
Manufacturing companies are continuously looking how to improve business processes, bring new business models, and accelerate new product development and innovation. These days it is directly connected to establishment of a digital transformation strategy and digital transformation initiatives. It helps to companies to focus on specific aspects of the business such as an example supply chain management, but not only.
Digital technologies are in the center of these processes in manufacturing sector. The article published by Prof. Martin Eigner last week – The Constant Conflict Between PLM and ERP made think again about a series of my earlier blogs about “PLM vs ERP wars”. You can get them all from the link to the last blog in this series – PLM vs ERP: how to achieve the synergy? which is resonating with the top of discussion proposed by Martin Eigner and examples of visionary implementations of knowledge graph and digital thread shared by him in the article.
In my article today, I want to speak about how existing technologies can be connected with the vision of building connected information processes and to provide decision support.
A Vision of Connected Data
An idea of connecting data in a complex engineering and manufacturing environment is not very new. I can follow the conversations about them for the last 10-15 years that started from data integration, federated databases, semantic search, many others. Back in those days, I presented a system of links that can connect data located in multiple systems.
A long time ago, I was talking about semantic of connecting product data during my KMWord presentation. In the solution I presented, the user can navigate between connected pieces of data. The system indexes and makes available data from CAD systems and 2-D drawing objects. In addition, the system automatically locates and links to product and engineering information in Excel tables, engineering databases, product data management systems and other enterprise applications.
Martin Eigner presents a graph based view of different BOM types, which allows to connect multiple silos of information and the ability of companies to integrated information streams that stand behind these data structures.

In the same articles, he speaks about the prototype of building a knowledge graph using RDF and Graph Databases technologies to connect pieces of information and link them together.

This is my favorite passage:
A graph-based approach to modeling the overarching digital thread offers further potential in addition to the extreme performance improvement of recursive procedures. By using attributes for objects and relationships, it is possible to filter and create views of, for example, E-BOM, M-BOM, and S-BOM, while minimizing redundancy throughout the system lifecycle
Organizational and Technological Maturity
From my earlier experiments with semantic data analysis and indexes, I’ve learned that building a successful technology capable to connect complex data in real time, requires mature technological foundation and also organizational readiness to create connected processes.
I think, for the last decade, we’ve seen both elements of this equation growing up in the maturity. As such, data management technologies such as triple store, graph databases, ontologies and knowledge graph management tools expanded their capabilities and scalability. In my current business (OpenBOM) we built an infrastructure of data management for engineering and manufacturing data, including capabilities to manage connected data sets and processes.
The vision behind the knowledge graph creation and implementation of integration and processes to manage connected data sets using multi-tenant SaaS platform using Neo4j database, microservices architecture and multiple data management allows to create a flexible data objects and connect them together. Check my article for more details.
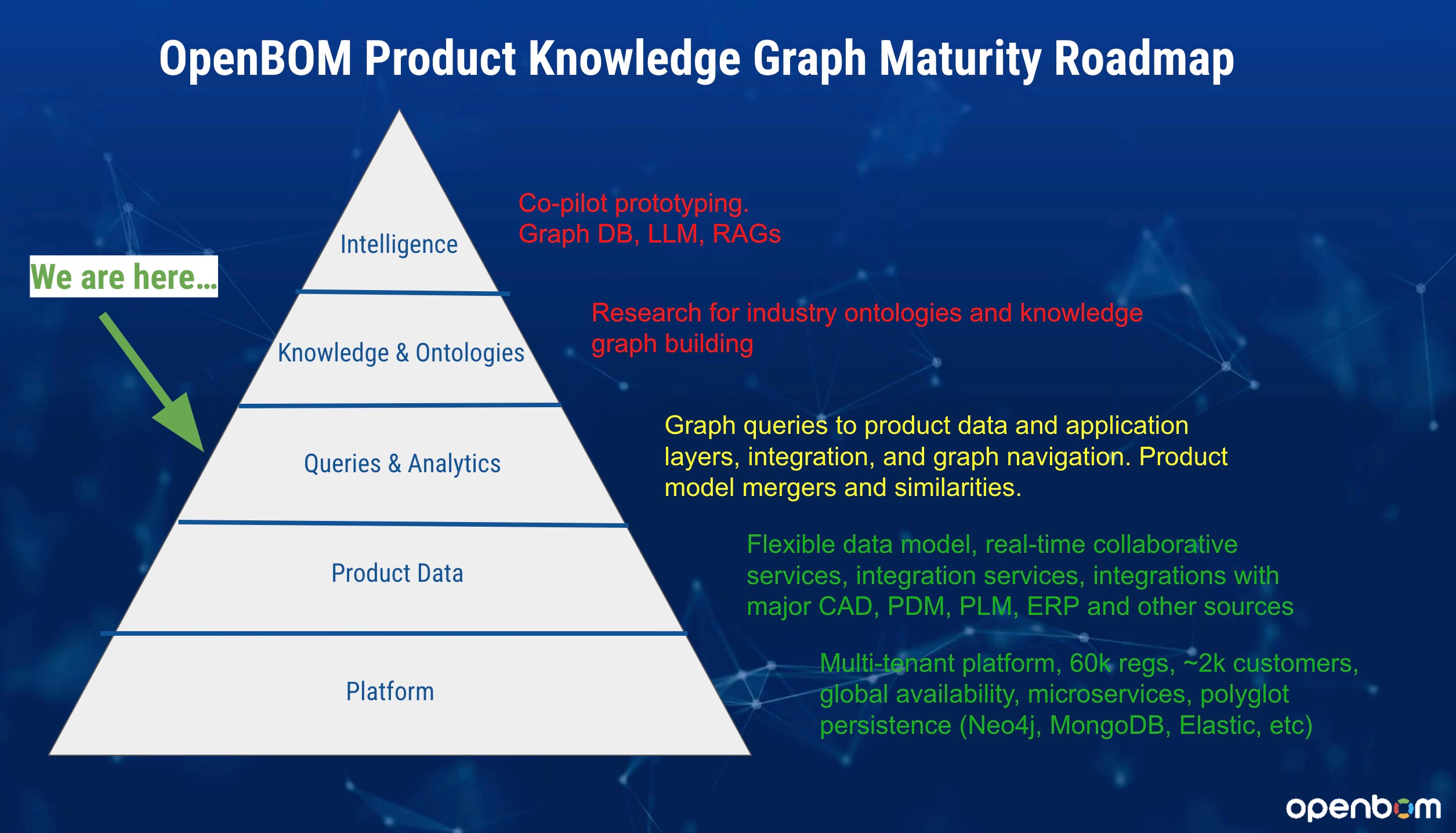
From an organizational perspectives, companies are growing in their understanding of the need to create a holistic model of information processes. And it is very much can be applied to engineering and manufacturing business.
