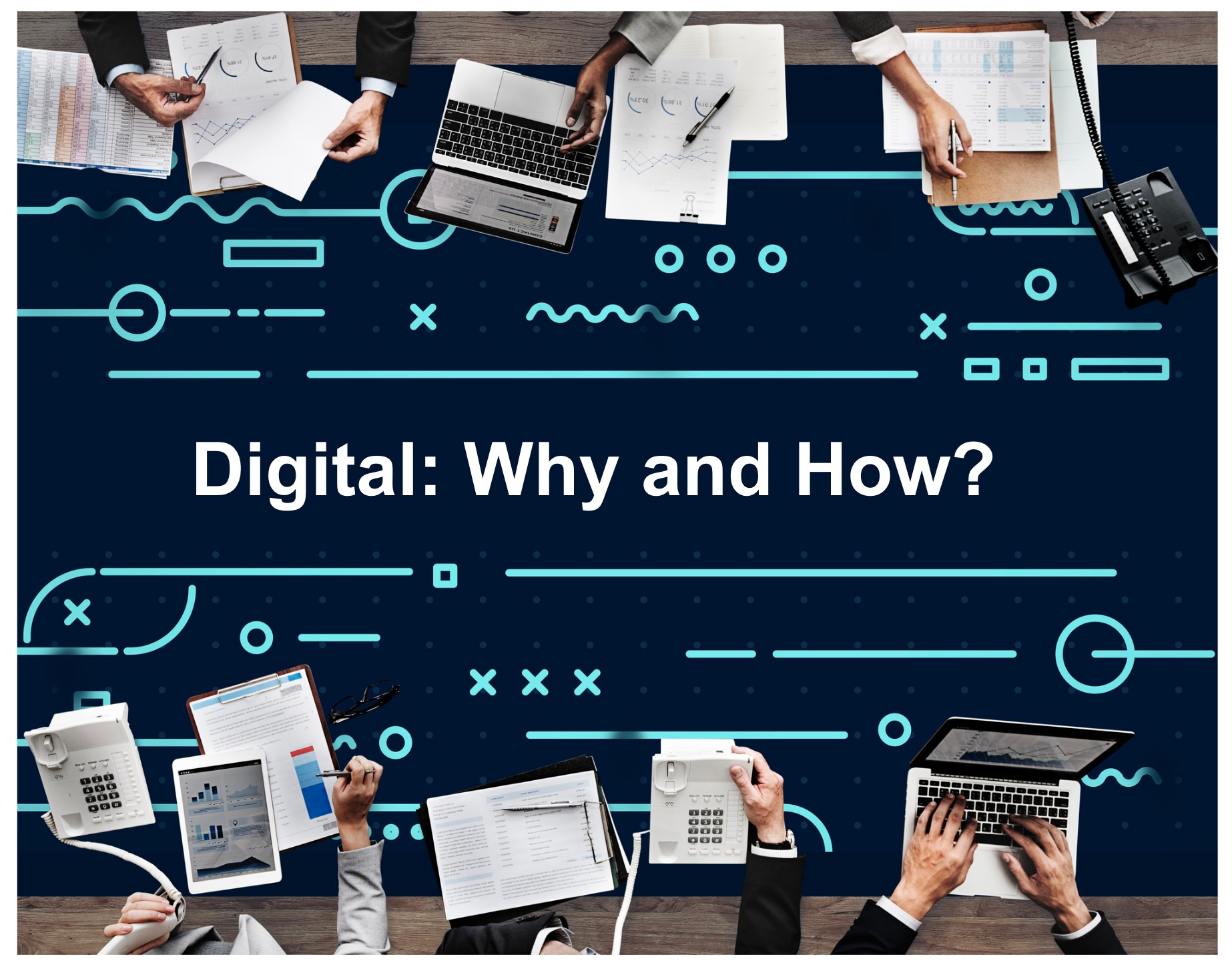
Earlier this week, I published the article Beyond Adoption: Rewiring Organizations to Dominate in the Digital Age speaking about how embracing digital technologies and mindset can change the way engineering and manufacturing companies can outcompete organizations that are stuck in the old way of doing business. The article sparked an interesting discussion online that brought a question of “why” companies need to digital transform their operation and activities.
Here is an interesting passage from that discussion:
Working in the field with companies as an inspirator and motivator for digital transformation in the PLM domain, I see the biggest challenge are the WHY and the HOW questions for each of the checklist bullets. For example, when mentioning Embracing a Digital Mindset, WHY should we? What is the arguable ROI? What if we don’t embrace a digital mindset? Will it kill our business?
Assuming the management agrees that they need to embrace a Digital Mindset, the next question is: HOW are we going to achieve this? By hiring new people in our existing business? By starting projects or buying tools that are currently not in our core flow?
“In an organization, the primary function of the current state is to optimize the current state. It is an immune system, and operational efficiency managers are its T cells.”
Working with many companies, it made me think about how the process of digital transformation can be introduced to engineering teams and manufacturing companies. It made me think about ways organizational can adopt digital tools and change the way they work – optimizing existing processes and establishing new digital processes. Let’s talk about it in my article today.
Why: Better, Faster, Cheaper
The goals of manufacturing companies remain the same for generation. To develop better products in a shorter time while optimizing cost and resources. You can go decades in the history of manufacturing businesses and found the same reason. Those are the same reasons that driving our individual performance progress practically in every task and activity in our personal life and business functions.
The easiest way to answer to the question “why” is to introduce a system of KPIs that can measure the activities and processes. If you cannot measure something, it cannot be managed. Therefore, measuring things like time and cost can be the the easiest way to answer on the question “why” to follow a digital transformation strategy.
