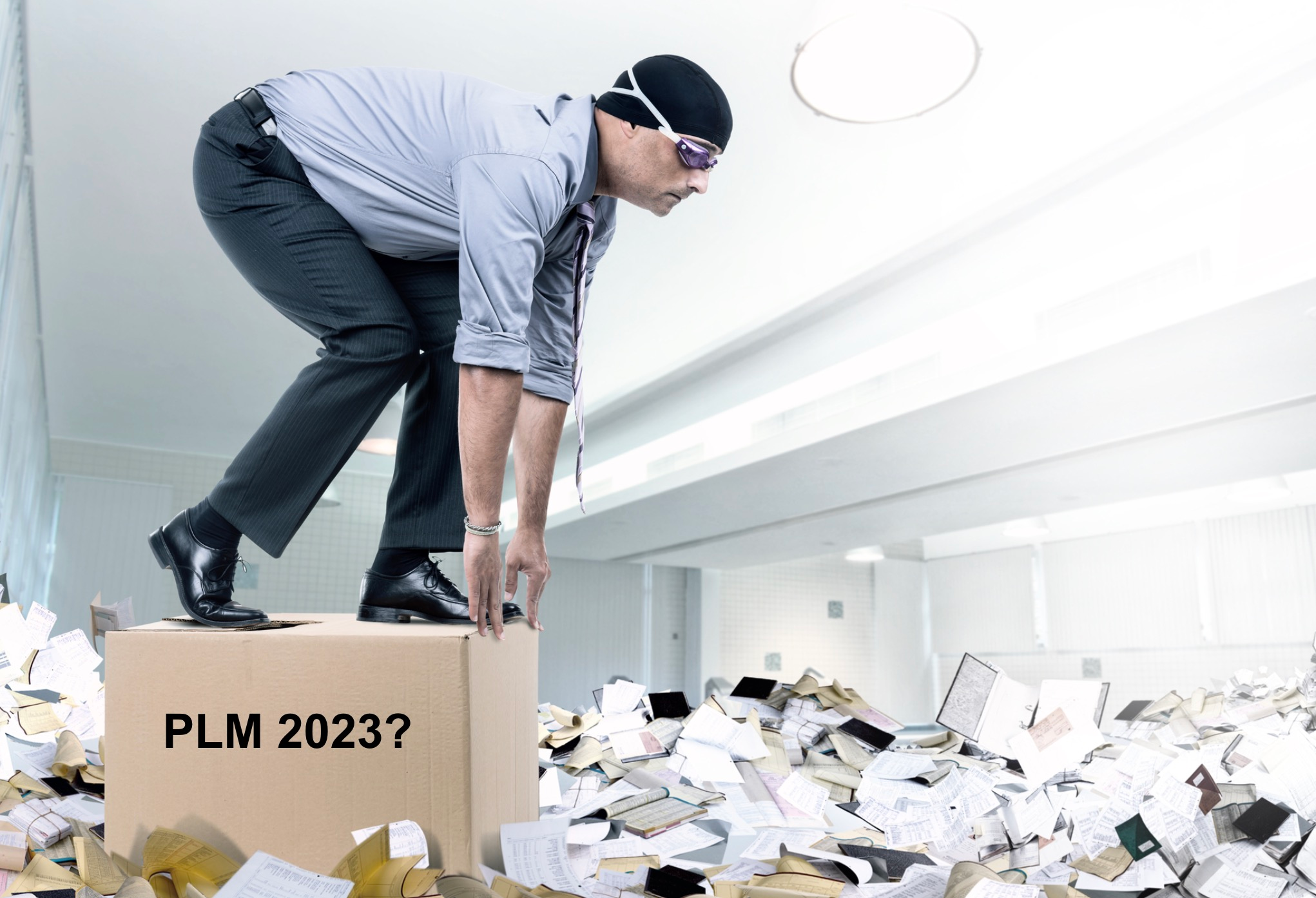
It is 2023 and every manufacturing company in the world understands that digital transformation is the name of the game. Remember a decade ago conversations about manufacturing and cloud? The game is over. If you want to survive in a digital world, you need to learn how to be digital. Dr. Covid-19 was the biggest acceleration factor that explained to everyone in the business world that relying on old fashion habits of running a business like it in 1995 doesn’t work. I remember watching companies back in 2020 asking questions about how to access their drawings that were locked in company servers without VPN and also hearing many companies that were looking to find alternative suppliers but had a hard time scrambling the full documentation about their product for RFQ to share. I know many of your that reading this blog now thinking… how many Excel spreadsheets with BOMs do I have to screen to find the one I need to send to my contractor and how to calculate the cost of a new product model I have in the development process right now. This is only a small list of questions, I’m sure each of you has your own thoughts.
How to Choose The Platform?
While everyone understands that product lifecycle management, product data management, enterprise resources planning, and supply chain management are the answers, the question of choosing the right platform to fit your business strategy is not the simplest one. Public reviews are one of the ways you can start your selection process. Navigating to G2 PLM Vendors will give you a list of almost 100 vendors. But which one is the right for your business and development process? The list of ERP systems is literally endless. In my business, every day I learn the name of another ERP/MRP system that is used in a specific industry or market. Everyone at least once heard horror stories of PLM implementations. As a manufacturing company looking into the process of selecting the right solution how to find an unstoppable PLM implementation strategy?
