A digital thread is a concept in manufacturing and engineering that refers to the seamless flow of data throughout the entire product development and production process. It connects all aspects of a product’s design, engineering, manufacturing, and maintenance, allowing for real-time access to information and enabling rapid decision-making. The digital thread can help to improve collaboration, reduce errors, and streamline production, ultimately leading to more efficient and effective manufacturing processes.
In my previous articles, I shared my thoughts about the digital transformation and the evolution of digital thread implementations starting from meaningful part numbers, a variety of integration technologies, and modern data sharing and federation. Check my previous articles here:
Digital Thread Evolution – Overview
Digital Thread Evolution – Folders, Files, and Part Numbers
Digital Thread Evolution – Enterprise Integrations
Digital Thread Evolution – Data Sharing and Federation
In the article today, I want to talk about what I see as a promising future of digital thread implementations that is also inspired by the future architecture of PLM systems.
The next step in Digital Thread evolution will be the creation of knowledge graph-based systems capable to display information about products in a semantically connected way.
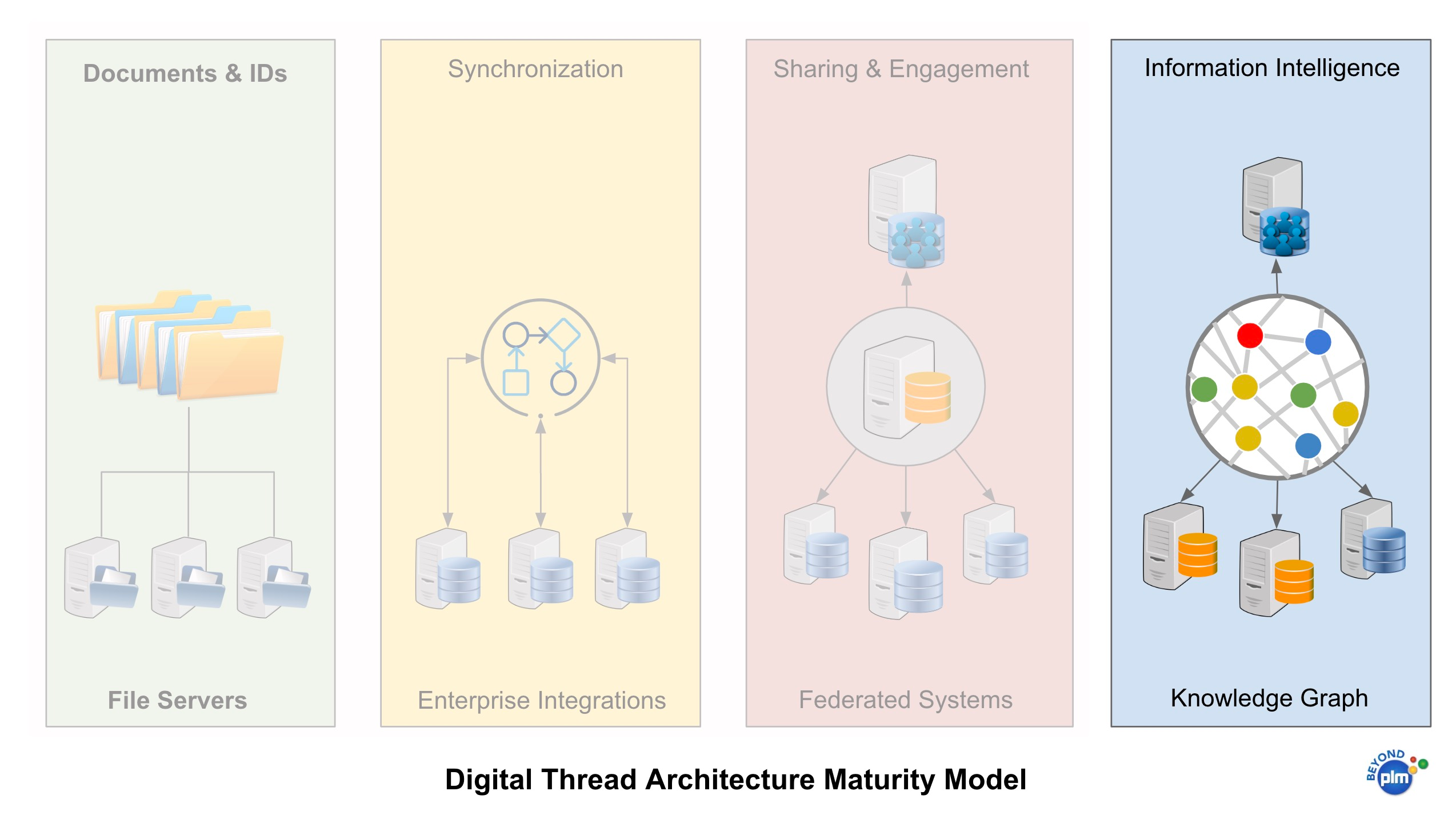
Let’s talk about how I think, the industry will move from traditional legacy enterprise PLM systems to modern PLM knowledge-graph-based systems.