But management performance and improving efficiency is not enough. To optimize the work and save time can be important aspects, but working on the right things (instead of wrong things) is even more important. Therefore focusing on the effective organizational change management and effectiveness of the decision process by providing new type of KPIs, capturing right information, customer feedback and many other factors can be part of digital transformation strategy as well.
How: From Tools to Processes
In our personal life, using navigation tools was a better way to find a way to move from point A to point B. In the same way, using digital tools to optimize document management was a better way to than using paper folders. In the same way, using first CAD systems that digitized drafting process was focusing on the efficiency of design, which later one expanded to 3D and provided a faster way to design.
Here is where complexity starts kicking in the way companies’ decision to adopt tools and optimize the processes. While it is easy for a single individual to decide about usage of a tool that brings a better performance, organize information or a process, the things are getting more complex when it comes to an organization with multiple teams, processes, goals and constraints.
Here are a few examples: file revision control, design review and new product development and prototype management.
Engineering file management and collaborative work is a great example. It was one of the first processes PDM/PLM tools were invented to solve. File management and engineering release remains one of the most important mechanism to manage information in a digital form and organize a digital process to approve the work and releases. Design review is another one. Compare receiving of dozens of pages with CAD screenshots as a powerpoint and sending it to multiple people. It is extremely inefficient. At the same time, think about a system that shares CAD data and orchestrate people review process. My third example is new product development that requires orchestration of multiple engineers of working together on different disciplines, creating product structure with multiple BOMs organizing mechanical, electrical and software systems, making assessment of cost, organizing suppliers orchestration and following the process of procurement. You can think about doing it using Excels files and Emails, which will be extremely inefficient. Instead you can think about modern digital environment capturing information automatically and connecting process in a digital pipeline.
It is important to understand that adopting of digital tools and technologies by individuals is easier than doing the same by a company where you need to adapt the process for multi-users and sometimes for multi-company performance. It requires optimization of business processes and this is why introducing organizational change management is really important for setting up digital transformation strategies and digital transformation initiatives.
Why To Bring Digital Transformation in PLM?
Focusing on organizations performance and ability of engineering and manufacturing organization to innovate, here are my four WHY digital transformation initiatives are important:
Improved Collaboration: Traditional processes often characterized by siloed data and fragmented communication channels. Digital transformation in PLM enables real-time collaboration among cross-functional teams regardless of their geographical locations. Cloud-based PLM platforms, for instance, facilitate seamless sharing of product data and enable stakeholders to work concurrently on design iterations, leading to faster decision-making and reduced time-to-market.
Enhanced Innovation: Digital tools are changing product development processes. By leveraging these technologies within PLM, companies can conduct virtual prototyping, simulate product performance under various conditions, and gather valuable insights from big data analytics. This fosters innovation by enabling engineers to experiment with designs, anticipate potential issues, and iterate rapidly without the need for physical prototypes. Modern tools capable to summarize and organize information can make real difference for engineering organization.
Streamlined Operations: Digital transformation in PLM streamlines and automates many manual processes, eliminating inefficiencies and reducing errors. For example, automated processes such as design review, engineering change, advanced supply chain analytics can ensure that design changes are seamlessly communicated across departments, while integration with enterprise resource planning (ERP) systems enables smooth data exchange between PLM and other business functions such as procurement, manufacturing, and sales.
Customer-Centricity: In today’s era of customization and personalization, understanding and fulfilling customer needs is paramount. Digital PLM solutions facilitate the collection and analysis of customer feedback and market trends, empowering companies to tailor their products and services accordingly. By incorporating customer insights into the product development process, businesses can deliver offerings that resonate with their target audience, driving customer satisfaction and loyalty.
How to Embrace Digital Transformation in PLM?
Let’s move to the last part, which is the hardest. How to introduce digital transformation efforts in the organization that focused on optimizing of its current status quo.
Define Clear Objectives: Start by clearly defining the goals and objectives of your digital transformation initiative. Whether it’s accelerating time-to-market, reducing costs, or enhancing product quality, having a clear KPI can help to define where you want to go. It can shortening the time for new product development, reduce supply chain risks and cost optimization. It must be measurable and not abstract.
Invest in Robust Technology: Selecting the right technology stack is crucial for successful digital transformation in PLM. Evaluate different PLM software vendors based on factors such as scalability, flexibility, ease of integration, and support for emerging technologies like artificial intelligence (AI) and Internet of Things (IoT). You should consider whether an on-premises, cloud-based systems are needed and compare the functions and technical performance.
Cultural Shift and Change Management: Digital transformation isn’t just about implementing new tools; it requires a cultural shift within the organization and commitment of key stakeholders. Encourage a mindset of continuous learning and experimentation, and provide adequate training and support to employees as they adapt to new processes and technologies. Effective change management practices will minimize resistance and foster a culture of innovation and collaboration.
Iterative Approach: Digital technology and transformation in PLM is an ongoing journey rather than a one-time project. Adopt an iterative approach, starting with small-scale pilots or proof-of-concepts to test new technologies and processes before scaling up. Continuously monitor and evaluate the impact of digital initiatives, soliciting feedback from stakeholders and making adjustments as needed to drive continuous improvement.
What is my conclusion?
Modern digital technology introduces an amazing new paths to change the way we work as individuals and organizations. Focusing on the right KPIs can help to answer questions WHY the organization need to do so and brining right technologies and brining organizational change will help you to figure out the process. Companies need to find their digital transformation leaders capable to lead these activities and prevent companies from being stuck in long strategic debates about preserving an existing status quo. Just my thoughts…
Best, Oleg
Disclaimer: I’m co-founder and CEO of OpenBOM developing a digital-thread platform with cloud-native PDM & PLM capabilities to manage product data lifecycle and connect manufacturers, construction companies, and their supply chain networks. My opinion can be unintentionally biased.