The choices are probably running through your head – (1) Should we choose a proven product and large brand; (2) what is the right size, maybe we still can survive without PLM; (3) those PLMs really crazy, and complex, maybe my SharePoint and a fancy spreadsheet are enough; (4) should we select cloud or on-prem solution; (5) how to integrate all my processes and communication with contractors and supply chain. If you’re asking all these questions, you’re not alone. And this is just a short list of questions.
What comes next in every company is usually called an “evaluation process”. It is part of the PLM selection process that can be supposed to identify the best system. The challenge of all these processes is that when it comes to product lifecycle, business processes, and designing and building products, the environments are very complex and you need to get people from various departments and disciplines to get involved. It is hard and requires a lot of communication about both requirements and preferences.
Most companies these days are intelligent enough to run a PLM selection and evaluation process. And many people can easily get confused. Therefore, before jumping into details, I always recommend starting from the basics. Check my article – Top 5 Questions About Product Lifecycle Management.
5 Characteristics Of PLM For Digital Transformation
PLM technology was around for the last 25+ years. It started with the management of CAD files and expanded into engineering disciplines. In fact, if you look into the last CIMdata market research, you can find that most PLM implementations still focus on traditional PLM topics – engineering data management, release and change management, and configuration management. Check My top 5 important things about the state of PLM in 2023 (based on the CIMdata market forum).
So, if you’re looking at how to transform your organization, you should be carefully looking at products that developed 2-3 decades ago. I always recommend taking a fresh look around and checking what manufacturing companies and the PLM industry learned over the last 10-15 years from companies building online digital businesses. Read my Post-monolithic PLM world – data and system architecture.
Here are the top five things that I recommend to check when you’re approaching the selection of a PLM system for your digital transformation project.
Cloud-based (global availability)
Regardless of what lessons you learned from COVID, and independently about what you think about going back to the office, manufacturing projects are involving people located everywhere these days. Companies hire engineers based on skills and not on location. The product development process goes non-stop 24×7 in different places in the world. Customers are using your product everywhere (think maintenance). The list can continue. You really (seriously) don’t want your product development process dependent on servers and local access in a specific office. Note: there is a serious question related to regulated industries. I will address it separately.
Multi-tenant (support multiple companies)
Old PDM/PLM systems were developed to be used by a single company. In fact, all 20-30 years old PLM systems are in fact a “single database” system architecture. Those systems were born before the digital era and their architecture was a single tenant and not assuming that two companies can use the same system independently and communicate efficiently. In a single tenant system you either convenience everyone in all companies (Eg. suppliers and contractors) to login to the same system or you need to do export/import (or any other forms of ETL export-transfer-load functions). Modern multi-tenant systems allow to companies to connect seamlessly and share data in real-time.
Multi-disciplinary data management
Modern digital products are complex and contain mechanical, electronic, and software pieces. You don’t want to have a product lifecycle management system for mechanical design and a separate system for PCB and then think about how to connect all these pieces. Check how systems can support a multi-disciplinary design and product development process.
Data modeling flexibility
One size doesn’t fit all. Therefore companies are looking for flexibility allowing them to manage different sets of information and define their own attributes, objects, relationship types, and other elements of data that are needed for efficient product lifecycle management. A system with flexible data modeling capabilities provides a clear competitive advantage compared to so-called out-of-the-box systems that cannot be changed. The right balance is needed, but when you evaluate a system, check how new data modeling elements can be added or changed.
Standard integration capabilities (REST API)
Systems do not live alone in a modern digital world. Connectivity is key and therefore, you need to check for the ability of systems to integrate. REST API is the de-facto standard. Every manufacturing company today has software engineers that can quickly connect systems and data using REST API. Therefore, API must be on your checklist.
3 things To Avoid in 2023
Before you embark on your product lifecycle management platform selection process, I want to share with you my “no-no list”. If you see one of these three things during the system evaluation, I recommend you to quickly run away.
- Major functions of the system cannot run in the browser and require installation
- A proven old system with no clear visibility on system updates and security patches
- No REST API and no integration with engineering tools with the proven roadmap of upgrades
What is my conclusion?
Selection of product lifecycle management (PLM) systems and technologies is a complex process that requires consolidation of all your requirements and following the needs of multiple people in your organization. You need to think strategically, but also you need to think about the learning process in your own organization. The most important thing is to bring product and technology that fits your organization and processes. Your organization and processes will evolve and your product lifecycle management tools will evolve together. The main thing you should think about is the product life cycle and how to support data quality and product data consistency in your organization. In 2023, it all starts from data, your ability to manage data you need in the product development process, and your ability to streamline information flow and processes. Just my thoughts…
Best, Oleg
Disclaimer: I’m co-founder and CEO of OpenBOM developing a digital thread platform including PDM/PLM and ERP capabilities that manages product data and connects manufacturers, construction companies, and their supply chain networks. My opinion can be unintentionally biased.