Breaking PLM Monolithic Architecture
All existing mature PLM systems are built as monolithic enterprise systems. And they are hard to work with. This complexity is due to the fact that these systems contain large numbers of components that are tightly coupled together. They are built over time, complex and when changes need to be made, they affect all other parts of the system and cannot be done in isolation. Additionally, all monolithic PLM systems are highly complex and require significant levels of expertise to understand how the different components interact with each other.
Another challenge of legacy monolithic PLM systems is that due to their size and complexity, these systems can be difficult and time-consuming to maintain over time, as any updates must be rolled out across all components in the system at once. It causes release locks and challenges to upgrades.
Flexibility (or actually lack of flexibility) is another problem with legacy PLM systems. This makes them more difficult to customize and adapt when new requirements arise or the organization’s direction shifts. It also means that introducing new functionality or services may require significant re-engineering effort if existing components need to be replaced or adapted in order for them to accommodate the changes. All of this can lead to considerable expense and disruption for organizations that rely on such systems for their core business operations.
In recent years, microservices architectures are fast becoming a popular way to replace legacy monolithic systems. New microservices-based systems are coming to enterprises and targeting PLM systems as well. I want to point you to a few articles about breaking monolithic PLM systems.
From PLM monoliths to Federation and Data Mesh
PLM systems and future PLM scalability
5 Steps To Break PLM Monolithic Applications
In my view, breaking PLM monolithic architectures will become the next big trend in PLM system evolution and the digital thread will play one of the key elements. Companies are looking into how to create an interconnected system capable to manage larger and more connected data sets, stepping away from traditional “single SQL database” storing all information.
Knowledge Graph and Semantic Networks
A knowledge graph is an interconnected set of data points that uses machine-readable links to connect related pieces of information. This type of graph is designed to help computers gain a better understanding of the semantics and context of data. Knowledge graphs are used by organizations to organize, analyze, store, search and visualize information that is connected in some way.
I’ve been following knowledge graphs for the last decade since making the first appearance as a Google knowledge graph and later in many other applications and systems. Check my Beyond PLM articles about knowledge graphs.
Digital thread requires building connections between data, workflows, and applications. Therefore, the opportunity of semantic technologies and knowledge graphs is to play the role of medium where systems can store data and relationships. Also, a connected knowledge graph is a foundation to build business processes capable to flow across multiple business systems and companies. Such digital technology can be efficient in organizing information and providing a source of data that can be used in product development business processes and supply chain management.
The following picture shows you how the PLM system of the future can be used to organize a semantic meta-layer in the entire manufacturing product graph

The value proposition of a manufacturing graph is in the transformation of all data sources and silos of every type into the form of a knowledge graph. In the beginning, you can count on a subset so of data (Eg. Engineering and manufacturing bill of materials and connected information). As the system will be future-developed, the full spectrum of data will be explored and transformed into a graph model.
Digital Thread and Information Intelligence
Intelligence is in the air these days. Everyone is looking after how to capture the right data and turn it into intelligence. We can see it is happening in many business processes and systems. PLM vendors are not staying out of the “intelligence trend” and looking at how to use data to build future engineering and manufacturing intelligence.
A system of intelligence that can be used for decision-making is the future of the PLM industry that allows vendors to use an entire set of information captured into the knowledge graph. Check my earlier article – From System of Record to System of Intelligence.
Data is quickly becoming one of the most critical elements in many organizations. The amount of data produced by manufacturing companies is huge and all companies are asking questions about how to turn the data into a source of intelligence. In my article – PLM Data Intelligence In Manufacturing I discussed how in the future we can see online services playing a role of a center of intelligence for modern manufacturing organizations and supply chains.
Another Forbes article – From System of Records to System of Intelligence speaks about how digital transformation can be supported by a new type of technologies focused on the data and producing better insight and decision support. Check our – Moving Value: From System of Records to System of Intelligence.
The premise of a system of intelligence is beyond traditional data warehouses and analytical systems. The business case for these (SOI) systems is to take the idea of data intelligence and make it part of the system of records (SOR) eliminating the separation between systems. Old school data warehousing required the separation between systems of records and DW. A new system of intelligence does everything in real time because they are part of data management (system of records). The new system of intelligence will bring real-time analytics to old fashion enterprise systems by providing advanced data management methods, collecting and analyzing data, and replacing old school systems of records.
There is a strong business case to establish a PLM system of intelligence based on the new architecture of the system of records. Over time, a system of intelligence will provide a sustainable strategic digital differentiation with the ability to improve decision support.
What is my conclusion?
Digital technology is coming to the PLM domain. It is part of modern digital transformation initiatives for many manufacturing companies these days. The use of the knowledge graph, semantic networks, and multi-tenant, distributed PLM applications are allowing for the advancement of digital thread development. By connecting data and building intelligence and decision support systems we are able to create invaluable new solutions for the manufacturing industry. It allows connecting engineering, manufacturing, and supply chain data and processes together. It is an interesting time for digital thread development and future advancements can be seen on the horizon for future PLM development. It is also an opportunity to bring intelligence to the manufacturing space. Companies should be considering product lifecycle management strategies to implement this technology. Just my thoughts…
Best, Oleg
Disclaimer: I’m co-founder and CEO of OpenBOM developing a digital cloud-native PDM & PLM platform that manages product data and connects manufacturers, construction companies, and their supply chain networks. My opinion can be unintentionally biased.