In the rapidly evolving world of manufacturing, the integration of data from Enterprise Resource Planning (ERP) and Product Lifecycle Management (PLM) systems represents a significant opportunity for businesses to enhance their operational efficiency and strategic decision-making. By opening up and connecting data across these platforms, manufacturers can unlock a wealth of benefits that drive innovation and competitiveness in the market.
PLM and ERP: Connecting Blueprint
Before digging into the connecting vision and process, it’s important to understand what ERP and PLM systems are and the roles they play in manufacturing. ERP Systems manage and integrate the essential parts of a business, including planning, purchasing inventory, sales, marketing, finance, human resources, and more. PLM manages every aspect of a product’s lifecycle from inception, through engineering design and manufacture, to service and disposal of manufactured products. Both systems handle critical information that, when effectively integrated, can lead to a more streamlined, efficient, and productive manufacturing process.
Although, as it was explained in Martin’s article, companies are different methodologies and scenarios of role separation, it should not change the principle mechanisms of developing an connected data management and user experience.
Step 1: Establish a Clear Data Governance Framework
The first step in opening up data from ERP and PLM systems is to establish a robust data governance framework. This framework should define who can access the data, how it can be used, and the security measures that will protect it. Data governance ensures that data is consistent, trustworthy, and doesn’t violate any privacy regulations.
The foundation of this framework is defining attribute sets, data schemes, product models and ontologies to support them.
Step 2: Implement Data Integration Tools
Integrating data from ERP and PLM systems can be challenging due to differences in data formats and structures. Implementing modern data integration tools can help. These tools can automate the extraction, transformation, and retrieving data, ensuring that data flows seamlessly between systems without losing its integrity.
Step 3: Create a Unified Data Model
To effectively analyze and utilize the data from ERP and PLM systems, creating a unified data model is essential. This is a place where we are now. This model will serve as a blueprint for how data from disparate systems can be combined and analyzed to provide meaningful insights. There are different approaches that used in the past to build a “unified models”. Some companies built product models using industry standard frameworks and some others embarked on proprietary tools (eg. PLM platforms).
What I can see a very promising approach is to lower the common data modeling denominator from industry specific to technological enabler and at the same time, keep the high level of flexibility and openness. I spoke about it in my article about graph based product models.
Step 4: Leverage Advanced Analytics and AI
With a graph based data model in place, manufacturers can apply advanced analytics and artificial intelligence (AI) to this integrated data. These technologies can forecast trends, optimize workflows, and enhance decision-making. For example, AI can be used to predict machine failures before they occur, significantly reducing downtime and maintenance costs. It is a very interesting trend and I expect to see more examples of this in the near future.
Step 5: Foster a Culture of Continuous Improvement
It is important to keep the process of improvement. The outcome of opening PLM and ERP data is not a single moment event, but an ongoing process that requires continuous monitoring and improvement. It’s crucial to foster a culture where continuous improvement is a key goal. Regularly updating systems, training staff, and adopting new technologies are all essential for maintaining the efficacy of your data integration strategies.
Start with “Why”
It came in many recent discussion that “start with why” is an important business topic. While integrating data can have a specific technological and product outcome, we should remember and built a model for business to leverage this outcome. The benefits of integrating and opening data from ERP and PLM systems are manifold:
- Enhanced Collaboration: Seamless data flow between departments can lead to better collaboration and innovation.
- Increased Efficiency: Automated data flows reduce manual entry errors and free up employee time for more strategic tasks.
- Improved Decision Making: Real-time data provides a comprehensive view of the manufacturing process, enabling more informed decision-making.
- Scalability: With integrated systems, scaling your business operations becomes much easier and more manageable.
What Is My Conclusion?
The future of manufacturing lies in the ability to effectively integrate and utilize data from all corners of the enterprise. Starting from two key systems such as PLM and ERP can put a critical foundation into this technology and process. Opening data from ERP and PLM systems to connect processes not only optimizes decision support but also prepares businesses to meet the challenges of the future with agility and confidence. By following these steps, manufacturers can ensure they are making the most out of their digital transformation efforts.
Just my thoughts…
Best, Oleg
Disclaimer: I’m co-founder and CEO of OpenBOM developing a digital-thread platform with cloud-native PDM & PLM capabilities to manage product data lifecycle and connect manufacturers, construction companies, and their supply chain networks. My opinion can be unintentionally biased.